Products have become more complex with additional software and configuration options to meet customization demands; simultaneously, BOMs have also become more complex.
Mastering Configurable BOM Complexity
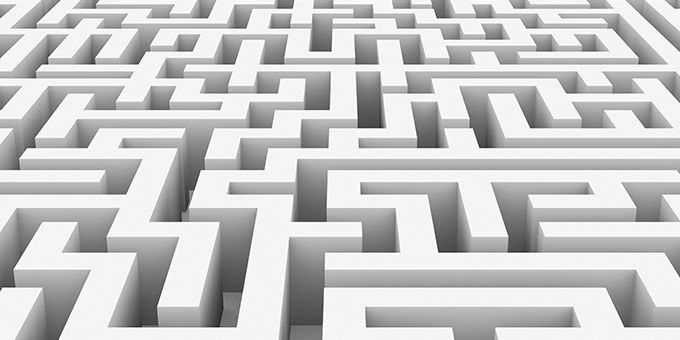
Daniel Joseph Barry, Vice President of Product Marketing | Configit
Bills of Materials (BOMs) are the central pillar of manufacturing processes, extending well beyond the engineering domain to capture the lifecycle of the product as-planned, as-designed, as-manufactured and as-delivered. Products have become more complex with additional software and configuration options to meet customization demands; simultaneously, BOMs have also become more complex.
Manufacturers have adopted different strategies to manage this complexity. Some prefer to have a single “universal” BOM capturing all information related to the product in one hierarchical, multi-level structure together with “views” for different users and lifecycle stages. The drawback with this approach is that because some complex products can have hundreds of thousands of parts, these universal BOMs lead to performance challenges, not to mention management challenges.
An alternative strategy is to work with multiple BOMs, sometimes generated in different systems, for each stage of the product delivery process and lifecycle. This has led to a wide range of BOM varieties, such as Engineering BOMs (eBOMs), Manufacturing BOMs (mBOMs), and Service and Sales BOMs (which can both be referred to as sBOMs, depending on the context). This ensures that different users at different stages of the product delivery process only need to see the information that is pertinent to their role and thus lowers complexity for the individuals. However, the flipside is that it can lead to other challenges with respect to managing changes and ensuring that all BOMs are correct.
All of the above issues lead to complexity challenges, no matter the strategy adopted. Then on top of that, the need to support customization and personalization adds another layer of complexity.
The challenges of customization
Customization and personalization are not new trends and today, both B2B and B2C customers expect these options. Nevertheless, they still pose challenges to manufacturers, especially with respect to how quickly they respond to requests for quotes from customers.
One of the underlying reasons for these challenges is the continued reliance on siloed systems and paradigms that were originally designed for mass manufacturing of standard products. Managing the complexity of configuring products, systems and services to meet specific needs requires new ways of thinking, but not necessarily a forklift replacement of existing systems.
This challenge is best highlighted by Request for Quote (RFQ) response times that can often take weeks. This typically requires a great deal of manual engineering work to ensure that a specified configuration from the customer can be used to filter the Configurable BOM (cBOM) selection conditions and generate a valid 100% BOM to be offered back to the customer. This isn’t efficient and it doesn’t induce “delight” in the customer.
Bringing a configuration lifecycle management approach
Configuration Lifecycle Management (CLM) solutions have already tackled similar challenges for product models in support of both product configuration and Configure-Price-Quote (CPQ) solutions. Product models capture the configuration choices that can be offered to customers as well as the rules and constraints governing these choices. This is very similar to the cBOMs where each configuration choice is defined for each BOM item, and the rules and constraints are captured as selection conditions.
What is different about CLM is the technology used to implement it. From the beginning, CLM solutions were designed to support enormous data sets and enable the validation of a specific configuration instantaneously. For example, a typical automobile could be configured in up to 1021 different ways and all these configuration options need to be stored and accessible in support of an interactive customer product configuration process.
CLM for cBOMs
By applying the same approach to cBOMs, it is possible to reduce the time it takes to explode and solve a cBOM from weeks to seconds. Not only does this dramatically reduce the time it takes to generate a BOM for a specific configuration, but it also opens new opportunities for designing and testing cBOMs that will increase the efficiency and accuracy of the process.
One or more of the cBOMs can be associated with a specific product model. This enables configurable eBOMs, mBOMs and sBOMs to be associated with a product model, which includes all of the rules, constraints and time-based effectivity rules associated with the product. These are similar to the selection conditions that are applied to each BOM item.
New opportunities for product design
For the product designer, this offers a range of new possibilities. Typically, the product model and cBOM would be developed in isolation and compared late in the design process. Now, it is possible to develop the cBOM and product model simultaneously, ensuring that the same rules and constraints are applied to both at the same time. This ensures that there are no inconsistencies between what is presented to customers during the product configuration phase and what is provided in the quotation and delivery phase.
It is also possible to solve a cBOM for a partial configuration. This enables designers to continuously generate configured BOMs for different configurations during the design process, iteratively testing the efficacy of selection conditions. The designer can, at the same time, take advantage of the rich test and verification environment available for product models, such as solution space generation, to understand the landscape of choices being offered to customers based on the rules and constraints defined.
The end result is a faster design process for cBOMs that are closely aligned with product models and a lower risk of errors and misalignments.
Another advantage of partial configuration is the ability to support Engineer-to-Order (ETO) processes. With a fully automated Configure-to-Order (CTO) process, all configuration choices are resolved and a complete 100% BOM is generated. But for some companies, it is desirable to leave some options open for further customization by partners or on-site. With the ability to support partial configuration, it is possible to generate what is termed a “120%” BOM where certain BOM item options are not defined, supporting this process.
Mastering complexity
By leveraging product models and CLM systems and technology, BOM designers now have new tools and paradigms in which to manage the complexity of both BOMs and configuration. This can provide inspiration for new ways of working and a new approach to tackling some of the remaining challenges associated with BOM management.
The content & opinions in this article are the author’s and do not necessarily represent the views of ManufacturingTomorrow
Comments (0)
This post does not have any comments. Be the first to leave a comment below.
Featured Product
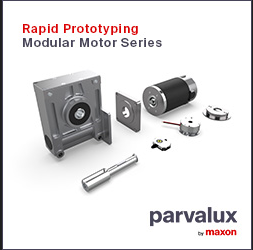