Increased demand for quick and reliable fulfillment is putting added pressure onto warehouses and distribution centers to prevent supply chain disruptions from lag in data, equipment failure, and design processes.
Material Handling Trends Require the Need for Speed
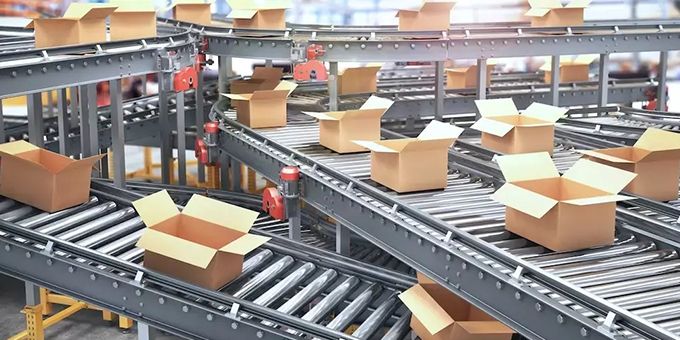
Article from | Rittal North America LLC
The scalability of modular enclosures plays an important role in accelerating facility growth, allowing for agility and expansion, and supports the adoption of Edge computing to warehouses and distribution centers. Climate control within enclosures helps to ensure reliability and uptime of the equipment as they provide a constant temperature, therefore they are the best prerequisite for a long service life and high reliability of all the electronic components within an enclosure. Consumers are increasingly switching to online ordering with the expectation that deliveries will be made quickly. This trend is being adopted by manufacturers, retailers, and end users alike – the need for speed is apparent for all.
Increased demand for quick and reliable fulfillment is putting added pressure onto warehouses and distribution centers to prevent supply chain disruptions from lag in data, equipment failure, and design processes.
Trends and challenges in the material handling environment
- Logistics companies are switching investments from traditional brick and mortar retail to investing in warehouses.
- The transition to distribution centers and warehouses is driving an increase in automated solutions to support 24/7 order picking and product distribution.
- Sourcing skilled labor in this environment has been heightened by the effects of the pandemic.
Solving the pressures and challenges facing the e-commerce boom
Facilities are rapidly adopting automation solutions, and Edge computing goes hand-in-hand to support the data needs. Human Machine Interfaces (HMI) are rapidly growing which is leading to an increase in robotic processes. For many manual processes such as cycle counting or picking, robots are now performing the tasks. These robots depend on complex server networks and Edge systems to keep them operational, generate work orders and packing slips, and manage the logistics within the warehouse. This transition supports the 24/7 demand and helps to solve the limited availability of skilled workers. These technologies can further lead to increased productivity, reduced human errors, and enhanced safety throughout the facility as workers are not doing repetitive tasks or lifting heavy objects.
Warehouses contain a lot of steel to support the structure. Steel can prohibit internet signals that traditional data centers rely on. Logistics leaders have had to move away from these data centers in favor of local solutions. The adoption of decentralized solutions, having many data centers throughout the world, is needed to support the high data demands of automation. Facilities can receive and interpret data at the source when and where it is most needed.
Bringing data to the source to support rapid growth
Historically data centers have been centralized to manage data at a hyperscale level. Industry 4.0 and IoT have increased resource demands that require faster processing time. Moving to a decentralized data solution creates the reliability needed for real-time reactions to data.
Warehouse and distribution centers that have been operating for decades need to be revitalized to address the need for flexibility. This is evident as companies expand, technology and automation increase, and consumer expectations change. Additionally, there is more consolidation in this industry with large companies acquiring small companies. The infrastructure of the small companies tends to be limited and where improvements are needed to meet the new standards.
Providing real time data is essential for rapid growth. Whether it’s powering systems throughout the facility or analyzing operations, bringing data closer to the source is necessary especially as consolidation and expansion continue. Implementing Edge solutions allow facilities to have more control over their operations by having data at their fingertips. Facilities are empowered to make more informed decisions and can better support the addition of automated processes to support 24 / 7 operations.
Security and monitoring to keep everything safe
The final piece of the Edge deployment is to ensure the highest level of physical security and to be able to monitor environmental parameters and control access to the Edge installation. The CMCIII system is designed to provide these needed capabilities at the Edge.
A range of environmental sensors including temperature, humidity, vibration, and leak detection can be easily installed in the Edge footprint. Enhanced electronic access control - electromagnetic handles, PIN Pad, or Card Reader access control devices, can also be used to add an additional layer of protection against unauthorized access. The Edge footprint will likely be in a remote location and not be continuously monitored; for this reason, the CMCIII system comes with network communications capabilities using TCP/IP and SNMP protocols. This software provides the remote monitoring and control capabilities critical to securing the Edge installation.
Material handling companies are turning to the TS 8 enclosure system
Designed on the premise of not knowing what the market is going to need due to the amount of change and customization occurring; the TS 8 enclosure offers the modularity, flexibility, and scalability needed for the demanding environment. It is built to meet a full range of applications, manufactured to take standard products, and assemble them into a variety of configurations allowing for a custom solution. Additional benefits include:
- Front-to-back and side-to-side baying – providing additional depth, width, and usable space without a traditional complete custom solution
- Option to add side canopies that can be turned into disconnects for high voltage applications
- Bay enclosures together to create multi-door enclosures or a complete system
- Change the configuration to fit application needs – one enclosure can do the job of multiple
Roles and benefits of EPLAN Pro Panel
Designing control panels can be challenging especially when working in a disconnected system. Changes can cause delays and increase costs. Switching to a fully integrated solution such as EPLAN Pro Panel allows you to design your control panels and send the schematics across teams to ensure accuracy. If changes are needed, you make your updates within Pro Panel and all downstream stages are easily updated.
EPLAN Pro Panel helps to reduce manual and administrative work. It eliminates the need to look through catalogs for replacement parts and stores all data needed at every stage.
- All design and part information stays connected including necessary details for maintenance, repair, and operations
- Drag and drop components directly into the design
EPLAN Pro Panel provides instructions of the plan to the customer, maintenance details and alternate products, and the life expectancy of controls. These details provide all parties with key information to make informed decisions on short- and long-term costs and provide key details to the maintenance department so they understand the components inside the control panels. If there is a problem with any part, information on exactly how to replace and with what part is clearly defined.
Historically, parts information can be lost; to counter this, maintenance is likely to preemptively order products for the possibility of a future need. While this helps to ensure the product is on hand, it also ties up capital for products that may become lost, damaged, obsolete, or not needed. Pro Panel makes it easy to identify the correct part when it is needed allowing more control over maintenance costs.
Climate needs to power automation
Consumer demands are driving the need for speed across material handling facilities leading to increased power requirements to support automation and real-time data. Enclosures protect critical equipment to support the high demands of 24/7 facility operations.
As electronic controls and equipment needs increase the need for climate control becomes necessary. If electrical control equipment gets too hot, it can fail causing operations to come to an abrupt halt. Unplanned downtime can cause exponential costs. To prevent this from happening proper climate control is necessary especially on the automated side where computers and servers are required to run the facility.
There is an explosion of new distribution centers that are going to OEMs or partnering with integrators and panel shops to build solutions based on scalable models that can be customized for the individual location. The influence of IT and industrial experts and OEMs come together to work with integrators on custom solution designs. For this reason, it is imperative to have solutions to support design flexibility and collaboration to further promote the need for speed across material handling facilities.
Choosing EPLAN as a CAE solution, TS 8 modular enclosures, Blue e+ cooling, and Edge systems support the increased demand of facilities. Each of these solutions provide benefits for facilities including promoting collaboration and increasing design speed, providing the needed flexibility to adapt to future changes, helping to reduce failures by contributing to proper enclosure temperatures, and bringing data to the source for real time information. With Rittal and EPLAN as partners, keeping up with demands is easy and efficient.
To learn more, watch the four-part Need for Speed podcast series today.
The content & opinions in this article are the author’s and do not necessarily represent the views of ManufacturingTomorrow
Comments (0)
This post does not have any comments. Be the first to leave a comment below.
Featured Product
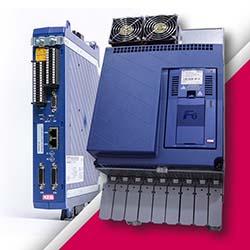