Experts believe that ERP can generate incremental value over the years. This blog discusses the costs of an ERP and the ROI calculations of the software. It goes on to debate whether ERP is an investment or an expense. Read this blog now!
Food ERP An Investment Or An Expense
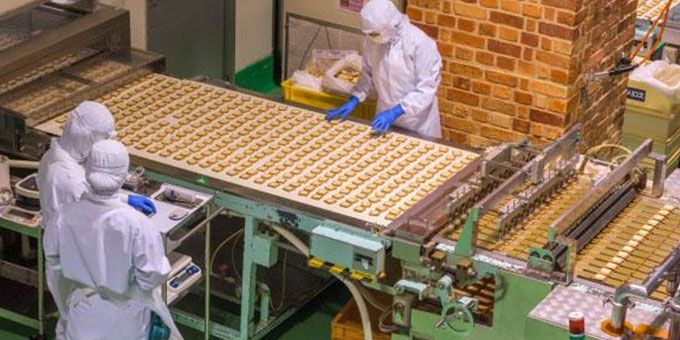
Sanjay Panjwani, Managing Director | BatchMaster Software
Food manufacturers have to operate on idealistic deadlines due to the short shelf life of their perishable inventory. Goods in the global food supply chain move at a rapid pace, owing to the manufacturers’ responsibility to deliver fresh and safe products to their customers. Over the years, the food industry has seen increasing challenges in terms of product quality, food safety, traceability and compliance. Supply chain disruptions following the COVID-19 pandemic have only added to the difficulties of this hyper-functioning industry environment.
Manufacturers of beverages, dairy, meat & poultry, bakery, convenience foods & snacks, fruits & vegetables, confectionery, frozen foods and many more categories are on the lookout for a best-fit ERP solution these days. But before finalizing a Food ERP solution, companies need to establish an economic case for the investment. A comprehensive cost-benefit analysis needs to be carried out to ensure that the ERP becomes an investment rather than an expense. Let’s examine the costs and returns of an ERP implementation to understand the nuances of the ROI calculation.
The Costs of Implementation and Operation
All the costs related to an ERP implementation are unified under a single umbrella called “Total Cost of Ownership” or TCO. There are two separate components of TCO, implementation costs and operational costs. Implementation costs are incurred upfront while internalizing the ERP system into your business and operational costs are all the costs related to the upkeep and maintenance of the ERP system over the years. Therefore, consideration of the total cost of ownership should be made over at least 5 years, so that the actual costs of maintenance, training and upgrades can be fairly included.
In addition to this, the TCO of an ERP implementation also depends on the mode of deployment, either perpetual licensing or SaaS (Software-as-a-Service). The perpetual licensing model caters to on-premises ERP implementations. This model has a well-defined cost of ownership and allows permanent use of the license without ongoing subscription costs. It may offer lower TCO for larger businesses over time. On the contrary, the SaaS model (Cloud or web ERP) is more suitable for smaller manufacturers. The Subscription pricing lowers the upfront costs with no on-premises hardware and minimum initial outlay for the license.
The major components of ERP implementation costs are as follows:
-
Software licensing fees
-
Additional servers and network hardware
-
Data conversion and transfer to new ERP
-
Customizations, if necessary
-
Testing
-
Training
-
Vendor/consultancy support post implementation
These are some of the most tangible costs of an ERP implementation, but companies should always make provisions for contingencies. According to experts, a 10% contingency budget built into your cost projections will put you in good stead for any unforeseen expenditure. On top of this, the business also has to invest in the maintenance of the software and its related infrastructure for all the years that they keep on using it. Maintenance costs for an ERP system typically run between 1–2% of the company’s annual revenue. The major elements of maintenance costs are as follows:
-
Hardware Maintenance
-
Network costs
-
IT workforce
-
Updates/Upgrades
-
System Expansion
-
Support
In the event of any tech investment, clients run the risk of getting oversold. There are many features that would sound exciting, but you will never use, whereas some may be needed later. To calculate the right ERP budget, you need to carefully select the features that you unconditionally need. This will help you keep the costs low and achieve a greater ROI for your investment. After much deliberation over budgets and costs, ROI calculation is equally important to project expected returns. Which is exactly what we will do next!
The Return-On-Investment
The analysis that goes into quantifying the ROI of ERP aids businesses in evaluating and anticipating the impact of an ERP system on their organization. The calculation also helps manufacturers refine their ERP to achieve incremental business value over the years. Companies need to understand the specific distinction between “hard” and “soft” ROI. Hard ROI refers to traditional return that can have quantifiable financial representation and soft ROI consists of all the intangible benefits offered by the ERP system, such as improved decision making and superior departmental collaboration.
The formula for calculating ERP ROI is as follows:
Difference between hard and soft ROI
As it is clear from the formula, ROI is the ratio of the gains delivered by an ERP to the total cost of ownership. The hard returns already have a numeric value, but companies also need to translate soft returns into solid numbers to correctly evaluate the ROI. It is important to understand that time-phased cost and benefit will project a time-phased ROI, which would be negative at the start and turn positive as the years go by. This is why it is advisable to calculate ERP ROI over 5 years. The hard returns obtained from an ERP can be categorized as:
-
Sales Growth
-
Productivity Gains
-
Operational Cost Savings
-
Increased Margins
-
Labor Cost Savings
-
Product Improvements
-
Increased Order Volume
-
Lower Administrative Costs
According to a study, ERP customers saw a 40% to 60% improvement in order process efficiency since the implementation of their systems, and 40% to 55% saw a reduction in reporting times, both of which can be easily quantified and therefore fall in the category of hard ROI. In addition to these tangible returns, there is a long list of intangible benefits that elevate the organization’s ERP experience. These soft benefits for a food manufacturer are listed below:
-
Improved Decision Making
-
Enhanced Compliance
-
End-to-End Traceability
-
Better Organizational Visibility
-
Heightened Employee Morale
-
Increased Brand Equity
-
Superior Collaboration
Irrespective of the implementation being on-premises or in the cloud, manufacturers can maximize ERP benefits by adopting certain practices. If the employees can use the ERP software to its full potential, nothing can stop a company from extrapolating its ROI. Everyone involved in the project should understand the critical role of the ERP in helping the company drive growth and success. It is also important to constantly evaluate and refine your approach toward the implementation. Business leaders should assess their costs and returns from the ERP solution periodically.
The accurate measurement of the benefits of a new ERP is very important to gain a complete picture of the obtained ROI, including both soft and hard benefits. Additionally, companies would do well to avoid common ERP pitfalls like treating ERP implementations as a traditional technology deployment, with a single upfront cost and short-term payback period. While in the real world, most successful ERP implementations are divided into well-planned phases and the ROI is calculated at each milestone.
Food ERP: Investment or Expense?
As stated above, ERP might look like a liability in the initial financial years after the implementation. However, as the business begins to realize the benefits of the ERP over time, they would see an increased output that can directly be attributed to the software. If the company has chosen the right ERP vendor and selected the correct modules, there is no chance that an ERP would ever turn into an expense over its planned lifecycle. There are many countable and abstract benefits of Food ERP software that prove that the software is worth its weight in gold. Some of those benefits are listed below:
Benefits of food manufacturing ERP software
-
Supply Chain Management – An ERP handles your all-day-to-day chores plus your mission-critical operations. From receiving sales orders to planning material and production, procuringplus managing inventory, handling processing, meeting quality and compliance, processing finance and finally delivering- an ERP streamlines and supports all.
-
Inventory Management – Food manufacturing ERP software ensures that stock levels are always maintained and replenished from time to time. Records relating to the storage specifications and expiry/shelf-life can also be kept, catchweight and lot strength of food items can be maintained, and lot characteristics can be precisely entered.
-
End-to-End Traceability – Every lot is assigned a unique ID which helps the manufacturer locate the associated material instantaneously. Ensuring step-by-step visibility across the supply chain can help with error corrections and product recalls.
-
Compliance – By raising alerts for potential compliance issues, ERP can curtail any possible losses. It also provides secure audit trails to reduce errors, generates labels, performs quality analysis and tests, and follows GMP with Lot statuses.
-
Real-Time Data – Food manufacturing is a hyper-functioning discipline, and a lot of important decisions need to be taken on the spot. With real-time data, ERP enables informed decision-making and ensures operational efficiency.
All these benefits actively or passively contribute to the ROI of an ERP and translate into sales growth, productivity gains and operational cost savings. This proves that if utilized correctly, ERP can deliver incremental value over the entire period for which it is functional. Industry-specific ERPs generally deliver their ROI faster than generic ERP software.
About Sanjay Panjwani
Sanjay Panjwani is the Managing Director at BatchMaster Software, the leading provider of enterprise software solutions for process manufacturing industries. He’s on a mission to solve business challenges through innovation in ERP solution suites.
The content & opinions in this article are the author’s and do not necessarily represent the views of ManufacturingTomorrow
Comments (0)
This post does not have any comments. Be the first to leave a comment below.
Featured Product
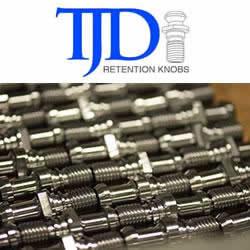