Bringing real-time visibility to entire production, asset performance, inventory, workforce utilization, supply chain, etc. starts by collecting accurate shop floor data.
5 Major Benefits of Data Collection for Manufacturing Companies
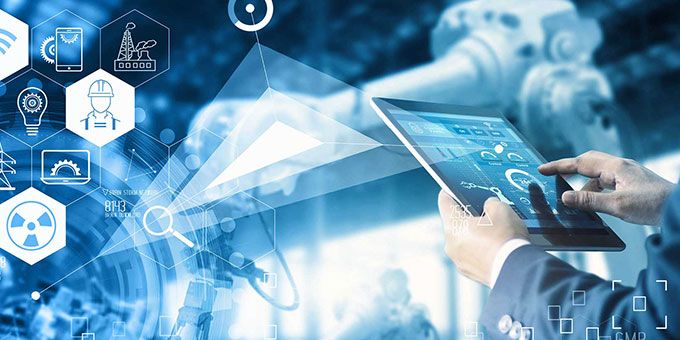
Snehal Joshi, Head of the Business Process Management Vertical | HabileData
With the onslaught of IoT (Internet of Things), Artificial Intelligence and Machine Learning technologies, manufacturing companies are buzzing to become a data-driven shop floor to top floor. To become a data-driven manufacturer, the first step is to capture or collect shop floor data from various segmented legacy systems.
By deploying an automated real-time collection of manufacturing shop floor data mechanism, manufacturers can easily optimize production, performance, profitability and reduce waste. From a highly accurate and standardized stream of data, extracting insights for shop floor equipment, workforce, inventory, supply chain and product quality leads to right decisions.
Key challenges faced by manufacturers in accurate data collection
-
Use of legacy systems and siloed data sources: Traditional systems, equipment, or assets were not primarily designed to talk to each other. Due to use of separate systems among different teams, there is a huge documentation and communication gap. It becomes difficult to consolidate highly unstructured data from multiple disparate systems.
-
Limited budget and aging workforce: Due to a huge labor gap in the market, manufacturers face the rut of aging manual workforce and operating on a limited budget. It fails to assist them in addressing the data needs of a smart manufacturing enterprise.
-
Unorganized data storage: From procurement to production, inventory and operations, manufacturers are heavily dependent on spreadsheets or manually written documents to store records. Such storage methods cannot cope up with the massive rise of data volume.
Without data collection and monitoring, manufacturers have no visibility or control over machine downtime, maintenance schedules, scrap, and performance to production tracking. This is why it is important to have digitized, accurate and real-time production data visibility for all operators, plant managers and engineers.
5 powerful benefits of data collection for manufacturers
Manufacturers can gain a competitive edge by adopting a digital approach to capture or collect shop floor or production data. It also helps them to eliminate data silos and empower MES (manufacturing execution systems).
1. High visibility: Manufacturers can get quick and timely insights on asset performance, workforce utilization, product quality, inventory levels and equipment efficiency. It helps to mitigate unplanned machine downtime, production bottlenecks, and boost factory floor efficiency and productivity.
With a comprehensive data collection across the organization, the decision makers can easily identify individual asset performance, low-performing shifts, and recurring maintenance issues.
2. Establish a single source of truth: Different teams maintain different data records and that too in different formats. With cumulative shop floor data collection, manufacturers are able to eliminate assumptions, guesswork and communication gap between various teams. It saves a lot of time and efforts of different teams to look for right information.
By having a single source of reliable, accurate and accessible production data at their fingertips, employees can collaborate, make critical decisions and respond to changes quickly. Apart from this, maintaining optimum quality across various production stages, aligning products with customer needs and making changes as per market demand is possible.
3. Easy adoption of AI and Machine Learning technologies: Data collection is the first step to become an empowered and data-driven manufacturing company. With large datasets at their disposal, manufacturers can use complex Machine Learning and AI algorithms and IoT enabled devices to:
-
Digitize production
-
Monitor performance
-
Maintain right inventory levels
-
Forecast demand accurately
4. Streamline scheduling to delivery: Accurate data capture at various stages on the shop floor like raw inventory, current production capacity, and estimated delivery, helps to align planning, production, and sales. Manufacturers can understand what the current status of a batch is and if they can easily fulfil customer requests within quoted lead time or not. Plant managers can rely on a detailed history to keep production on track, make commitments and meet established delivery times.
5. Optimize cost savings: With a stupendous rise in labor, transportation and materials costs, manufacturers are always on the sprawl to embrace ways to save money. Implementing data collection can translate to evaluate production processes, bring process improvements, increase output and reduction in scrap; while bringing down the overall costs.
Moving from descriptive or receptive maintenance to predictive maintenance based on real-time notifications and machine conditions also saves unplanned expenditure. Manufacturers who deploy automated data collection methods understand what the need of the market are, customers, and can make changes accordingly.
How does data capture help in various facets of manufacturing operations?
-
Production: Manufacturers have a clear vision about the amount of production to be done on any particular day. To projections and avoid overstocking or under-stocking, they also have correct estimates of raw materials and inventory to meet.
-
Supply chain: As supply chains become more complex, data is stored in different forms as spreadsheets, ERP systems, supplier portals, etc. By streamlining these various data streams, manufacturers can leverage real-time monitoring of shipment, supplier capacity, quality to optimize supply chains.
-
Demand forecasts: Bridge the wide gap between actual sales vs. weekly, monthly or yearly estimations by determining the exact demand of a particular product. Product or location-based forecasts for products can help reduce production losses, too.
-
Maintenance: Use of legacy systems did not provide any visibility on the machine health or impact of factors like temperature, vibration, heat, or pressure on the overall functioning of machines. As a result, there used to several unplanned machine breakdowns. With data visibility, manufacturers can efficiently predict when machines will need maintenance and prevent equipment failure and losses.
-
Sales and customer satisfaction: Data capture helps to understand what customers really want and focuses on increasing product and brand reputation. Manufacturers delivering on time with the required quality can reduce product recalls, too.
Conclusion
To succeed in an increasingly competitive and volatile manufacturing market, data collection tools or software have become more affordable and qualitative. So, manufacturers who want to create tailored products and grab higher market share can start by capturing the right data in the right way and from the right place.
About Snehal Joshi
Snehal Joshi heads the business process management vertical at HabileData, the company offering quality data processing services to companies worldwide. He has successfully built, deployed and managed more than 40 data processing management, research and analysis and image intelligence solutions in the last 20 years. Snehal leverages innovation, smart tooling and digitalization across functions and domains to empower organizations to unlock the potential of their business data.
The content & opinions in this article are the author’s and do not necessarily represent the views of ManufacturingTomorrow
Comments (0)
This post does not have any comments. Be the first to leave a comment below.
Featured Product
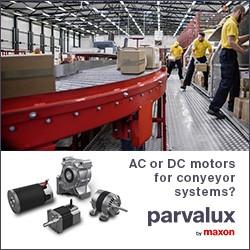