As directed by the facility’s warehouse management software (WMS), a fleet of 142 AMRs continuously delivers mobile shelves to associates at workstations equipped with light directed picking modules on both floors.
Sneaker and Sportswear Retailer’s New Mezzanine and Ground Floor Feature ResinDek Robotic Flooring
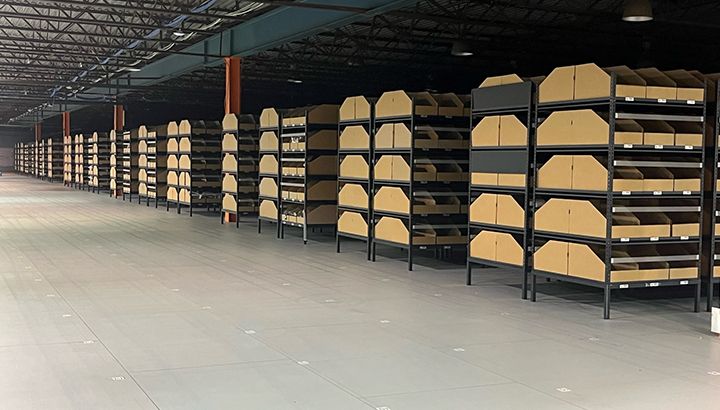
Case Study from | ResinDek
To support organic growth and expansion via acquisition, a global retailer of sneakers and streetwear sought to increase throughput and optimize order fulfillment efficiency in its existing Philadelphia distribution center (DC). The operation, which supports both e-commerce and retail replenishment, has employee shifts nearly around the clock to keep up with demand. It also cross-docks shipments, when possible, to minimize handling.
The retailer first engaged retail supply chain consultants Claris Solutions (claris-solutions.com) to define the optimal layout and technologies to meet their goals. Tony Chaplin, Claris Solutions’ Co-Founder and Managing Partner, led the project.
“First we determined that the existing building could sustain both their forecasted growth trajectory and their desired throughput,” he said. “To do that, however, we advised the installation of a 70,000-square-foot mezzanine above their existing 220,000-square-foot workspace, along with the implementation of a shelf-to-person autonomous mobile robot (AMR) system.”
Mezzanine Engineered to Maximize Usable Space
For the mezzanine, Claris brought in Legacy Platform (legacyplatform.com). Upon arriving at the facility, the first thing Legacy Vice President John Sloan noted was its age.
“The building is a historic brick structure that is several decades old,” he recalled. “That meant we first needed to verify that the existing concrete floor could support the weight of the mezzanine.”
After conducting core samples in several areas, Legacy determined that the existing floor could support a mezzanine constructed of steel — but not one made of concrete.
“Not only would concrete have been too heavy a load for the existing ground floor to support, but also the retailer wanted to continue to operate their distribution center throughout the construction of the structure,” Sloan noted. “To build a concrete mezzanine would have required them to shut down.”
Additionally, to attain maximum space beneath the mezzanine, the retailer asked Legacy to space the support columns as far apart as possible. When building a platform of this size, Legacy typically places columns 15 feet apart; in this case, the company’s engineers were able to create spans of nearly 30 feet by using larger beams to carry the load.
Existing Concrete Floor’s Condition Posed Problems for Robotic Navigation
At the same time, Chaplin and Sloan both noted issues with the concrete flooring’s surface. It was not entirely level in certain places, and there was wear and damage in others.
“A sloping, worn, and damaged concrete floor will prevent the AMRs from traveling smoothly and predictably along their workflow paths,” explained Chaplin. “Yet to grind it down to level it would be time consuming and extremely messy, particularly in an operation that needed to continue running throughout the project.”
Legacy recommended the installation of ResinDek® mobile robot flooring panels from Cornerstone Specialty Wood Products (resindek.com) for both the mezzanine surface and overlaid across the existing ground floor. To ensure the ResinDek installation on the ground floor was level, the concrete was surveyed first to identify areas where shims were added to compensate for the slope.
ResinDek Mobile Robot Flooring Installed on Both Levels
With the retailer running loads of more than 2,000 pounds, Dave Paquin recommended ResinDek MD for the mezzanine floor. On the ground floor, Paquin advised installing ResinDek HD, a 0.75-inch-thick panel capable of handling robot loads up to 4,000 pounds and pallet jack loads up to 4,500 pounds.
“AMRs rely on sensors to successfully and safely navigate through a facility. For that reason, all ResinDek robotic floor panels have a customized finish that meets the specific coefficient of friction, surface roughness, levelness, gloss, and wear requirements of the AMRs being deployed,” Paquin explained. “Every floor we design is custom manufactured to meet the specified load capacities and traffic volumes to ensure the operation attains the performance and throughput they expect.”
To further protect the robots’ sensitive on-board electronics from static electricity, Paquin also recommended the mobile robot flooring panels be coated with Cornerstone’s proprietary TriGard® ESD finish. This coating incorporates electrostatic dissipative (ESD) protection that complies with ANSI/ESD Association specifications to shield electronic equipment from damage. Additionally, TriGard ESD has been engineered to provide 3x greater resistance to wear than the standard ResinDek surface finish. This ensures that the panels will withstand the consistent, repeated travel patterns of high-frequency robotic traffic.
Finished Facility Meets Retailer’s Goals
By working closely with the retailer’s operations team to clear inventory from work areas daily, the mezzanine construction and flooring installations were completed in a highly aggressive 12 weeks. The facility is now home to more than 2,000 mobile storage racks across the two different levels with 50,000 product locations. Apparel and accessories are housed on the mezzanine; footwear on the ground floor.
Conveyor transports received cartons to designated induction stations on each level which direct putaway into empty shelf positions. As directed by the facility’s warehouse management software (WMS), a fleet of 142 AMRs continuously delivers mobile shelves to associates at workstations equipped with light directed picking modules on both floors. Conveyors also transport completed picks from the mezzanine down to the ground floor for order consolidation as needed.
“The retailer gained three main benefits from this project,” noted Chaplin. “First, by transitioning away from conventional picking to shelf-to-person, they’ve been able to increase their throughput without needing to increase their headcount. In a challenging labor market, that’s very important. Second, they’ve reduced their inventory turn time and enhanced their service levels because orders can be filled faster. And third, they’ve significantly improved their space and capacity to accommodate continued growth.”
# # #
ABOUT CORNERSTONE SPECIALTY WOOD PRODUCTS, LLC
For more than 20 years, Cornerstone Specialty Wood Products, LLC (www.resindek.com) has been in the forefront of research and development in the field of engineered wood floor panels for the material handling industry. Solutions include durable flooring that withstands the rigorous demands of heavy rolling pallet jacks, automatic guided vehicles (AGVs), and autonomous mobile robots (AMRs), as well as flexible shelving systems.
ABOUT LEGACY PLATFORM, LLC
Headquartered in Milwaukee, Wisconsin, Legacy Platform (www.legacyplatform.com) is an established delegated design and construction metals manufacturer covering a range of products from elevated platforms, catwalks/crossovers and miscellaneous metals serving variety of markets and customers. In addition to our project management and engineering offices in Milwaukee and Piqua, Ohio, we have the support of our 60,000-square-foot full-service fabrication facility in Amherst, Wisconsin.
ABOUT CLARIS SOLUTIONS
Claris Solutions (www.claris-solutions.com) offers management consulting, engineering services, and automation design, selection, and implementation to help retail operations achieve maximum return on investment (ROI). Focused on omni-channel store operations, distribution, and warehousing, Claris has helped retailers improve performance by increasing throughput and efficiency since 1998. The Claris team strives to exceed customer expectations by saving clients’ money and attaining faster results than larger firms while remaining independently focused on each project.
The content & opinions in this article are the author’s and do not necessarily represent the views of ManufacturingTomorrow
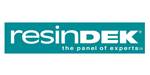
ResinDek / Cornerstone Specialty Wood Products
At Cornerstone Specialty Wood Products®, we know and understand the importance of having the right flooring product for the right application. That's why we offer a variety of ResinDek panels in different thicknesses, densities, and with different surface finishes. Since 1994, ResinDek flooring panels have been installed in distribution centers, warehouses, manufacturing plants, and cold storage facilities for major corporations worldwide. The intent of Cornerstone Specialty Wood Products then and now is "We don't just make better mezzanine floors…We make mezzanine floors better". We strive to provide solutions that improve the ergonomics in work environments, reduce environmental impacts, and bring significant value to the professionals in many different industries.
Other Articles
Key Flooring Considerations When Updating an Existing Industrial Mezzanine System
Warehouse Robots and Why Flooring is Important
Electrostatic Dissipative Flooring vs. Anti-Static Flooring: Which Flooring is Right for Your Facility?
More about ResinDek / Cornerstone Specialty Wood Products
Comments (0)
This post does not have any comments. Be the first to leave a comment below.
Featured Product
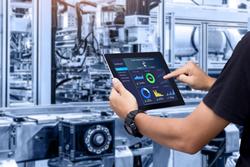