Fictiv’s robust digital supply chain infrastructure is growing every day. We have a highly vetted network of US-based additive manufacturing partners like Jabil Additive that enable customers to get the highest quality 3D printed parts delivered quickly
Expanding US-based Additive Manufacturing Services
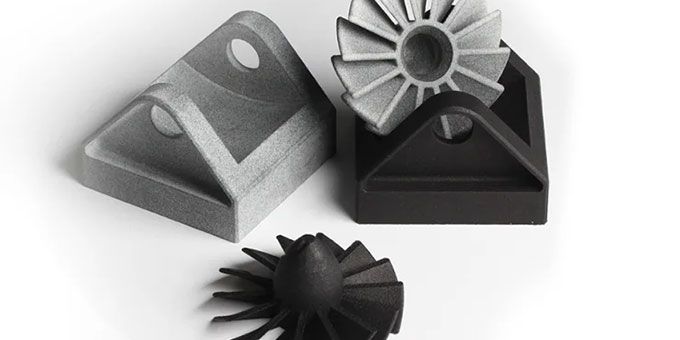
Q&A with Riley Hall, Director of Additive | Fictiv
Tell us about yourself and your role with Fictiv.
Riley Hall is the Director of Product Marketing for Fictiv. He’s involved in advocating for customers, presenting customer feedback to internal teams, and defining Fictiv’s product roadmap. Prior to joining Fictiv, he held a variety of roles in engineering, project management, and sales at Hexagon Manufacturing Intelligence, Hilti North America, and Markforged. He holds an MBA from the University of Colorado Boulder and a degree in mechanical engineering from the University of Michigan.
Fictiv recently announced expansion of 3D Printing services, machines and materials. Can you elaborate on the range of new 3D printing materials for advanced engineering applications? How do you envision these materials benefiting customers in different industries?
Our release of 14 new 3D printing materials creates more opportunities for advanced engineering applications suitable for production use cases. 3D printed parts are increasingly used in automotive parts, consumer products, medical devices, functional assemblies, jigs, fixtures, and more. What sets these materials apart is the wide array of innovative applications and design flexibility they allow. They range from high-temperature materials such as Ultem 9085, to biocompatible materials such as ABS-M30i, to Somos materials for optical clarity and water resistance. Ultimately, these materials give customers the flexibility, low production costs, and innovative and sustainable tools they need to create new products rapidly.
How will these enhancements in the Fictiv platform improve the overall customer experience, and what kind of flexibility and cost savings can customers expect to achieve with these features?
This is another important step in our overall commitment to serving as a strategic partner to our customers throughout the product development lifecycle. These enhancements enable high-quality 3D printed results for a broader range of technical requirements and applications. Improving the material selection process and adding configurations for infill density and threaded inserts gives customers confidence in all aspects of the project—from prototype to production.
Additionally, customers now have online quoting features for 3D printing on the Fictiv platform, including expanded lead time options. Customers can now specify infill density as well as threaded inserts, and improved material selection interface to determine the ideal balance between performance, lead time, and cost—all without sacrificing quality.
How do these partnerships enhance Fictiv's digital supply chain infrastructure, and what benefits will customers gain from the ability to order hundreds to thousands of parts with industry-best prices?
Fictiv’s robust digital supply chain infrastructure is growing every day. We have a highly vetted network of US-based additive manufacturing partners like Jabil Additive that enable customers to get the highest quality 3D printed parts delivered quickly (as fast as 24 hours). Customers place the order, receive design for additive manufacturability (DfAM) feedback, and then we source and manufacture the parts, all via Fictiv’s digital manufacturing platform.
Given the increasing interest in on-shoring and domestic production in the USA, how is Fictiv positioned to meet the needs of customers who are looking to source additive manufacturing and 3D printing services locally?
All of Fictiv’s 3D Printing orders are proudly manufactured in the USA. Additionally, each manufacturing partner in our network has to meet stringent quality management, intellectual property protection, and security requirements. For customers who need local, high-quality additive manufacturing options, we can source the best printing supplier for their project.
Can you share an example of a US based customer and how Fictiv has helped them improve their manufacturing process.
We have a number of customers who’ve used Fictiv 3D printing capabilities to dramatically improve their manufacturing process. One great example is Mira Labs, a company building a smartphone-powered augmented reality system. They needed high-quality, customer-ready units that were production-grade at lower volumes, so they leveraged Fictiv’s Multi-Jet Fusion (MJF) printing capabilities and were able to meet customer demand more quickly than ever before.
TransMed7 is another great example of better outcomes and more efficient processes. They’re a groundbreaking medical device solutions company that leveraged 3D printing to shorten their design and development time from weeks to days and decreased commercial product innovation from 10 to 2 years. They were ultimately able to bring five new breakthrough medical devices to market.
The content & opinions in this article are the author’s and do not necessarily represent the views of ManufacturingTomorrow
Comments (0)
This post does not have any comments. Be the first to leave a comment below.
Featured Product
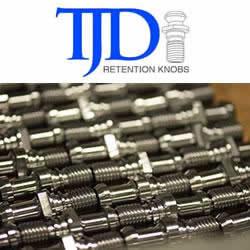