Regulatory bodies worldwide enforce stringent controls and conduct frequent audits, making it imperative for manufacturers to have a handle on every facet of their production process.
The Power of Traceability: The Ultimate Shield Against Product Recall Risks
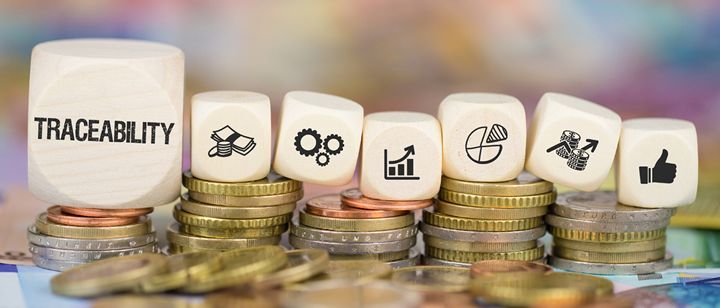
Deb Geiger, VP Global Marketing, | Aegis Software
In a manufacturing landscape defined by rigorous standards, emerging technologies, and customer demands for exceptional quality, traceability has become a paramount necessity. Regulatory bodies worldwide enforce stringent controls and conduct frequent audits, making it imperative for manufacturers to have a handle on every facet of their production process. Overlooking risks or falling short in compliance could result in severe penalties, damaging recalls, and even irreversible harm to your brand reputation.
This leads us to one critical question: How can you fortify your operations, minimize recall risks, and ensure absolute regulatory compliance? The answer for mitigating risk lies within the realm of Manufacturing Execution Systems (MES).
The manufacturing execution system benefits extend well beyond the realm of improved productivity and reduced waste, offering you a robust means to ensure traceability and, subsequently, compliance. Read on to explore how traceability functions as the lifeline of today's highly regulated industries and how it can be harnessed to effectively neutralize product recall risks.
The Grave Impact of Product Recall Risks
In industries such as aerospace, automotive, food and beverage, medical devices, consumer goods, and pharmaceuticals, the stakes are invariably high due to the extreme levels of regulations governing them. The term "recall risks" is, hence, a menacing phrase that sends a ripple of unease through these sectors. The reasons for these jitters are multifold.
Compliance with stringent safety standards and laws, the guarantee of product integrity, and a constant need for high-quality deliverables define these sectors. A product recall – arising due to factors such as non-compliance with the set standards, product defects, or quality control issues — can be an immense logistical challenge, leading to significant financial drain and irreparable damage to your brand's reputation and consumer trust. However, the repercussions don’t stop here.
There's a deeper, more serious issue at hand — safety risks to consumers. Any lapse in product quality or safety can lead to disastrous outcomes and potentially life-threatening scenarios. Consequently, it can open the floodgates for heavy legal suits and punitive regulatory penalties.
A Snapshot of a Recall Crisis
To fully comprehend the magnitude and repercussions of a product recall, let’s delve into a real-world instance that rattled the automotive industry to its core. Takata Corporation, a Japanese automotive parts company, was compelled to recall millions of vehicles due to a dangerous flaw in the airbag inflators. These faulty inflators were prone to exploding with excessive force, posing a grave risk to the driver's safety.
The recall wasn’t just significant in terms of the financial blow it dealt to the company and the palpable dent in its reputation. It was equally noteworthy for underscoring a major issue plaguing many manufacturers — a lack of end-to-end visibility and control over their supplier's manufacturing processes. Without that lack of visibility, manufacturers may be recalling more than is needed because the precision of trace is not trusted and they do not want to run the risk of defective units in the field.
The Rise of Traceability in Manufacturing
In the face of such daunting challenges, traceability in manufacturing proves to be a formidable ally. In the pre-traceability era, manufacturers faced the herculean task of maintaining comprehensive oversight over their entire production line and supply chain. Often, they were blindsided by product issues or potential compliance risks in manufacturing, which surfaced only when it was too late to take corrective action.
However, the incorporation of traceability components within a Manufacturing Execution System (MES) solution marks a paradigm shift in this scenario. These components empower you with real-time, transparent visibility into every stage of production — from sourcing raw materials, through tracking materials down to single piece and its entire history and lot information and associating that without error to each final end-unit produced. This granular insight enables you to swiftly identify potential issues and implement remedial measures. As a result, it minimizes the risk of product recalls, thus circumventing the associated financial losses and reputational damage.
Clearing the Fog of Compliance Misconceptions
The ever-growing emphasis on manufacturing regulatory compliance brings us to a crucial point of discussion — the common misunderstandings many harbor about compliance. Many manufacturers perceive compliance as a static, one-time objective that, once achieved, requires no further attention. This notion, however, is a far cry from the reality.
Compliance isn’t a destination but a journey. It isn’t just about meeting the stringent regulatory requirements at a given point in time. Instead, it demands continuous adherence to these standards, despite changes in the regulatory landscape, market dynamics, internal operations, and technological advancements.
The Core Traceability Components within an MES Software Solution
Understanding the manufacturing execution system benefits, particularly the value of traceability components, can substantially alleviate risks. Let’s delve deeper into these features:
1. Real-time data capture and visibility.
Data is the backbone of traceability, providing the means to track, verify, and document the entire lifecycle of products or materials. The ability to easily capture and retrieve data in real-time and present it in an easy-to-understand manner is a significant advantage offered by modern MES solutions. Real-time data capture and visibility means you can swiftly spot and rectify issues, whether it's an equipment failure, a sudden spike in defect rates, or a drop in production efficiency. This immediate identification and resolution of issues often prove crucial in preventing expensive recalls.
2. Detailed audit trails.
In a highly regulated environment, having a detailed and accurate record of every operation and transaction is critical. Audit trails provided by MES solutions ensure that every movement of goods, every adjustment in parameters, and every quality check is recorded and easily retrievable. These digital 'paper trails' simplify the process of inspections and audits. They enable you to demonstrate your adherence to regulatory standards and quickly identify the root cause in the event of a recall. By highlighting exactly where a defect or non-compliance occurred, audit trails help in swift recall management, saving precious time and resources.
3. Supplier quality management.
The role of suppliers in a manufacturer's production process is undeniable. The quality of raw materials sourced from suppliers can significantly impact the final product's quality. Therefore, having robust inspection, data capture, and analytics is essential. The right MES solutions can enable you to closely monitor the quality and compliance of raw materials and your suppliers. This proactive approach helps minimize the risk of introducing defects or non-compliance issues into the production process, thereby mitigating recall risks.
Guarding Against Uncertainty
In a rapidly changing manufacturing landscape marked by stringent regulatory norms and high consumer expectations, recall risks present an ongoing challenge. By deploying advanced traceability measures, you can fortify your operations against potential setbacks.
As discussed above, it’s clear that the stakes are high in the highly regulated manufacturing sector. The potential risks emanating from product recalls are not merely financial but can significantly damage a company's reputation and customer trust. However, armed with robust traceability capabilities, in a modern MES platform, you can navigate this precarious path with increased confidence.
To learn more about improving operational efficiency in manufacturing, mitigating risk, and deploying advanced traceability measures, watch our free video, "FactoryLogix Solution Overview.”
The content & opinions in this article are the author’s and do not necessarily represent the views of ManufacturingTomorrow
Comments (0)
This post does not have any comments. Be the first to leave a comment below.
Featured Product
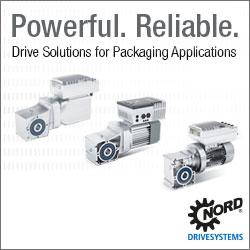