The lean manufacturing methodology chiefly revolves around minimizing production times and raising efficiency by eliminating waste. In this post, we go through the 8 principal wastes in lean manufacturing and see how manufacturing software can help to address them.
The 8 Wastes of Lean Manufacturing
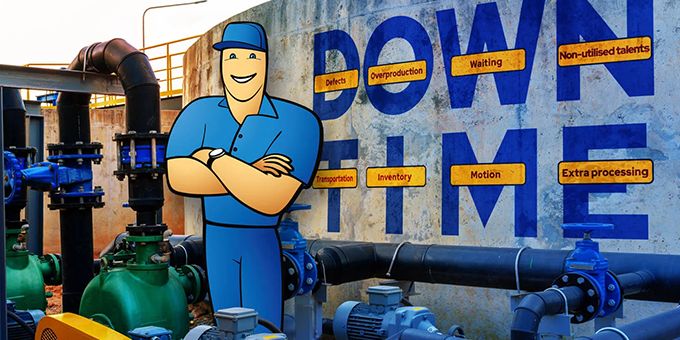
Mattias Turovski | MRPeasy
What is waste in lean manufacturing?
In the lean manufacturing methodology, waste is described as any activity that does not bring value to the customer. It encompasses far more than physical garbage or production residues and can result from anything that loses time or lowers a company’s operational efficiency. From underutilized resources and overprocessing to badly organized work spaces – waste in lean thinking is essentially the measure of any process that is running sub-optimally.
The lean way, as developed by Toyota and later perfected into the Toyota Production System (TPS) revolves around reducing cycle and takt times and eliminating non-value-adding steps from manufacturing processes. It also includes concepts like Kanban – lean scheduling, Kaizen – continuous improvement, as well as designing process flows and implementing lean management practices. In this, lean bears many similarities with the Just-in-Time manufacturing methodology.
The 8 wastes of lean manufacturing
In lean thinking, the different types of manufacturing waste are together referred to as Muda, a Japanese term meaning uselessness. Two other terms – mura and muri, are also used to describe situations where processes depart from optimal resource allocation. Muda was originally grouped into 7 categories: Transportation, Inventory, Motion, Waiting, Overproduction, Overprocessing, and Defects. Skills was later added as the 8th waste. This gave rise to the phrase TIMWOODS – an acronym that has become synonymous with driving lean efficiency.
In recent years, another phrase has emerged that regroups the 8 wastes into a more memorable acronym DOWNTIME. According to this, the 8 wastes of lean manufacturing are:
- Defects
- Overproduction
- Waiting
- Non-utilized talent
- Transportation
- Inventory
- Motion
- Extra-processing
Next, let us look at each of the 8 wastes in more detail.
Defects
Defect waste is the loss of value that occurs when a product does not meet quality standards or customer specifications or is otherwise unfit for use. Because the defective item will take extra processing to rework or often needs to be scrapped altogether, this results in lost time, resources, and money.
Defective waste can be caused by many factors like poor item design, a highly complex or excessive variation in the manufacturing process, use of sub-par materials, insufficient training of assigned employees, unnecessary handling, improper storage, etc.
Overproduction
Overproduction occurs when more goods are produced than are actually needed in a given time. This can be due to inaccurate demand forecasting, badly optimized production schedules, ineffective workstation setups, etc. It can also result from opting for a just-in-case approach instead of a just-in-time one. For example, when an item’s safety stock runs out once due to a random customer demand spike and is then set consistently too high thus creating an unnecessary surplus.
Overproduction may also result from a temptation to avoid idling workstations or employees. Companies utilizing “push”-type manufacturing workflows like make-to-stock – in which goods are produced in anticipation of sales – need to be especially vigilant in avoiding overproduction.
Waiting
The waste of waiting is increased overhead cost that arises from co-dependent workflows and routings being unevenly synchronized. In other words, it is the loss of efficiency from items waiting their turn in production queues and WIP inventory. This mostly occurs due to insufficient production planning or badly organized inventory or warehouse management practices.
Waiting results in production bottlenecks, unplanned downtime, and falling capacity utilization rates, all of which increase production costs and stretch lead times. For example, when components take longer to arrive at a workstation than the workstation takes to complete a cycle – it is left idling while it waits for the next batch.
Non-utilized talent
Non-utilized talent is the waste arising from failing to recognize and fully utilize employee skillsets and appointing them to mismatched tasks. It mostly occurs when employees are not allowed to self-govern at all, if managers are made to micro-manage too many aspects of employee tasks, or if employee inputs are not taken into consideration.
This leads to underutilization, overlooked opportunities, skillsets remaining hidden, and poor engagement. Non-utilized talent was not included among the original 7 wastes. It came to be recognized as a key driver of manufacturing inefficiency and addressing the other wastes in later years.
Transportation
This waste is defined as the lost time and efficiency from the unnecessary moving of raw materials, WIP inventory, or finished goods. Transporting goods as such does not add value that customers are willing to pay for. This waste is mostly caused by poor warehouse layouts or route and production line planning.
A prominent example is when sequential workstations fail to be positioned appropriately, like in a cellular layout, and extra effort is needed to move components from one to the other. Next to longer lead times and needless work, excess transportation can increase the wear and tear of inventory and increases the risk of defects and damage.
Inventory
Inventory waste is defined as any kind of accrued overhead arising from excess stock. Essentially, all inventory that is not moving toward exiting the pipeline as closed sales, constitutes tied-up cash and accumulates overhead. Whether it’s raw materials, WIP, or finished goods, excess stock is caused by ineffective inventory management and optimization.
Overstocking inevitably raises storage costs and congests the warehouse. What’s more, the excess stock may lose its quality and value over time and is at risk of becoming dead stock. Overstocking can occur for any number of reasons like overestimated safety stock levels, an overly optimistic or faulty demand forecast, over-purchasing due to tempting discounts on bulk purchases, improper tracking practices, etc.
Motion
Motion waste should not be confused with transportation waste. Motion waste is the needless action that employees and equipment undergo when creating products. It is mostly caused by unergonomic workstation layouts and machinery placement, or poor process documentation and checklists.
Motion waste results from employees having to needlessly walk to, reach or bend down for, lift, or carry tools and items. It may be hard to spot but can quickly add up to a huge time loss, especially for repetitive tasks. Motion waste leads to low worker safety, productivity, repetitive strain injuries, and even loss of motivation.
Extra-processing
This waste is generated in instances where workers’ skills or equipment is of a higher grade than is required to produce a specific good. Also, if products are made out of raw materials with higher capacities than the product requires, or if there are extra steps in a product’s routing that do not add value that customers are willing to pay for.
Like many others on this list, extra-processing waste results in raised production costs and elongated lead times. Overqualified employees cannot create value on par with their compensation, otherwise, it would be a case of non-utilized talent. Similarly, using high-precision machinery for simple processing negatively affects its rate of return and depreciation.
How can manufacturing software help reduce waste?
The lean way encompasses many more principles than simply awareness of the different types of manufacturing waste. Whether a company wants to “go lean” or not, however, a critical look at the 8 wastes can provide valuable insight into improving overall efficiency.
Perhaps the best single way to fundamentally reorganize or address shortcomings of a manufacturing operation in terms of efficiency is by implementing manufacturing software. To end this article, here are four key ways in which manufacturing software helps address the 8 wastes of lean manufacturing.
- Process improvement and automation. Manufacturing software, especially ERP/MRP systems, automate large parts of the manufacturing process. An overall reduction in manual processes and inputs saves substantial amounts of time and decreases the chance of human error. It also means fewer menial tasks for workers, leading to increased employee satisfaction. By automating order management, requirement calculations, reporting, etc., many processes can also be redesigned to be more efficient from the ground up.
- Real-time, data-driven, decision-making. MRP/ERP software unifies the whole manufacturing operation into a single, data-driven digital ecosystem. Every input and process is recorded and made available system-wide in real-time. This gives managers a birds-eye-view, simplifying spotting bottlenecks, increasing quality control, and taking the guesswork out of planning phases. Manufacturing software uses a perpetual inventory system which enables continuous and up-to-date info on inventory and shop-floor movements. This helps keep production costs in check and also enables near-automatic product cost and lead time calculation.
- Production scheduling. One of the key ways in which MRP/ERP systems help reduce waste is by optimizing production schedules. By analyzing customer demand, inventory levels, and production capacities, these systems generate accurate and interactive production schedules. This helps to ensure that production is always aligned with customer demand, and time and resources are used optimally. Good MRP systems also offer a host of tools for production planning and can easily be set up to manage pull-type workflows.
- Inventory optimization and traceability. By matching procurements with real-world material demand, MRP/ERP systems significantly reduce the risk of overstocks or stockouts. As manufacturing software provides real-time data on inventory levels, stock movements, and shop-floor processes, traceability is substantially improved. This helps to avoid both inventory and transportation waste and greatly improves overall efficiency.
Key Takeaways
- In the lean manufacturing methodology, developed chiefly within the Toyota Production System, waste is described as any step within the manufacturing process that does not create value for the customer.
- There are 8 principal lean manufacturing wastes, grouped by the areas in which it occurs in manufacturing. In lean terms, they are together known as muda.
- The original 8 wastes consisted of Transportation, Inventory, Motion, Waiting, Overproduction, Overprocessing, Defects, and Skills. This created the acronym TIMWOODS, a phrase that has become synonymous with lean efficiency.
- In recent years, the wastes have been regrouped into a different, more intuitive acronym – DOWNTIME: Defects, Overproduction, Waiting, Non-utilized talent, Transportation, Inventory, Motion, and Extra-processing.
- While the lean way comprises a set of many other efficiency and waste reduction oriented principles, which companies might or might not want to consider, anyone looking to improve their operational efficiency can do well to analyze the 8 wastes.
Frequently Asked Questions
The 8 wastes of lean manufacturing are:
- Defects
- Overproduction
- Waiting
- Non-utilized talent
- Transportation
- Inventory
- Motion
- Extra-processing
What is the acronym for the 8 wastes?
There are two common acronyms for the 8 wastes in lean manufacturing. The original acronym is TIMWOODS, and consists of Transportation, Inventory, Motion, Waiting, Overproduction, Overprocessing, Defects, and Skills. In recent years, another acronym has emerged, which groups the 8 wastes as DOWNTIME: Defects, Overproduction, Waiting, Non-utilized talent, Transportation, Inventory, Motion, and Extra-processing.
What is waste in lean manufacturing?
In lean manufacturing, waste is seen as anything that does not add value to the customer. It can stem from anything such as poor storage layouts, unnecessary processing, overqualified employees, the extra time it takes for raw materials to get to a workstation, etc. Waste reduction is primarily seen as a means for reducing cycle and lead times, and increasing the efficiency of processes.
This article was originally published on the MRPeasy blog.
The content & opinions in this article are the author’s and do not necessarily represent the views of ManufacturingTomorrow
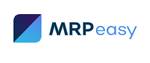
MRPeasy
MRPeasy is a seriously powerful and easy to use ERP software for small manufacturers that gives you everything you need to manage your manufacturing and distribution processes. Integrating sales, procurement, inventory, production, finances, and your team, it provides you with an accurate real-time overview of your operations. MRPeasy is trusted by 1800+ small manufacturers worldwide, 700+ of which are based in the US and Canada. Our users report a 54% average improvement in the overall performance of their business and a 42% increase in on-time deliveries. Try for free, no credit card needed.
Other Articles
BOM Management Expert Guide for Growing Manufacturers
Scottish Chemical Manufacturer ‘Struck Gold’ with Manufacturing ERP Software
5 Most Common Small Manufacturing Challenges According to Consultants
More about MRPeasy
Comments (0)
This post does not have any comments. Be the first to leave a comment below.
Featured Product
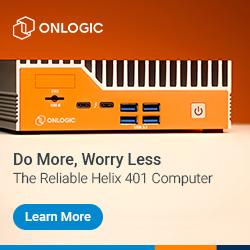