In metal powder bed fusion process the quality and of the powder raw material are of paramount importance, as the process relies on thin layers of metal powder being deposited and melted to produce metallic parts.
Metal Additive Manufactured Parts for Racing Car
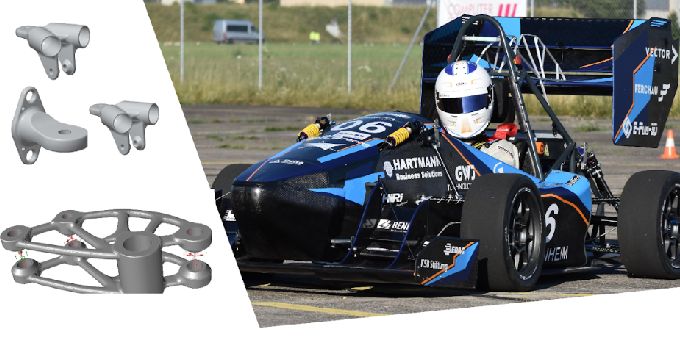
Case Study from | Eplus 3D
Machine
EP-M260
Material
Aluminum and Titanium
Other Parameters
The automotive parts and accessories market is an important source of revenue for global automotive manufacturers. With the 3D technology it is possible to print parts with geometries, that are difficult to realize with conventional methods, and it is also more cost effective, when non series production take place. An example of this can be seen on pictures below. The wishbone is used to connect carbon tubes, which are used in the suspension with each other and with other components such as the above described diverter. Eplus3D supported the team in manufacturing the parts using Ti6Al4V Titanium Alloy powder. In this case, Delta Racing could fulfil their design requirements, resulting in a win-win situation regarding cost and weight. In an average, the weight could be reduced by over 50% and the whole car could benefit of a weight reduction of around 3kg. The MPBF printing technology, not only allows the user to produce high performance parts, it also improves the efficiency of whole chain, from production time to the performance of the part.
- Build Volume: 266×266×390mm3
- Optical System: Fiber Laser, 500W/1000W(single or dual-laser optional)
- Spot Size: 70~100µm
- Building Speed: Single Laser 15~35 cm3/h Dual Laser 25~55cm3/h
- Layer Thickness: 20~120µm
- Dimension: 2800×1300×2410mm3
- Application: Aerospace, Aviation, Automotive, Tooling etc.
Overview
The Delta Racing team at Mannheim University of Applied Sciences and Eplus3D Tech GmbH recently demonstrated that additive manufacturing technology can dramatically reduce costs and material in the production of automotive components.
Partner
Delta Racing Team Since 2012 the Delta Racing team, with around 60 students, are working on a concept for an electric racing car. In the last year, some parts were printed by Eplus3D in the EP-M260 with Titanium and Aluminum for their racing car, achieving a weight saving of 60%.
The racing car is ideally as light as possible. A lighter car means a higher acceleration and better handling among other things.
Introduction
Additive manufacturing technologies (AM) or 3D printing allows the layer-by-layer production of complex parts with features that are difficult to achieve by traditional methods. In metal powder bed fusion process the quality and of the powder raw material are of paramount importance, as the process relies on thin layers of metal powder being deposited and melted to produce metallic parts. In this technology, conventional powder quality assessments are limited to particle morphology, size distribution, density and flowability. In addition, Additive manufacturing has several advantages. For example:
Freedom of Geometry
Hollow spaces or cooling channels can be integrated into components. This makes it possible to save weight or combine electrical or mechanical functions in one part.
Digital Manufacturing
With this technology it is easier to produce a part direct from a CAD file. No casting forms are needed and none CNC-code has to be programed. Usually, the CAD file only have to be edited to include support structures and divided into layers (slicing) with a data preparation software.
Finished Parts and Time Saving
After the printing process the parts are almost ready to use and it is only necessary to finish the function areas like bearing places or screw threads. Additional post processing technics like sanding or coating is also possible. This allows the user to save time.
Eplus3D has printed several parts for Delta Racing until now. A few of these are shown below. The long-lasting relationship helps both our business by combining knowledge, consumer reach and technology. We all can build a team, where individual members can learn from each other through giving and receiving feedback and sharing different perspectives.
Both of us will thrive as a result of the combined efforts to help one another.
Front and Rear Diverter
Topology Optimization
Front and rear diverter are necessary to transfer the forces from the wheel carrier to the spring-damper unit. Additive manufacturing gives the user more freedom to design the part for the same function and make it lighter at the same time. To achieve this, the Delta Racing Team used the SKO (Soft Kill Option) method to identify all the areas where material is not needed. In areas of high stress, the E-module is increased in the simulation, while in areas of low stress, it is decreased. In conclusion, the software creates a function of the E-Modul about the tension in the different regions of the part.
For the Simulation the following aspects need to be defined: All different angles and load cases need to be identified. The boundary and ancillary condition together with the loads of the system must be set. Afterwards, the program calculates the optimum shape of the diverter for all the load cases. As a result, the safety factor and the force flow can be controlled.
Design for Manufacturing
For better results, the generated topology optimized geometry Diverter needs to be improved. For this step, different approaches can be used. The Delta Racing team works with Solidworks to reconstruct the shapes with curves, avoiding sharp and small corners. To validate the generate design, a mechanical structure analysis must be performed.
Wishbone
The automotive parts and accessories market is an important source of revenue for global automotive manufacturers. With the 3D technology it is possible to print parts with geometries, that are difficult to realize with conventional methods, and it is also more cost effective, when non series production take place. An example of this can be seen on pictures below. The wishbone is used to connect carbon tubes, which are used in the suspension with each other and with other components such as the above described diverter. Eplus3D supported the team in manufacturing the parts using Ti6Al4V Titanium Alloy powder. In this case, Delta Racing could fulfil their design requirements, resulting in a win-win situation regarding cost and weight. In an average, the weight could be reduced by over 50% and the whole car could benefit of a weight reduction of around 3kg. The MPBF printing technology, not only allows the user to produce high performance parts, it also improves the efficiency of whole chain, from production time to the performance of the part.
Print Parts
In this case the delta racing team decide to print the diverter with a titanium alloy, saving more than 60% of weight. The weight was reduced from 240g to 91g per part, what means around 600g less for the racing car. In addition additive manufacturing offers the team maximum geometric design freedom and due to the lower material consumption, costs can often even be reduced significantly.
About Eplus3D
Eplus3D was founded in 2014, the core technical team has more than 25 years of AM technology experience and is engaged in research and development of industrial-grade Additive Manufacturing systems and application technologies using with MPBF™ (Metal Powder Bed Fusion) , PPBF™ (Polymer Powder Bed Fusion) and Stereo lithography 3D printing technology. Eplus3D provides professional application solutions for the fields of Aerospace & Aviation, Energy, Oil & Gas, Automotive, Tooling, Healthcare, Consumer Goods and Precision Manufacturing. Eplus3D has three facilities in Beijing, Hangzhou and Stuttgart, with an annual scientific research investment of more than 20% of the revenue with comprehensive invention patents, utility model patents, software copyrights as well as appearance patents. It has made great achievements in the design-, process-, software-, materials- and post-processing development for additive manufacturing and has successfully implemented AM solutions at customer site in more than 40 countries and regions such as Europe, USA, Japan, South Korea and Southeast Asia.
The content & opinions in this article are the author’s and do not necessarily represent the views of ManufacturingTomorrow
Comments (0)
This post does not have any comments. Be the first to leave a comment below.
Featured Product
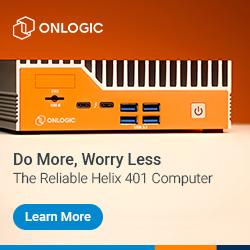