Remote inspections with smart glasses bundle the know-how of specialists from various fields in only one carrier who must be on site. This saves time and costs and lowers emissions.
Remote Inspections Save Time and Increase Flexibility
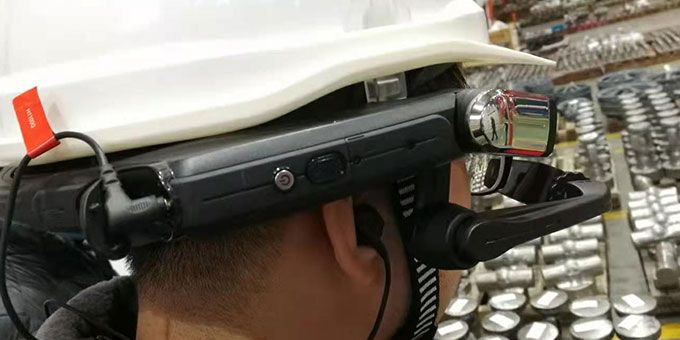
Christoph Gatzen, Head of Instrumentation, Control and Electrical Division & Simon Lemin, Director of Industry Service Division | TÜV SÜD
Conventional inspections of plants and components were limited to some extent during the “Corona crisis” because of the imposition of lockdowns and travel restrictions. A Chinese valve manufacturer opted for a remote inspection (RI) from TÜV SÜD using “smart glasses”. This enabled an independent third-party quality assessment to meet regulatory requirements in Europe prior to product marketing.
Can an inspection be conducted without all necessary experts being present on site? It can, as recent examples show. To remotely test, inspect and certify technical systems and facilities, a bidirectional connection is established – between at least one onsite inspector (smart glass user) and any number of remote assessors (external experts). They follow and guide the inspection step by step on a computer screen. This reduces travel time and cost of flights to plants which can be located anywhere in the world. The solution is thus environmentally friendly by reducing air pollution. Areas of application usually include development, maintenance, troubleshooting and training.
TÜV SÜD has already successfully applied the technology in the context of production monitoring, training, and further education, as well as acceptance tests or site acceptance tests. From a strategic perspective, there are good reasons for this: According to an analysis by Fortune Business Insights the global inspection, repair, and maintenance (IRM) market size has shown a 7.2 percent decline in 2020 as compared to 2019 in “pre-pandemic times”. Nonetheless, the IRM market is anticipated to grow from about USD 43 billion in 2022 to nearly 73 billion by the end of this decade. As the industry becomes more digitised, remote solutions such as smart glasses will grow in importance where performing inspections would otherwise be an obstacle due to distance or restrictions.
Remote guidance and much more
The industrial smart glasses provide remote guidance for the wearer to visually connect with experts and technicians. At the same time, remote assessors can transmit digital information such as images, videos, or text to be displayed on a movable, high-resolution screen on the edge of the glasses. TÜV SÜD chose a fleet of assisted reality devices of the HMT-1 model from the US manufacturer RealWear for their robust and durable design. Installed is the SHARE app by the German software vendor oculavis GmbH, which works closely with RealWear on integrated solutions. In addition to their basic functions, the smart glasses include self-guided augmented reality workflows and step-by-step instructions. That makes technical information like digital manuals directly accessible to the wearer, who in turn can record videos and photos to share with an expert.
In noisy work environments, such as an engine room, hearing protectors (Personal Protective Equipment – PPE) can be connected to the smart glasses via jacks. The microphone of the smart glasses can either be muted to allow one-way communication only. Or noise cancellation can be activated so that inspections can still be conducted. The industrial smart glasses are also designed to withstand dusty and wet conditions: They can be worn under protective eyewear and be integrated into safety helmets (PPE). This largely eliminates the risk of personnel being exposed to a harsh working environment. Additional occupational safety benefits are provided by a voice-controlled user interface, which leaves the wearer’s hands free so that they are not distracted from the actual inspection process.
A second opinion might be easily at hand
TÜV SÜD brings together experts from various fields from around the world to optimize workforce use and enhance global collaboration. Assessments can be flexibly adjusted to the situation: For example, if expertise from various domains is needed, both the mechanical engineer and the electrical engineer or the colleague from materials technology can be consulted. They are available at much shorter notice than with traditional on-site inspections. This also greatly reduces downtimes. In addition, a second opinion can always be obtained from another expert, which further improves the inspection quality. Real-time feedback saves follow up consultations and thus time.
For an inspection to take place remotely, a few questions need to be answered: Is a TÜV SÜD Remote Inspector available near the site? Has the TÜV SÜD employee received a briefing on the project with the specifics of the inspection? Does the customer agree with the RI and has he confirmed if an RI is permissible for his client’s request (e.g., if an authority requires proof of conformity)?
It must also be clarified if all technical documents have been checked for completeness and validity and whether the glasses and their software can be integrated into the existing IT infrastructure. Once all organizational hurdles have been cleared, the inspection is conducted. An inspection report is then prepared, and the results are sent to the customer in the form of a protocol.
Secure servers and a fast network needed
As the examination is recorded and documented as part of production monitoring, all data must be stored on servers according to the high security requirements of the General Data Protection Regulation (GDPR). To handle sensitive data as carefully as possible, TÜV SÜD operates secured servers that are certified in accordance with the international standard ISO/IEC 27001 – Information security management. Before a remote inspection is initiated, the customer must allow video and audio transmission. A data protection officer available on site should also be involved, for example to approve a data backup and select its type or to specify privacy measures such as face blurring.
The connection of smart glasses also requires a reliable and sufficiently fast network on site. The easiest way to check this is running an internet speed test suitable for the respective connection type (Wi-Fi, LTE). This can be done online via any web browser. Recommendations for a flawless experience include, amongst others, a bandwidth of 4Mbit/s (Up/Down).
In a nutshell
Remote inspections with smart glasses bundle the know-how of specialists from various fields in only one carrier who must be on site. This saves time and costs and lowers emissions. Plant failures and consequential damage can be investigated and repaired in a short time. TÜV SÜD offers customers inspection services according to DIN EN ISO/IEC 17020:2012 and provides an ISO 20071-certified Remote Service Platform to store and permanently retrieve the recorded inspections in encrypted form. To date, TÜV SÜD Remote Inspectors are available at over 100 locations worldwide – growing constantly.
Global collaboration even during lockdowns
TÜV SÜD´s customers already using remote inspections include a Chinese manufacturer and distributor of valves. The company needed a third-party quality assessment to meet regulatory requirements for marketing in France and the UK. Although a lockdown was imposed at the time and travel restrictions were in place, the company was able to bypass these and successfully assess the valves within the specified time frame. This also helped the customer to save on travel expenses by avoiding seven round-trip intercontinental flights, each with more than ten hours of travel time. Another plus was the reduced air pollution that would otherwise have occurred.
The valves in question were intended for use in nuclear and thermal power plants, among other applications, and therefore had to be monitored during production. For this purpose, the company commissioned TÜV SÜD. Employees from TÜV SÜD Greater China were on site but could rely on the support of their colleagues from TÜV SÜD in Germany. As the valves were electronically controlled, electrical engineers had to be called in via smart glasses at the manufacturing facility. Together with mechanical engineering experts, they checked the critical components against digital manuals and circuit diagrams. The specialists for non-destructive testing and leak tightness as well as for seam welding were also involved via smart glasses.
The content & opinions in this article are the author’s and do not necessarily represent the views of ManufacturingTomorrow
Comments (0)
This post does not have any comments. Be the first to leave a comment below.
Featured Product
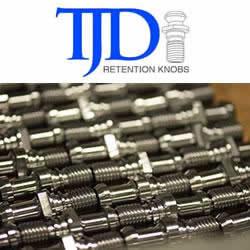