Machine monitoring can be a particularly attractive priority due to its low investment options, both in terms of pricing and connectivity, as well as rate of return.
How to Compare Machine Monitoring Software with These 3 Questions

Article from | Shop Floor Automations
As manufacturers continue to seek alternatives to overcome the labor shortage, automation remains at the core of corporate strategy. Automation priorities can take the form of cobot programming, networking CNC machines for NC program transfers and machine monitoring to capture and improve upon Overall Equipment Effectiveness (OEE), among others.
Machine monitoring can be a particularly attractive priority due to its low investment options, both in terms of pricing and connectivity, as well as rate of return. But, with so many choices available today, how do you decide what is the best machine monitoring solution for your manufacturing operations? You’ve come to the right place. As one of the leading manufacturing integrators in North America, Shop Floor Automations has over 24 years of experience in sourcing, installing and supporting shop floor technologies to keep your production lines moving optimally.
After reading this blog posting, you’ll have a better sense of the significant differences between solutions and how to weigh those differences against your own key criteria to properly compare machine monitoring software.
Vetting Equipment Monitoring Software for Your Manufacturing Operations
In essence, machine monitoring software helps your manufacturing company to increase efficiency, productivity and profitability by automatically tracking the data your shop floor equipment produces when it’s running – and especially when it’s not. Not all machine monitoring is created equal, however. The list below shares some common distinctions related to equipment monitoring software and questions that should be a part of your vetting process as you compare machine monitoring software solutions.
- How can your software support legacy and manual machines? Modern equipment often comes equipped with “plug and play” connectivity, which can make the equipment monitoring installation a relatively simple process. Manual machines, like saws and grinders, and older CNC equipment, however, tends to lack these capabilities. Some machine monitoring solutions are not able to natively support this type of equipment at all. Other systems can but require extensive hardware and consulting to get the machine online. Even so, issues may prevail well after initial installation. These issues can necessitate further technical troubleshooting to consume valuable time and effort, and potentially delay your company’s ability to realize a favorable Return on Investment (ROI). By identifying the machine monitoring software that cannot support all of your existing equipment upfront, you lessen the likelihood of purchasing “shelfware,” that is, software that goes unused, a reference to the age when software came packaged in disks and was stored on physical shelves in offices.
- What are my licensing options? Software-as-a-service (SaaS) subscription models are ubiquitous these days, but that doesn’t mean they’re a fit for every manufacturing environment. An ideal machine monitoring system should offer transparent options – whether you need an on-premise deployment, multi-term pricing, various combinations of flexible user levels or user license scalability to accommodate demand peaks and valleys – to suit your unique needs. Most of all, your ongoing satisfaction should be guaranteed. If the machine monitoring solution isn’t meeting your requirements, you should have the freedom to end your usage within a 30-day period.
- Who connects, installs and supports my equipment monitoring solution? Your manufacturing operations can be complex; the implementation and support of your monitoring software shouldn’t be. The process of connecting equipment, particularly legacy or manual equipment, can take effort, time and personnel to initially set up – especially if the responsible parties lack expertise. There are also ongoing adjustments necessary, such as new equipment connections, the troubleshooting of any issues that arise, integration assistance and tweaks to processes to take advantage of software feature enhancements, that warrant the need for a manufacturing integrator to minimize disruption and keep your equipment data flowing.
The process of connecting equipment, particularly legacy or manual equipment, can take effort, time and personnel to initially set up – especially if the responsible parties lack expertise. An experienced manufacturing integrator that can source, implement and support a scalable machine monitoring solution can serve as an effective resource to set up new equipment connections, troubleshoot issues that may arise and help integrate machine data with ERP, for example.
For these three reasons and more, you should see that a comparison of machine monitoring software ought to go well beyond functionality assessments. Both your equipment monitoring solution and manufacturing integrator should be able to adapt to the many changes your organization will undergo in the months and years to come – and be an essential part of that change. Learn more about how Shop Floor Automations is the entrusted integrator for manufacturers with 5 to 75-plus pieces of equipment by contacting a representative today.
The content & opinions in this article are the author’s and do not necessarily represent the views of ManufacturingTomorrow
Comments (0)
This post does not have any comments. Be the first to leave a comment below.
Featured Product
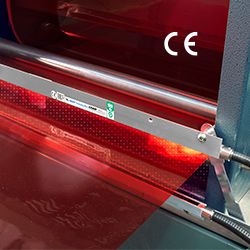