One of the best ways today to improve business efficiency is through the use of warehouse robots. And while planning is underway to adopt warehouse robots, it's important to consider the most ideal flooring.
Warehouse Robots and Why Flooring is Important
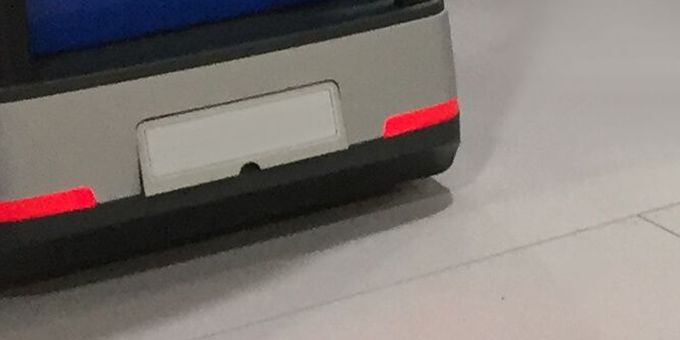
Article from | ResinDek
Throughput is everything.
Robots need to move quickly and operate as efficiently as possible. That's how you and your business can maintain uptime and reach your daily operational goals.
One of the best ways today to improve business efficiency is through the use of warehouse robots. Autonomous mobile robots (AMRs) and automated guided vehicles (AGVs) provide improved speed and accuracy within a warehouse environment. And while planning is underway to adopt warehouse robots, it's important to consider the most ideal flooring.
The Difference Between AMRs and AGVs
Autonomous mobile robots (AMRs) can include various automated robotic machines that help get work done. But instead of being fixed in place, as we've seen for years, these machines move with swiftness throughout manufacturing plants, warehouse facilities, and distribution centers. AMRs can include a variety of movable machine types. They come in all sorts of shapes, sizes, and various functionality where they are pre-programmed to perform various - yet highly specific - workplace duties.
Automated guided vehicles (AGVs), on the other hand, are the older brother of AMRs. AGVs have been around longer and use different technology. They move based on wires or magnetic strips. They are self-guided and can carry and deliver goods or items throughout a warehouse or facility. Pre-programmed through software, they move along directional routes.
AMRs are "smarter" than AGVs in a sense. Like a car with a built-in GPS, AMRs use navigation created via mapping software based on the facility's unique dimensions and pathways. Once the paths are preloaded, the AMRs move about on their own. Through laser technology, they will avoid obstacles in the way. Once that upfront programming work is completed, AMRs can be set to begin their routine, daily duties.
Both types of warehouse robots - AMRs and AGVs - require the right flooring underneath to ensure they are operating correctly, efficiently and avoiding technical issues or downtime.
How Warehouse Robots Are Improving Operational Efficiencies
It's been forecasted by ABI Research that revenues driven by robotics in business will grow from $166 million to $22 billion in less than 10 years - a mindblowing 13,000% increase. The real benefits of warehouse robots come from the ability to move faster, react more quickly, and repeat the same recurring tasks with ease. They can capture images and data, move materials, stock, sort, and inventory, and optimize picking.
With fewer errors, fewer inventory checks, the ability to safely perform dangerous jobs - and no lunch breaks needed! - workplaces are finding ways for machines and humans to coexist in a synergetic way. Robots are set to perform their technical, mundane, and repeatable work, freeing up operations employees to focus on more skilled jobs that require human.
What's more, equipped with artificial intelligence (AI), some can learn from their past behaviors and become smarter with each routine they perform. Through speed, safety, and efficiency, AMRs are having a significant impact on the supply chain and overall workplace productivity, ultimately helping companies reach greater levels of output and revenue - over time.
Industry 4.0 and Warehouse Robots
The term "Industry 4.0" represents the modern, 4th industrial revolution - one that focuses on innovative technology, artificial intelligence (AI), digital software, automation, and the Internet of Things (IoT). Robots play a profound role in Industry 4.0. More and more businesses are taking advantage of these mobile machines to improve their supply chains, especially at the manufacturing and distribution levels. The reality is that robots can perform work differently - and often better - than humans can.
They are stronger, more reliable, faster, more dexterous, and more precise. And they never tire, working day and night, if that's what makes sense for the business. They can lift hundreds of pounds and be equipped with laser-based safety features to avoid knocking into anything, including their human co-workers. Enabled through WiFi and equipped with sensors, cameras, and careful calibration, technology (and people) put robots on flooring paths throughout the workspace to perform their duties consistently, repeatedly, and error-free.
Why ResinDek® Mezzanine Flooring Is Perfect for Robots
Warehouse robots can be programmed to operate in warehouses and distribution centers. But operations managers should consider the type of flooring that's currently laid underneath the machines. The durability and condition of the flooring where the robots travel can have an impact on efficiency levels and cost. Certain flooring types, or worn or uneven surfaces, can severely impact the speed, fluidity, accuracy, and safety across the robots' motion and pathway.
Consider These Six Flooring Elements
It's critical that testing and evaluation happens upfront to understand first the type of work being performed on the floor. Flooring shouldn't be an afterthought or viewed as a commodity. Instead, it should be part of the planning process when robot technology is being considered.
There are six things to think about when planning for robots and flooring:
- Capacity: Can the flooring handle the load of the robot and the product? (ResinDek panels can easily support dynamic and static rolling loads from 2,000 to 8,000 lbs and can withstand the intense demands inside any warehouse.)
- Friction: Can the robots operate smoothly based on what's on the floor? This shouldn't be considered for just when the floor is new, but when it's in use when there's dirt and grime from day-to-day operations too.
- Roughness: What is the contact area like between the wheels and floor? How will the robots run along it?
- Flatness: Folks using traditional concrete flooring have reported issues with levelness, and this leads robots to possibly falling off-track, further leading to human involvement, repairs, and expensive downtime. (You don't have to worry about ResinDek flooring with its trusted, level surface.)
- Gloss: If lasers are reading vertically/downward toward the floor - think about stickers or labels - then gloss of the flooring might be a factor. You'll need a flooring finish that doesn't impact laser accuracy. (When required, ResinDek's coatings can be customized to your specific robots requirements).
- Wear-resistance: Traditional warehouses using pallet trucks on elevated platforms can see tens of thousands of cycles over 10 years. Over that same time, robotics may see millions of cycles. That shows the massive amount of work that robots can perform over humans and the redundancy of robotics. (ResinDek with MetaGard® steel should be considered for use in areas around pickstations and areas with high traffic cycles. It offers supreme durability and is crafted specifically for areas with unusually high wear from the robots.)
Our Flooring Recommendation for Warehouses with Robots
In general, our warehouse mezzanine flooring is ideal where AMR and AGV robots are being used. ResinDek with TriGard® ESD is purposefully engineered to endure the consistent, repeated travel patterns associated with robots and AMRs. The TriGard ESD finish comes standard with an electrostatic dissipative (ESD) finish that protects sensitive electronic equipment from damage.
As more and more businesses deploy robots throughout their facilities and warehouses, it's important to keep in mind the most appropriate flooring to help keep production operating at its highest levels while also reducing the frequency of flooring repair or replacement. ResinDek mezzanine flooring from Cornerstone Specialty Wood Products is ideal for workspaces utilizing warehouse robots.
The content & opinions in this article are the author’s and do not necessarily represent the views of ManufacturingTomorrow
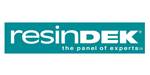
ResinDek / Cornerstone Specialty Wood Products
At Cornerstone Specialty Wood Products®, we know and understand the importance of having the right flooring product for the right application. That's why we offer a variety of ResinDek panels in different thicknesses, densities, and with different surface finishes. Since 1994, ResinDek flooring panels have been installed in distribution centers, warehouses, manufacturing plants, and cold storage facilities for major corporations worldwide. The intent of Cornerstone Specialty Wood Products then and now is "We don't just make better mezzanine floors…We make mezzanine floors better". We strive to provide solutions that improve the ergonomics in work environments, reduce environmental impacts, and bring significant value to the professionals in many different industries.
Other Articles
Sneaker and Sportswear Retailer’s New Mezzanine and Ground Floor Feature ResinDek Robotic Flooring
Key Flooring Considerations When Updating an Existing Industrial Mezzanine System
Electrostatic Dissipative Flooring vs. Anti-Static Flooring: Which Flooring is Right for Your Facility?
More about ResinDek / Cornerstone Specialty Wood Products
Comments (0)
This post does not have any comments. Be the first to leave a comment below.
Featured Product
