Limited floor space can hinder the implementation of new manufacturing technologies or the scaling up of production. Does this mean that manufacturers forced to operate within confined spaces should settle for suboptimal layouts
The pool of operational excellence - CubeBOX Pallet Pool integrated with robust software maximises floor space
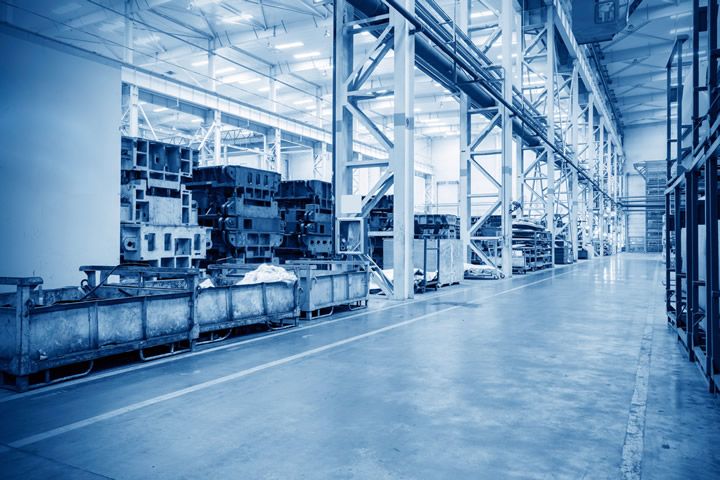
Serhat Volkan Yılmaz, General Manager | Tezmaksan Robot Technologies
Spatial constraints are a hurdle for many production facilities and, as a solution, PwC recommends that manufacturers modernise their manufacturing network design. Here, Serhat Volkan Yılmaz, General Manager of CNC automation system manufacturer, Tezmaksan Robot Technologies, delves into the transformative potential of lean principles, advanced software solutions like RoboCAM and innovative robot technologies such as Tezmaksan's CubeBOX Pallet Pool. With these tools, manufacturers can navigate spatial constraints and achieve operational excellence in today's competitive landscape.
Limited floor space can hinder the implementation of new manufacturing technologies or the scaling up of production. Does this mean that manufacturers forced to operate within confined spaces should settle for suboptimal layouts, inadequate utilisation of resources and subpar supply chains?
It used to, but not anymore according to PwC’s Designing the factory footprint for competitive advantage report: “Historically, companies rarely adjusted manufacturing footprints. The headaches associated with moving a plant greatly outweighed the operational benefits, and a high degree of vertical integration ensured that any change in plant sites could have a massive impact on the supply chain.”
Traditionally, these issues arose from a lack of necessary infrastructure and information-sharing capabilities, which made locating factories at a distance from sources of supply, end markets and customers costly. But such constraints are no longer an issue in the modern era of Big Data and Industry 4.0.
“Today’s business conditions — improved logistics, better computer systems and telecommunications infrastructure, less vertical integration, streamlined supply chains […] and competition that is stronger than ever before — have made it absolutely necessary to address network design issues,” explains PwC’s report.
But what is manufacturing network design? It refers to the strategic planning and arrangement of manufacturing facilities, distribution centers, suppliers and other elements within a supply chain network. Effective manufacturing network design optimises production, distribution and overall operational efficiency to overcome spatial constraints and achieve strategic goals.
Robotics and automation can perform a vital role, here, by helping to maximise limited floor space, improve resource utilisation, and scale up production efficiently. Likewise, real-time data analytics and predictive modelling can further enhance decision-making, mitigating risks and driving operational excellence in the face of spatial limitations.
Emphasise efficiency
Put simply, optimising floor space means accommodating as much value-adding potential as possible per unit of floor space. For example, a common metric in the retail trade is surface area productivity, which measures the turnover generated per square foot.
In manufacturing, various categories and metrics of lean production are customary. For example, carmaker Toyota is among the pioneers of lean manufacturing with its Toyota Production System (TPS), which embodies the Japanese principles of jidoka and Just-in-Time manufacturing to emphasise efficiency and minimise waste. Generally, the categories of lean production are value-adding, value-supporting and waste. In a machine shop, the workspaces of the machines are value-adding areas. Handling or staging areas are value-supporting, and areas for the storage of tools and fixtures belong to the same category. The remainder is waste.
However, if these classifications are extrapolated for a whole factory, then the result is that very little space is utilised for value-adding. As a solution, those units of floor space must be designed to give as much value-add as possible.
For this reason, Tezmaksan has developed the CubeBOX Pallet Pool, which can manage up to 24 pallets and 16 tools using a single unit. Pallets are arranged in a compact circle in front of the machine and a 6-axis robot handles the loading and unloading process — resulting in reduced operator intervention.
The compact, cube-shaped system is designed to maximise the utilisation of floor space. The system’s automated loading capabilities significantly reduce the need for manual intervention, thereby mitigating labour costs and ensuring consistent, efficient operation.
Because it is designed to integrate seamlessly with existing control units and robotics systems, the CubeBOX ensures easy implementation and interoperability with other manufacturing equipment — but how is this interoperability achieved?
Flexible manufacturing
Unlike the information-starved manufacturing networks of yesteryear referenced in PwC’s report, today’s digital and Industry 4.0 technologies are essential to modern manufacturing network design.
Advanced manufacturing software solutions play a crucial role in optimising manufacturing operations through real-time data analytics, predictive maintenance, and production scheduling capabilities. Manufacturing Execution Systems (MES) and Enterprise Resource Planning (ERP) systems enable manufacturers to monitor and control every aspect of the production process, from raw material procurement to finished goods distribution.
Furthermore, the adoption of Flexible Manufacturing Systems (FMS) allows companies to adapt swiftly to changing production demands, reducing setup times and enhancing overall operational efficiency. FMS integrates various manufacturing technologies, such as CNC machines, robotics and material handling systems, into a cohesive and agile production system. This integration enables manufacturers to respond quickly to changing market demands, minimise production downtime and optimise resource utilisation.
The CubeBOX Pallet Pool is integrated with Tezmaksan's advanced and customisable RoboCAM-FMS software, which is designed so that workpieces and tools for single or multiple CNC machines can be managed efficiently.
RoboCAM is based around a structured transaction process made up on ‘cells’ that include machine data, tool and workpiece information and operator definitions. The is concept similar to blockchain, where data units containing transactional records are chained together. Once the cells are defined, subsequent steps involve uploading and registering workpiece data, selecting raw materials, registering tools into the FMS library, determining operation sequences, and initiating controlled starts.
RoboCAM facilitates seamless communication between the software, robot, and CNC machines. The software's ability to handle communication via BUS or physical cabling offers flexibility in implementation, with necessary programmable logic controller (PLC) changes on the machine side. The software is also optionally compatible with barcode readers.
In essence, RoboCAM serves as the backbone of the CubeBOX Pallet Pool system. The software plays a crucial role in optimising workflow efficiency, ensuring that all required tools are available for each machining operation and facilitating automatic loading and unloading of workpieces.
Maximised floor space
Spatial constraints have long posed challenges for manufacturing facilities, limiting their potential for optimal layouts and resource utilisation. However, with advancements in digital technologies like Industry 4.0 and innovative solutions such as the CubeBOX Pallet Pool integrated with robust software like RoboCAM, manufacturers can effectively maximise floor space, streamline operations, and enhance productivity.
By embracing automation, flexible manufacturing systems, and real-time data analytics, companies can navigate spatial limitations, reduce labour costs, and achieve operational excellence in today's competitive landscape.
To discover what Tezmaksan’s CubeBOX CNC automation system can offer, visit the website or speak to a specialist today.
The content & opinions in this article are the author’s and do not necessarily represent the views of ManufacturingTomorrow
Comments (0)
This post does not have any comments. Be the first to leave a comment below.
Featured Product
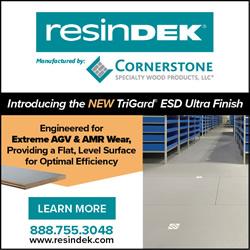