Using ultramodern capabilities and world-class laboratory facilities, NREL’s energy storage researchers continue to push battery boundaries with materials development, thermal management, diagnostics, and modeling.
Powering the Future: NREL Research Finds Opportunities for Breakthrough Battery Designs
Rebecca Martineau | NREL
In the 200 years after its invention, the extraordinary battery has undergone significant evolutions to meet modern applications. These self-contained energy sources are key to our increasingly connected society, powering our communication and transportation networks.
With the shift to renewable energy, a new era of electrification is on the horizon, supported in large part by the breakthrough battery designs that researchers at the National Renewable Energy Laboratory (NREL) believe are at our fingertips.
“NREL’s battery research team brings together a diverse range of experts—physicists, chemists, and engineers—to meet complex challenges in energy storage,” said NREL Senior Energy Storage Engineer Matt Keyser. “Our research spans the scale of technology readiness and battery research, from atom-scale materials science to full-scale systems.”
From left, Kandler Smith, Matt Keyser, and Andrew Colclasure lead the electrochemical energy storage research at NREL, providing a holistic approach to modeling and diagnostics, materials development, and battery safety. Photo by Werner Slocum, NREL
Today’s predominant choice for advances in energy storage, lithium-ion (Li-ion) batteries gained popularity as a lighter and more powerful alternative to lead-acid or nickel-metal hydride designs. These batteries allow users to control energy flow for repeated, high-speed charging and discharging—powering everything from cell phones to laptops, electric vehicles (EVs), and large-scale stationary storage. Ongoing research at NREL continues to refine Li-ion batteries to meet the unique needs of different applications.
What does the future of battery storage hold? In the transition to a more electrified society, batteries will play an essential role in helping store energy from renewable sources to supply electricity for buildings, transportation, and grid applications. Emerging battery technologies must focus on reducing costs, while maintaining lifetime and density performance. Using ultramodern capabilities and world-class laboratory facilities, NREL’s energy storage researchers continue to push battery boundaries with materials development, thermal management, diagnostics, and modeling.
Materials Research for Lithium-Ion and Beyond
The first level of innovation happens in battery materials synthesis—the stage at which developing or refining materials for new battery designs occurs. At a high level, all batteries have a positive electrode (cathode) and a negative electrode (anode) suspended separately within an electrolyte. As electrons move from the anode to the cathode, they generate an electric current and supply electricity. Breakthroughs in material upgrades throughout the battery architecture can unlock better battery performance, stability, and sustainability improvements. However, introducing new materials, such as silicon and sulfur, can also bring about new chemical reactions and mechanical stressors. NREL researchers rise to the challenge of addressing these evolving reactions through careful evaluation of advanced materials, weighing opportunities to meet a variety of applications and needs.
Silicon nanoparticles may help eliminate barriers to improved energy density in lithium-ion battery cells. Photo by Werner Slocum, NREL
Silicon Anodes Unlock Increases in Energy Density
Silicon may be one of the next big battery material upgrades. As EVs continue to gain popularity, researchers have identified silicon as a promising opportunity to increase the energy density of vehicle batteries. Recent research from the NREL-led Silicon Consortium Project (SCP) has found that replacing the graphite typically used in Li-ion battery anodes with silicon may pave the way to reduce battery pack size by 25%–30% and increase driving range by 30%–40%.
However, silicon-based anodes present unique challenges to the stability and lifetime of Li-ion batteries. Lithiation—which occurs during battery charging—leads to swelling and compression of the silicon, causing cracks and fractures of battery particles. Additionally, a reaction between the silicon and the liquid electrolyte leads to the formation of a “silicon electrolyte interface” material that causes decomposition of the electrolyte within the battery.
“It comes down to making sure different components within the cell behave well together,” said NREL Senior Materials Scientist Tony Burrell. “Our SCP research aims to equip silicon anodes with protective coatings to extend the calendar life of the silicon-based batteries, essentially how long they can function. Electrode coatings are commonly used to improve the durability of batteries, but it’s up to us to identify the right materials and thickness for use with silicon.”
Researcher Andrew Colclasure uses a glove box to assemble and disassemble batteries components for materials analysis. Photo by Werner Slocum, NREL
Future Designs Target Sustainability, Material Availability
Sustainability is another concern at the forefront for NREL researchers. As such, research teams are prioritizing material and product designs that reduce the use of rare critical materials, such as cobalt, currently used in Li-ion batteries. Although Li-ion continues to be the standard for EVs, the unique priorities of stationary energy storage—where lifespan is typically more important than battery size—are opening new doors in materials research.
“There is a lot of value in optimizing designs for battery applications beyond transportation,” said NREL Energy Storage Researcher Andrew Colclasure. “Our increased focus on stationary batteries is challenging researchers to get creative with materials development, including earth-abundant or readily available materials.”
Recent NREL research has identified lithium-titanate anode and lithium-manganese-oxide cathode batteries as promising critical-material-free options. The laboratory’s researchers also look beyond lithium to new or emerging technology ideas, such as redox flow, aqueous, sodium, or magnesium. One encouraging area of research aims to replace the liquid electrolyte with a solid-state battery design. Solid-state batteries could offer improved stability and energy capacity over traditional battery technologies; however, more research is needed to optimize these batteries for widespread use in vehicle or stationary applications.
Guiding Innovation From Materials to System-Level Designs
From chemistry compositions to overall battery structures, the opportunities for battery advancements are endless. To guide future innovations, NREL’s cutting-edge capabilities and facilities offer experimentation, modeling, and analysis tools to better understand the physical, chemical, mechanical, and structural properties of energy materials and storage systems.
For new materials, these evaluations can streamline advancements within the battery architecture—including the cathode, anode, or electrolyte. As these materials progress to be used in cells, modules, packs, and complete energy systems, characterization also continues to play an important role in battery research.
“Our diverse and talented electrochemical energy storage team is working hand-in-hand with the lab’s materials scientists to evaluate new chemistries and incorporate optimized materials in large-scale cells,” Keyser said. “Our team performs extensive characterization to assess the fundamental cell and module characteristics critical to material development, model building, and validation efforts.”
From left, researchers Donal Finegan, Chuanbo Yang, Kandler Smith, Andrew Colclasure, Peter Weddle, and Ankit Verma are part of the electrochemical energy storage using advanced X-ray diagnostic capabilities to take three-dimensional images of battery materials. Photo by Werner Slocum, NREL
Cutting-Edge Capabilities Reveal New Perspectives
NREL’s leading facilities equip researchers with the experience and tools they need to provide a thorough assessment of battery architectures. X-ray diagnostic tools—including a new X-ray nanoscale computed tomography scanner—capture the evolving composition and architectures of battery materials. Given the nondestructive nature of X-ray tools, researchers can view mechanical, electrochemical, or thermal changes as they occur in real time to understand the reactions within a battery during operation or cycling. These diagnostic capabilities span the different sizes, or length-scales, of battery architecture to provide the necessary insight for informing future battery designs.
Alongside advanced imaging, NREL researchers apply cutting-edge computer engineering coupled with physics-based machine learning and artificial intelligence to address gaps in how we understand battery properties. In one example, this approach leverages computer algorithms to mimic real-world degradation processes, giving researchers an idea of how different materials or designs would impact battery lifetimes. Overall, predictive models developed at NREL can quickly distill complex data sets to guide a variety of research projects, helping make batteries that charge faster and last longer.
“Where other research institutions rely on package battery models, NREL is developing new models leveraging our diverse research experience in complex physics, chemistry, mechanics, safety aspects, and artificial intelligence to provide new perspectives on battery research,” said NREL Energy Storage Researcher Kandler Smith. “Our combined forces bring a higher level of knowledge to every research and design project.”
Researchers at NREL, including Kandler Smith (pictured), use cycling techniques to measure the performance of next-generation battery cells during successive charge and discharge phases. Photo by Werner Slocum, NREL
Decoding Thermal Signals To Improve Battery Performance
One of the most important aspects of research around battery performance is thermal management. Although higher battery temperatures can improve the cell’s ionic conductivity and energy capacity, balance is key. Higher temperatures can accelerate chemical reactions, leading to cell degradation or aging that limits battery lifetime. Lower temperatures can limit energy density and battery performance. In addition, thermal management is critical to battery safety. In some cases, overheating and over-pressurization of the cell can result in thermal runaway—an extreme heat release with occasional catastrophic effects.
“The thermal performance of a battery is fundamental to overall energy efficiency,” Keyser said. “Hot spots in cells can indicate that energy is not being used efficiently throughout the cell. Our research optimizes operating temperatures of energy storage systems, ensure uniformity across the battery, and inform thermal management system designs.”
Accordingly, NREL’s thermal management experts rely on extensive equipment and capabilities—including NREL-customized calorimeters, cyclers, and environmental chambers—to evaluate all thermal aspects of battery operation to find where heat is developed. These assessments help optimize the thermal behavior of a battery cell, its lifespan, and safety of the energy storage system.
NREL’s battery recycling research includes black mass purification, led by researcher Kae Fink, to remove contaminants and maximize the amount of recoverable material to reduce Li-ion battery waste. Photo by Werner Slocum, NREL
Glimpsing the Future of Battery Storage
Backed by research at NREL, the next generation of battery storage looks promising. The laboratory’s research not only focuses on improving industry-favored Li-ion batteries, but simultaneously continues to explore new opportunities in battery designs. Key to the enduring success of battery storage, however, researchers also recognize the need to consider the future of spent and discarded batteries.
To that, NREL’s battery portfolio includes novel research to increase the lifetime value of battery materials through reuse and recycling. As part of the U.S. Department of Energy’s ReCell Center, NREL is helping improve direct recycling of Li-ion batteries, which uses less energy while minimizing environmental impacts to capture more valuable materials as compared to alternative recycling methods. This research supports the development of a circular economy for essential battery materials and improves overall sustainability of battery technologies.
“Energy storage is at the core of NREL’s mission to spread renewable energy technologies and optimize energy systems throughout the world,” Burrell said. “If our battery research can help support energy demand across the grid, we can minimize energy use, greenhouse gas emissions, resource depletion, and costs to fully realize a clean energy future.”
The content & opinions in this article are the author’s and do not necessarily represent the views of ManufacturingTomorrow
Comments (0)
This post does not have any comments. Be the first to leave a comment below.
Featured Product
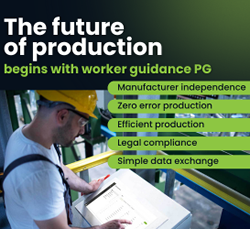