You could get the greatest benefits from additional automation if you first make sure your existing facilities support the highest productivity possible and the highest storage density feasible for your type of operation.
You Might Not Need Automation To Realize Greater Efficiency in Storage Operations
Article from | Steel King
Thinking of further automating your warehouse or distribution center? If so, you could get the greatest benefits from additional automation if you first make sure your existing facilities support the highest productivity possible and the highest storage density feasible for your type of operation.
“Automation can be the solution to many material handling issues,” says Ryan Wachsmuth, Southeast Regional Sales Manager for Steel King, a leading manufacturer of storage rack and material handling products. “But if efficiency is the goal, study your existing operations before automating or adding additional automation.
Automation has widespread benefits for management of a warehouse or distribution center, including better use of existing space, reduced labor needs and reduced risk of employee injury, better throughput, and better product integrity.
Multiple Factors Driving Automation
Labor availability, productivity demands and pressures to increase density in existing spaces – especially in cold storage facilities, are driving warehouse operators to consider greater use of automation. That could include an incremental approach where only certain functions are automated – giving you “islands” of automation, or going all the way to a “lights-out” facility that is so automated that few employees are needed and where the lights can literally be kept off.
A fully manual distribution center might have push-back racking that would accommodate its need for pallet positions, but such systems require more labor for the positioning and retrieval of pallet loads.
The transition from fully manual to use of some automation could include use of picking technology that indicates pick locations via some form of lighting. Another incremental option could be the installation of an automated deep lane pallet storage system. Those systems can utilize a shuttle that automatically places or retrieves a pallet load from the forklift’s access position.
Steel King is now partnering with Automha Americas regarding its Pallet Runner™ deep lane storage system. The lithium-ion powered Pallet Runner™ efficiently moves pallets in and out of high-density storage lanes.
Pallet Racking Changes Can Bring Benefits
Some of the same issues that drive people toward automation, including space, labor and picking accuracy can also be solved using various types of storage systems.
“Automation may not always be what you need to solve operating efficiency problems,” Wachsmuth noted, in a presentation at the recent MODEX expo in Atlanta. Once it’s recognized that efficiency could be improved, you need to identify your warehouse’s current operating data. From there, you can create a plan to either adjust your type of racking systems, or engage some level of automation.
“It’s like going to the doctor,” Wachsmuth told the MODEX attendees. “First you understand that something isn’t right with you, then you enlist an expert to help identify the source of the problem and develop a plan for improvement.” Your review of existing operations should include:
- Process documentation/Data analysis
- Facility and space factors
- Product and SKU mix
- Talent and personnel
- Integration with existing systems
- Safety considerations
- Budget factors and ROI
Automation Might Not Be the Solution – Yet
For a warehouse, you might determine that automation is not the best answer – at least not yet. Start out by looking at existing space, labor, throughput and product integrity. Is there opportunity for increased density by reducing aisle space? Does your facility have opportunities for storage above dock doors or by adding mezzanine levels for extra storage, equipment or offices?
If your plans include adoption of automation at a later date, including the use of robotics, remember that your racking design might need to meet certain tolerances to accommodate robotics.
With the use of AutoCAD, you can create an open canvas to virtually reposition equipment, current racking, etc., to identify opportunities for improvement. That might include a change in the type of pallet racking in your warehouse. Whatever system you now use, it might have opportunities to optimize efficiency. Things to consider in those systems could be:
Selective Racking – Narrow aisles; build in smart inventory slotting; add carton flow or dedicated picking aisles.
Portable Racking – Use storage containers or pallet racks – both of which are stackable – for extra storage when needed.
Drive-In Racking – This high-density system provides efficient storage but offers reduced selectivity. It’s a “last-in, first-out” system for items that will have longer life in storage, and don’t require immediate access. Drive-in systems are slower to access, but also less mechanically complicated than the next type of high-density storage: pallet flow.
Pallet Flow Racking – This system allows high storage density plus the advantages of the “first in, first out” handling for products that require inventory rotation. You can store as many pallets deep as you have the space for, on multiple levels.
Pushback Racking – When product perishability or rotation is not a factor, pushback racking allows for more flexibility and better selectivity than pallet flow or drive-in solutions. In a pushback rack system, forklifts place pallets on nested carts riding on inclined rails. Those pallets are pushed back by subsequent loading, exposing the next cart—a last-in, first-out storage strategy.
Mezzanines, Platforms Can Boost Efficiency
Productivity in a facility also can be boosted through use of work platforms and mezzanines. Mezzanines and platforms also affect space and time by using vertical space to add functional areas for storage, people and processes. Platforms and pick modules are naturally part of automated systems that reduce travel time, deliver goods to pickers, and integrate with many other types of automation.
“Mezzanines are a big part of many automated systems, because they can host conveyor lines, vertical conveyors, reciprocating lifts, spirals, and robots,” says Wachsmuth. “Pick modules — multilevel platforms with a variety of picking and put-away options — are where automation meets platform storage, racking and storage systems.”
There is no doubt that automation can bring benefits to warehouses. But before adopting automation, look at the existing operations and how your racking and other equipment is meeting your efficiency expectations. Don’t presume you have to fully automate; incremental steps or changes in racking might be all you need. If you decide on additional automation, make sure you have a good understanding of installation and implementation factors, as well as ramifications for upstream and downstream systems. Finally, make sure your planning includes education and training on the automation, with the understanding that staffing requirements and talent needs will likely change.
The content & opinions in this article are the author’s and do not necessarily represent the views of ManufacturingTomorrow
Comments (0)
This post does not have any comments. Be the first to leave a comment below.
Featured Product
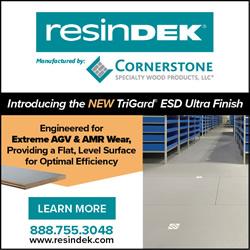