No matter if you are a longtime safety expert or know relatively little about the industry, you have probably experienced a safety inspection or safety audit at some point. But what exactly do these events entail and how can they help your organization?
A Quick Guide to Workplace Audits and Inspections
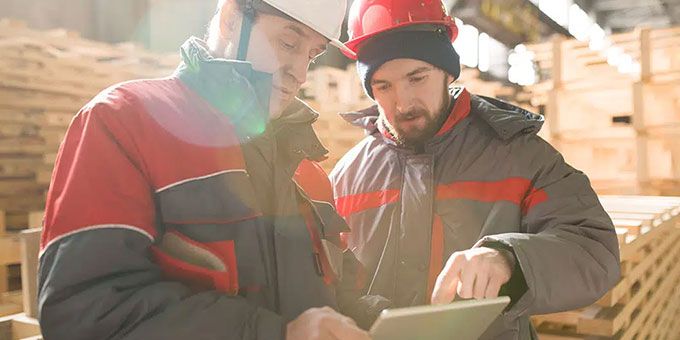
Article from | SafetySkills
Terms to Know
Before digging too deeply into the importance of audits and inspections, let’s take a look at these two terms in the context of a safety program.
Most people are likely familiar with safety inspections, which typically cover the day-to-day tasks and activities involved in a job. Inspections can include looking at machinery and tools or conducting jobsite walkthroughs to identify potential safety hazards.
On the other hand, safety audits aim to identify weaknesses in an overall safety program by reviewing processes and procedures. Audits also help to ensure operations meet safety requirements and best practices.
However, try not to get too hung up on these terms. Many organizations use them fairly interchangeably, and some may even use the terms opposite of the widely used definitions outlined above.
Regardless of what your team calls these safety reviews, all that matters is that these tasks serve to identify and create the safest working environment possible.
What is Required?
We know it can feel overwhelming to think about the hundreds of potential OSHA regulations your company must uphold at any given time, and there are some extremely specific OSHA rules detailing inspections for certain equipment or situations, such as cranes or powered trucks.
But when it comes to self-inspections, it can help to think of safety on a basic level. For example, no matter what type of work you are involved in, you will need to abide by OSHA’s General Duty Clause, which requires employers to provide a place of employment that is “free from recognizable hazards that are causing or likely to cause death or serious harm to employees.”
While the General Duty Clause does not specify that you must carry out workplace inspections, it is easy to see how doing so can allow you to create a safer environment for all employees. After all, inspecting equipment or reviewing procedures will help you identify potential issues or safety hazards — ideally before an incident occurs.
Additionally, you need to remember that OSHA conducts literally thousands of workplace inspections each year. About 60% of inspections are unplanned, which means they occurred because of employee complaints or due to an incident.
OSHA inspections can result in massive potential fines. In fact, in 2022, employers could face fines ranging from $1,036 up to $145,027 per violation. Aside from the obvious risk of potentially endangering employees, OSHA violations are clearly something to be avoided.
Self-inspections could help in this area, bringing to light potential dangers before an official visit from an OSHA inspector happens.
Conducting a Safety Inspection
If you didn’t before, you likely now understand that inspections are an important part of any workplace safety program. But how do you go about completing them? Well, it can be as simple or as complicated as you want it to be.
One way to conduct safety inspections is to have employees conduct informal inspections every day. In fact, many employees probably already do this without realizing it, for instance checking for slip or fall hazards or inspecting personal protective equipment before use.
Making sure employees always follow up with a supervisor or manager regarding what they find during these basic inspections can reinforce safety in a simple, everyday way.
Another option is, of course, conducting a formal inspection. These reviews should occur regularly, based on your organization’s needs — they can happen weekly, monthly, quarterly or on some other set schedule that best fits your industry and your hazards.
These inspections should be led by someone knowledgeable in the area(s) they will be looking at. This doesn’t always have to be a safety professional in title, but for many teams, it probably will be.
Similarly, the items an inspector reviews will vary depending on industry, job hazards, how detailed each inspection is, and other factors. However, there are some basic checklist ideas that could apply in nearly any situation, to give you an idea of hazards to be on the lookout for:
- Are safety signs or warnings posted where appropriate?
- Is a first-aid kit available and adequately stocked?
- Are operating permits and records up-to-date?
- Are fire suppression system inspections current?
- Are all work areas properly lit?
There are practically endless checklist items that can be added to an official inspection and it may seem overwhelming to know where to start. It can be helpful to use a template guide that provides checklist criteria that is potentially related to the operations at your organization.
While creating your inspection checklist is of course important, the crucial part of an inspection actually occurs when it is complete. What are the next steps?
If your safety inspector comes across a situation or piece of equipment that fails the checklist inspection, logically, that issue will need to be corrected. The safety inspector — or someone further up the chain, where applicable — should set up corrective or preventive actions (CAPAs) intended to resolve the failed inspection.
Corrective and preventive actions can essentially be anything that will fix the situation, from replacing a piece of equipment to assigning employee training. Regardless, your CAPA should always have a specific employee (who will be responsible for the action) and a specific end goal (that can be documented as “completed”).
Don’t think of failed inspection items or even corrective actions as negatives. On the other hand, these can be seen as positives, because they represent potential hazards that may have caused larger, more severe incidents in the future.
By conducting a thorough safety inspection, you can be sure your team is regularly checking for safety hazards, keeping your employees safe and your company out of trouble.
Conducting a Safety Audit
Unlike a safety inspection, a safety audit is likely not being done on an everyday basis by any regular employee. As mentioned previously, safety audits cover processes and procedures, meaning they will typically be completed by someone with not only safety experience, but knowledge of the organization and its inner workings.
Similar to safety inspections, the details of a safety audit will be up to each organization, but there are four basic steps that can help you understand and outline what should be done for your own safety audits.
- Inspect the general environment. One of the first things a safety auditor will do is inspect the overall workspace to get a general understanding of what might need to be addressed. Remember that common areas should be checked, because places such as restrooms, parking lots and break rooms are likely not free from hazards.
- Review work processes. Next, the auditor should perform a physical inspection of all work areas. They will need to investigate the premises, procedures, people and programs, looking for any clear violations and potential hazards or safety issues. Auditors often take pictures or interview employees and organizational leadership for further details.
- Create a report. Once the audit is complete, the auditor should summarize what is and isn’t working within each department or area, indicating the priority and severity of different safety issues. This report can also include deviations from industry best practices and safety procedures that are not being followed properly.
- Make recommendations. Of course, just like with safety inspections, the follow-up recommendations are key. This step isn’t necessarily completed by the safety auditor, but their guidance can be helpful. Again, here is where the corrective and preventive actions come into play, correcting existing problems and preventing future potential accidents.
As mentioned, OSHA does not require any safety inspection or safety audit, but they do offer an audit tool to help organizations evaluate how well they are implementing their safety program, identify weaknesses and focus on continued improvement.
Partner with Safety Professionals
Incorporating safety audits and safety inspections into your organization may seem daunting, but consider how important these tasks can be in identifying and preventing serious occupational incidents.
Whether you decide to simply start having your employees conduct informal — but documented — inspections or you want to implement annual safety audits, knowing where to start is typically the hardest part.
For more than 30 years, SafetySkills has been working with customers around the world to implement health and safety training programs and offers a full-suite of safety management tools, including those necessary for effective audits and inspections.
Contact SafetySkills to learn how audits and inspections can help reinforce safety in your organization and to access free template guides with safety audit and inspection checklists today.
The content & opinions in this article are the author’s and do not necessarily represent the views of ManufacturingTomorrow
Comments (0)
This post does not have any comments. Be the first to leave a comment below.
Featured Product
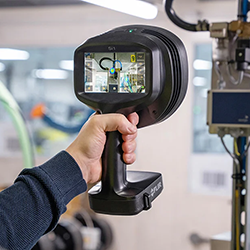