Metal 3D-printed parts can be produced at higher production rates with impeccable quality by implementing advanced quality control and post-processing techniques.
Enhanced Quality Control and Post Processing for Metal 3D Printing
Article from | Wayken Rapid Manufacturing Limited
Enhanced Quality Control and Post Processing for Metal 3D Printing
Metal 3D-printed parts can be produced at higher production rates with impeccable quality by implementing advanced quality control and post-processing techniques. You will be able to produce top-quality metal parts with unlimited design freedom at relatively lower costs. Besides utilizing metal machining services, implementing in-house quality control will also level up your product quality.
Let's explore four proven techniques to enhance quality control and post-processing of 3D-printed metal parts for superior part quality.
Crisp Tolerance for Metal Parts with CNC Machining
Using CNC machining in post-processing 3D printed metal parts can help achieve high dimensional accuracy, smooth surfaces, and tight tolerances. The layer-by-layer deposition process in 3D printing leaves rough surfaces. The roughness is usually more than 200 µin Ra; However, CNC machining in post-processing can help smooth it up to 63 µin Ra.
CNC machining removes excess material at a higher precision level without affecting part dimensions. CNC machining allows material-specific adjustments to retain the part's intended material properties. 3D printed parts could be refined using an adaptive toolpath at specific cutting speeds, feed rates, and depth of cut according to the material's thermal properties. The temperature control during the process also helps mitigate heat-induced distortions. Resultantly, the finest quality and surface finish could be achieved with crisp tolerances.
Frequent Powder Testing to Ensure Compliance with Chemical Composition
Frequent testing, analysis, and traceability of powder material are crucial to ensure part quality. The material must be tracked on a single-lot basis from raw form to the final product, with each step documented and validated. It ensures material integrity and helps detect the slightest variation in the composition during the process.
For analysis, standardize a sampling process to minimize bias. Then use contemporary techniques like X-ray fluorescence (XRF), optical emission spectroscopy (OES), and inductively coupled plasma (ICP) analysis. Account for potential variations and document the results for comparison and future use. Make sure to follow industry-specific regulations and clearly determine the acceptable variation ranges and tolerances.
Moreover, real-time monitoring through In-situ sensors and other monitoring systems also ensures compliance with chemical composition. If the variation is detected during the process, corrective measures can be taken instantly. Accurate information on composition also helps optimize the process; keeping a record of thermal properties and mechanical changes allows for precise adjustments to printing parameters and post-processing steps.
Eliminating Stress and Warping Utilizing Heat Treatment
Heat treatment effectively eliminates residual stresses and warping due to the rapid cooling of 3D-printed metal parts. Multiple techniques can be used depending on a material specification, such as Stress Relief Treatment, Hot isostatic Pressing (HIP), Solution Annealing, and Aging. These processes harden and strengthen the metal part to revive its mechanical integrity. The ASTM 3301 standard also emphasizes heat treatment of 3D-printed metal parts to ensure optimal quality.
- Stress Relief Treatment: It can eliminate internal stresses generated during printing. The treatment involves multiple cycles of uniform heating and gradual cooling per the part specifications. It helps minimize the risks of distortion, cracking, or premature failure. The part is reinforced with increased toughness and fatigue resistance.
- Hot isostatic Pressing (HIP): The process consolidates, solidifies, and eliminates defects in internal material structure. The part is heated at high pressure and uniformly applied from all directions, which heals the internal structure, reducing porosity and eliminating cracks or inclusions. Resultantly, the part's strength, ductility, and other mechanical properties are enhanced.
- Annealing: It induces changes in the material's microstructure to achieve higher strength and ductility in the part. The part is heated at a high temperature and cooled down rapidly to relieve internal stresses. It also reduces porosity, maintaining the part's structural integrity.
- Aging: The process hardens the metal part and introduces fine precipitates for higher fatigue strength. It is best used for specific alloys, aluminum-based, copper-based, super alloys, etc. The aging process also significantly impacts material properties, such as corrosion resistance and electrical conductivity.
Heat treatment often introduces surface irregularities or roughness. It is recommended to send parts for CNC milling services to enhance the surface finish further and refine the part's final shape and features. The slight deviation in dimensions or improved room for tolerances could also be eliminated with CNC milling service. Where heat treatment removes internal stresses and mitigates the risk of warping, distortion, and other deformation issues, CNC machining further enhances the surface finish.
Trial & Error for Efficient Dealing of Additive Part Structure
Trial and error is an efficient approach to achieve optimal results with minimal effect on the additive part structure during post-processing. For instance, use an iterative approach when CNC machining metal parts adjust and re-adjust machining parameters until the best outcomes are achieved.
Try to implement newer strategies considering toolpath optimization, cutting direction, and tool selection. Keep every step and parameter on record to compare. Choose the best approach that helps maintain the structural integrity of the part.
In the case of feedstock testing, trial and error opens doors for innovation. Where you optimize the process by frequent testing and analyzing trends, you can also develop new alloys and custom compositions. Using novel materials can help achieve better printability, structural integrity, and improved resistance.
Heat treatment has the most significant impact on material properties. Following data sheets or laboratory results doesn't bring desired results during manufacturing. The best way to achieve superior part quality is to design a heat treatment procedure from trial and error.
Use an iterative approach to adjust heat treatment parameters, such as temperature, duration, and cooling rates. Monitor the process with visual inspections and make dimensional measurements; also use non-destructive tests to ensure mechanical and material properties improvement.
Then validate the process using mechanical testing and microstructural analysis. If the part structure is maintained with enhancement in strength and mechanical properties, document the parameters for reuse.
Conclusion
Post-processing 3D-printed metal parts are crucial to producing high-quality parts with great dimensional accuracy and structural integrity. Additional machining and rigorous testing can help elevate part quality while maintaining material properties. Integrating CNC machining with metal 3D printing will allow you to cater to the demands of profitable markets and industries ranging from aerospace and medical to the precision industry.
The content & opinions in this article are the author’s and do not necessarily represent the views of ManufacturingTomorrow
Comments (0)
This post does not have any comments. Be the first to leave a comment below.
Featured Product
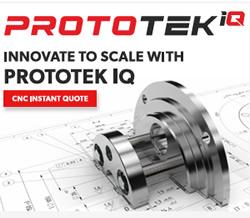