In maintaining equipment required for manufacturing processes, organizations want seamless processes and confidence in their providers. With Quickbase, Daifuku-Wynright has been able to create that peace of mind, and know that they can handle rapidly shifting challenges.
Daifuku-Wynright: Manufacturing Visibility & Control with Quickbase
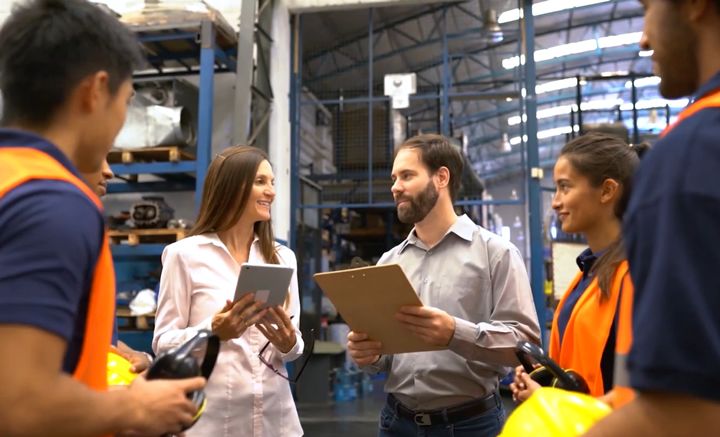
Case Study from | quickbase
Daifuku-Wynright is an established name in the manufacturing industry, focused on empowering modern manufacturers to move product safer, faster, and more affordably. Specifically, they’re focused on automated materials handling. As Jaime Townsend, Senior Manager of Resident Systems Support put it, Daifuku-Wynright creates “simplistic solutions to complex problems.”
This includes preventative and reactive maintenance to job sites, which focuses on stabilizing sites as they run or helping customers respond to changing business needs. With this involving balancing digital solutions and physical assets, doing so well requires a platform that can react to change and have the flexibility to handle this kind of dynamic work.
In maintaining equipment required for manufacturing processes, organizations want seamless processes and confidence in their providers. With Quickbase, Daifuku-Wynright has been able to create that peace of mind for their customers, and know that they can handle rapidly shifting challenges.
Daifuku-Wynright: Manufacturing Visibility & Control with Quickbase
Change management – a process of trust
For a task in manufacturing like materials handling and maintenance, organizations want to trust the tools and people they’re dealing with. The biggest issue comes with managing change – that is, ensuring that any equipment maintenance is done with foresight, communication, and efficiency.
“Any time that you're introducing change into a production system, that can be pretty daunting,” Jaime said.
Organizations may fear the worst when needing maintenance on their equipment. That can be critical for Daifuku in how they build trust in handling those communications. “We saw at times that we would have someone very eager to improve the site, but wasn’t necessarily aligned with the customer,” she added.
Eliminating this lack of alignment, and reducing anxiety in customers, comes with having the right information available at the right time. With Quickbase, Daifuku can accurately inform customers what changes may be coming to their production sites – and allow them to understand what may be on the horizon. This comes with one singular platform uniting all of the right information.
“We use Quickbase predominantly in change management, whether informing stakeholders from our company or the customer about what is coming to their live production site. Now, we can have engineers, mechanical techs, electrical techs, software developers – all different disciplines, engaging in one platform.”
With Quickbase, one form allows for Daifuku to determine what information is most relevant based on the customer’s specific situation, determining what information is most relevant and who needs to be informed of the change. That means better communication – and a better customer experience.
“We're providing more clarity on the technical change, whether it's mechanical, electrical, software related,” Jaime added. “I think also we're providing a sense of calm, which is intangible, but nonetheless important for our customers and even our own stakeholders.”
Eliminating challenges, creating peace of mind
Daifuku-Wynright can now make sure customers and internal stakeholders are on the same page with facilities management. Solving that problem means they believe in the experience they’re delivering to their customers. Just as importantly, Daifuku can share information in a way that everybody in the organization can understand.
For people with differing levels of tech-savviness, a single, easy-to-use platform allows for everybody to get on the same page quickly.
“We have hundreds of employees that we're trying to use with the platform. Pretty soon we might be in the thousands of employees. Quickbase is intuitive to use for all of those people, across different levels of understanding of technology.”
Not only can Daifuku do this in a way that is easy to understand, but it can do so with speed and agility.
“Quickbase is dynamic in that it solves a long-term problem very quickly. Because it’s malleable and can tailor to our needs, we use it for quick problems that need to be solved in a day, or addressing quickly problems that last months at a time.”
This results in customers having trust that Daifuku-Wynright will keep their equipment up to date and do so in a way that will be as minimally disruptive as possible. Now, Daifuku can work dynamically – and not get bogged down in the problems that Gray Work and stagnant processes used to bring.
“The ROI we get out of Quickbase is that ultimately, we’re eliminating a problem,” Jaime said.
As Daifuku continues to see success with Quickbase, they’re finding new opportunities to make their work more connected and controlled. For Jaime, that starts with a full project portfolio management process.
“What I'm looking to create next with Quickbase is to really organize my department. Resource management, schedule management, assigning tasks to users, risk management onsite,” Jaime said, noting that their use of Quickbase could go beyond these opportunities. “Its application is only limited by your creativity.”
The content & opinions in this article are the author’s and do not necessarily represent the views of ManufacturingTomorrow
Comments (0)
This post does not have any comments. Be the first to leave a comment below.
Featured Product
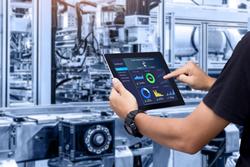