Using the Essentium High Speed Extrusion (HSE™) 180 ST 3D Printing Platform and Essentium PCTG-Z, Additive at Scale partnered with Blues Wireless to design and manufacture 100 pilot units for an asset tracking solution for a multinational chemical company in just 60 days.
Additive at Scale Uses Essentium Technology to Create an Asset Tracking Solution in 60 Days
Case Study from | Essentium, Inc.
Using the Essentium High Speed Extrusion (HSE™) 180 ST 3D Printing Platform and Essentium PCTG-Z, Additive at Scale partnered with Blues Wireless to design and manufacture 100 pilot units for an asset tracking solution for a multinational chemical company in just 60 days.
SITUATION OVERVIEW
Additive at Scale, a premier end-to-end solution provider, offers engineering and scale-up manufacturing services to clients from a wide spectrum of industries. Using their out-of-the-box manufacturing methods, they strategically manage client demands across the entire product life cycle and accelerate commercialization strategies.
Partnered with Blues Wireless and their data-pump solution, the Notecard and Notecarrier, the engineers at Additive at Scale worked with IoT developers to create an asset tracking solution for various applications. This device offers GPS capabilities, an onboard accelerometer, and allows the end-user to pump data to the cloud without Wi-Fi or Bluetooth connectivity, making it perfect for robust asset tracking. However, most end-users who are interested in developing an IoT solution don’t have electronic enclosures on-hand and are limited by off-theshelf solutions. These electronic enclosures often require a specific form factor, custom PCB mounts, external plugand-play ports, displays, and a rugged design for outdoor installations.
Like many end-users adopting this asset tracking solution, one of Additive at Scale’s customers, a multinational chemical company, faced electronic enclosure limitations. The goal for this specific project was to support and assist with an asset tracking solution for fleet management and monitoring of 18-wheeler chassis that transport chemicals.
In the end, Additive at Scale designed an electronic enclosure complete with an O-ring groove and seal, threaded inserts, and custom PCB mounts, and printed 100 units for their pilot phase with an Essentium HSE 180 ST 3D Printer
THE CHALLENGE
To solve this problem, Additive at Scale tested several off-theshelf enclosures but quickly realized that a custom ruggedized solution was necessary and began designing, prototyping, and scaling production.
Functionally, the electronic enclosure needed to house the Notecard and Notecarrier, provide ingress protection, and easily mount to the chassis. In addition, the client requested that the enclosure be white, UV resistant, weatherproof, and eventually approved through third-party testing for Class 1 Division 2 certification. With these constraints, Additive at Scale chose to leverage Essentium’s High Speed Extrusion Platform and advanced materials to complete the pilot phase of the project quickly.
THE SOLUTION
To meet the requirements set by the multinational chemical company, the Additive at Scale team chose to use Essentium PCTG-Z for its ESD-safe properties, impact strength, chemical resistance, and low cost.
“Working with Essentium’s material scientists and application engineers helped us select a material and process settings that would maximize print speed, part strength, and repeatability for this use case,” explained Madison Jones, Director of Additive at Scale. “They also offer the best ESDsafe materials on the market which in most cases, is ideal for electronic enclosures or assembly of electronics.”
In the end, Additive at Scale designed an electronic enclosure complete with an O-ring groove and seal, threaded inserts, and custom PCB mounts, and printed 100 units for their pilot phase with an Essentium HSE 180 ST 3D Printer.
BUSINESS OUTCOMES
With Essentium’s technology along with Essentium’s material scientists, service and support team, and training, Additive at Scale was able to complete the pilot phase in 60 days. Due to the success of the project, Additive at Scale has been given official vendor status and is in the process of scaling-up production.
About Essentium, Inc.
Essentium, Inc. provides industrial 3D printing solutions that are disrupting traditional manufacturing processes by bringing product strength and production speed together, at scale, with a no-compromise engineering material set. Essentium manufactures and delivers innovative industrial 3D printers, materials, software, and services, enabling the world’s top manufacturers to bridge the gap between 3D printing and machining and embrace the future of advanced manufacturing. Essentium is AS9100D certified and ITAR registered
The content & opinions in this article are the author’s and do not necessarily represent the views of ManufacturingTomorrow
Comments (0)
This post does not have any comments. Be the first to leave a comment below.
Featured Product
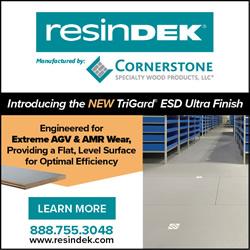