With a variety of post-processing technologies available, it is essential to understand their capabilities and limitations. In this article, we will benchmark different post-processing technologies and explain why mass finishing technologies are the best fit and the most efficient solution.
AM Post-processing: Benchmarking Alternative Technologies
Colin Spellacy, Head of Sales, | AM Solutions UK
Additive manufacturing (AM) has been a game-changer in the manufacturing landscape, offering unparalleled design freedom, material efficiency, and rapid production times. Despite these advantages, post-processing remains a critical aspect of ensuring the desired surface finish, accuracy, and functionality of AM parts. With a variety of post-processing technologies available, it is essential to understand their capabilities and limitations. In this article, we will benchmark different post-processing technologies and explain why mass finishing technologies are the best fit and the most efficient solution.
AN OVERVIEW
Post-processing encompasses various techniques to improve the surface quality, dimensional accuracy, and mechanical properties of printed parts. There are four common post-processing technologies: hand finishing; CNC machining; chemical finishing; and mass finishing technologies
Mass finishing technologies can be adapted to various shapes and sizes of parts, making them a versatile post-processing method for various AM applications.
Hand Finishing. Hand finishing is a traditional AM post-processing method that involves manual sanding, grinding, and polishing to achieve the desired surface finish. The key advantages of hand finishing include the ability to achieve precise, custom finishes that may be difficult to achieve with automated methods, as well as the ability to quickly identify and correct errors or imperfections in the part. However, hand finishing can also be time-consuming and labour-intensive, leading to increased costs and reduced efficiency. Additionally, the consistency of the finish may vary from part to part, depending on the skill and experience of the operator. As such, hand finishing may be suitable for small-scale or custom projects where precision is critical, but may not be ideal for large-scale or high-volume production due to its time and labour requirements.
CNC Machining. CNC machining is a subtractive manufacturing process that can be used as a post-processing method for AM parts. The key advantages of CNC machining include the ability to achieve high precision and accuracy, even for complex geometries. CNC machines are also highly customizable and can accommodate a wide range of materials, including metals, plastics, and ceramics. Additionally, CNC machining can be automated, reducing labour costs and increasing production efficiency. However, there are also some disadvantages to using CNC machining as a post-processing method for AM parts. One of the main drawbacks is the high cost of equipment and setup, which can be a barrier to entry for some manufacturers. Additionally, CNC machining may not be suitable for parts with intricate internal features or fine details
Chemical Finishing. Chemical finishing is a post-processing method that involves treating AM parts with chemical solutions to alter the surface finish or properties of the part. The key advantages of chemical finishing include the ability to achieve precise and uniform finishes across complex geometries, as well as the ability to alter the material properties of the part, such as corrosion resistance or biocompatibility. However, there are also some disadvantages to using chemical finishing as a post-processing method for AM parts, key among which is that the effectiveness of chemical finishing may depend on factors such as the material of the part and the specific chemicals used, which can make it difficult to achieve consistent results across different parts or applications. In addition, chemical finishing may not be suitable for parts that require precise tolerances or that have complex internal features, as the chemical solutions may not be able to penetrate or reach these areas. Overall, while chemical finishing can be an effective and cost-efficient post-processing method for additive manufactured parts, careful consideration must be given to the potential drawbacks and limitations of this approach.
Mass Finishing Technologies. Mass finishing technologies, such as vibratory and centrifugal finishing, utilize abrasive media and mechanical energy to smooth and polish printed parts. These processes are highly scalable, and capable of handling large volumes of parts simultaneously. They are also versatile, working with various materials and part geometries. Moreover, mass finishing technologies are cost-effective, fast, and environmentally friendly.
WHY MASS FINISHING?
Mass finishing technologies offer several advantages over other post-processing methods, making them the preferred choice for AM parts.
Scalability. Scalability is important for several reasons. First, mass finishing enables the treatment of a large volume of parts at once, which can significantly reduce the time and labour required for finishing compared to treating parts individually. This can improve overall efficiency and reduce production costs. Also, mass finishing ensures consistent finishing results across a large batch of parts, which can be difficult to achieve with manual or individual finishing methods. This can help ensure that parts meet specified requirements for surface finish, roughness, and other critical parameters.
Treating a large batch of parts simultaneously can also help reduce variability in the finishing process, as each part is treated in the same way for the same duration. This can help reduce the risk of defects or inconsistencies in the finished parts.
The scalability of mass finishing also makes it a cost-effective method for finishing a large volume of parts, as the cost per part decreases as the batch size increases. This can be particularly important for industries such as aerospace and automotive, where large quantities of parts are required.
Material Compatibility. Mass finishing technologies work with a wide range of materials, including metals, polymers, and ceramics. This versatility enables manufacturers to use a single post-processing method for various AM applications, simplifying the production process. By using a single post-processing method for multiple materials, manufacturers can reduce the need for separate equipment or processes for each material. This can help reduce equipment costs, space requirements, and maintenance needs.
Using a single post-processing method across multiple materials can also help improve process control and consistency. Manufacturers can develop a standardized process for finishing that can be applied to different materials, reducing variability and improving overall quality.
In addition, standardizing on a single post-processing method can help increase overall efficiency by reducing the need for additional equipment, reducing setup times, and streamlining the finishing process. This can help manufacturers produce parts faster and at a lower cost.
Mass finishing technologies can be adapted to various shapes and sizes of parts, making them a versatile post-processing method for various AM applications. This means that manufacturers can use mass finishing to finish a wide range of parts, regardless of their material, shape, or size.
Uniformity and Consistency. Mass finishing technologies can achieve uniform surface finishes across complex part geometries, even in hard-to-reach areas. This consistency ensures that all parts meet the required specifications, enhancing product quality and reducing the need for additional finishing processes.
AM parts often have complex geometries with hard-to-reach areas that can be difficult to finish with traditional methods. Mass finishing technologies, however, can achieve uniform surface finishes across the entire part. Achieving uniform surface finishes across complex geometries is critical to ensuring product quality. By achieving consistent finishing results, mass finishing technologies can help ensure that all parts meet the required specifications for surface finish, roughness, and other critical parameters.
Mass finishing technologies can also help reduce variability in finishing results, even across complex geometries. This can help reduce the risk of defects or inconsistencies in the finished parts, improving overall quality. Achieving consistent surface finishes across complex geometries can reduce the need for additional finishing processes, such as hand finishing or secondary machining. This can help reduce the time and cost required for finishing, improving overall production efficiency.
It can also improve the aesthetics of the finished parts, making them more visually appealing. This can be particularly important for consumer-facing products or parts that will be visible in the final product.
Reduced Labour Costs. Mass finishing technologies are largely automated processes that require minimal manual intervention, reducing labour costs and the potential for human error. The automation of mass finishing technologies can also increase efficiency, as machines can work continuously, without breaks or interruptions. This can help reduce the time and cost required for finishing, improving overall production efficiency.
Mass finishing technologies can also incorporate quality control features, such as sensors and feedback mechanisms, that can detect and correct errors or deviations in the finishing process. This further reduces the potential for human error and improves overall product quality.
PARTNERHIP & COLLABORATION
It is important when choosing a mass finishing post-processing technology supplier to locate one with the expertise in process development and optimization that is vital in achieving repeatable end results. Expert engineers should be able to work closely with clients to develop tailored post-processing solutions that optimize cycle times, minimize waste, and ensure the desired surface finish and dimensional accuracy.
Suppliers should also demonstrate a focus on providing exceptional customer support, and also offer a range of services, including equipment installation, training, maintenance, and troubleshooting. Such commitment to customer satisfaction ensures that clients can rely on their chosen supplier for ongoing assistance and expertise.
The chosen supplier should also have expertise that spans a wide range of mass finishing technologies. By offering a comprehensive portfolio of products and services, suppliers effectively become a one-stop-shop for addressing the diverse post-processing needs of their clients.
It is also advantageous if your chosen mass finishing post-processing technology supplier offers a wide range of abrasive media and finishing compounds, specifically tailored to the needs of AM applications. By understanding the unique characteristics of different materials and part geometries, a supplier should be able to provide customized technology / media solutions that yield optimal surface finishes while preserving part integrity.
About Colin Spellacy
Colin Spellacy is the Head of Sales at Rösler UK. AM Solutions is part of the Rösler Group, which has been a leading expert in the field of surface finishing for more than 80 years, and offers the most extensive portfolio of mass finishing systems, shot blasting, consumables, and services in the world. Renowned companies from a wide range of industrial sectors trust in Rösler products and services. AM Solutions was created from this rich heritage to apply the knowledge and expertise gleaned from 8 decades working in traditional manufacturing processes to the emerging and disruptive area of additive manufacturing. AM Solutions’ specialist team is able to design an AM post processing system that is perfectly suited to specific applications.
The content & opinions in this article are the author’s and do not necessarily represent the views of ManufacturingTomorrow
Comments (0)
This post does not have any comments. Be the first to leave a comment below.
Featured Product
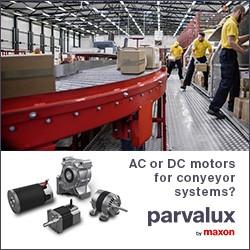