You might be aware that Industry 5.0 is aspirational for even the manufacturing who’s who and while the jury is still out on what exactly the goal of 5.0 is, many experts observe that Industry 4.0 is far from complete
From Simple Fixes to Advanced AI: A Small Manufacturer's Guide to Industry 4.0
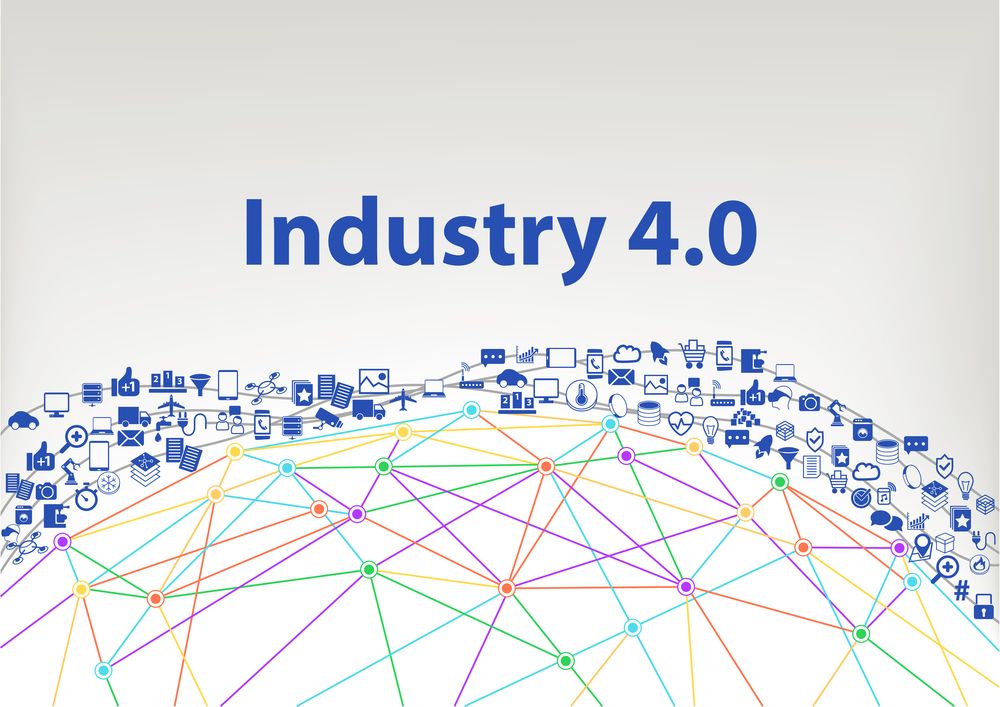
Rajesh Asher, Associate Vice-President of Business Development | Trigent Software Inc.
You might be aware that Industry 5.0 is aspirational for even the manufacturing who’s who and while the jury is still out on what exactly the goal of 5.0 is, many experts observe that Industry 4.0 is far from complete with even large enterprises yet to adopt intelligent technologies synonymous to 4.0.
But, as manufacturing consultants, we are more interested in how small-scale manufacturers perceive these developments. Are these terms (4.0 and 5.0) mere jargon to them? Do they look up to these technologies as aspirational or have they concluded that their organization is well off without these intelligent technologies?
Recently on the sidelines of an industry event, I heard a CEO jokingly point out that small manufacturers are ever caught in industry PI (i.e., 3.14159 – a casual dig implying that small-scale manufacturers endlessly circle and do not want to go beyond industry 3.0)
Maybe the small manufacturers are right. They are happy with siloed automation that unlocks incremental efficiencies. But are they right in assuming that any further digital transformation efforts would only create unnecessary complexities, affecting their day-to-day operations, without helping them realize significant business value?
This fear towards continued digital transformation might have primarily stemmed from:
- The implementation of standardized products that demand small manufacturers to completely alter their workflows.
- Erstwhile failures in integrating non-disparate systems. For e.g., one gets a product X for quality, y for manufacturing, z for operation, and then none of them work together.
- Short-term focus over long-term gains.
Whatever the fears might be, the opportunity cost of missing out on advanced technologies is significantly high, particularly for small-scale manufacturers. Hence, we propose a way to start with small-scale automation that gradually leads to seamless Data, AI, and Gen AI integrations typical of industry 4.0 and even 5.0.
Fig 1: Small Manufacturers’ Eight Steps to 4.0
(To assess complexity, the following variables were considered. a. Data complexity b. system integration c. customization requirements. To assess ROI, the following variables were considered a. Operational efficiency gains b. Revenue growth potential c. Cost reduction potential.)
Start with Simple Fixes on the Shop Floor (Low Impact, Low Complexity)
The overarching objective of these simple fixes is to address persistent inefficiencies commonly observed on shop floors.
Timesheet Automation
Automated time tracking eliminates the need for manual recording of employee hours. Even if you are using manual timekeeping systems such as punch cards, time clocks, or paper records - a simple RPA solution can automatically digitize and accurately record the information. You have the flexibility to retain your legacy system or adopt a cloud-based timekeeping system. Regardless of the choice, automating timekeeping gives you three immediate benefits:
- No manual errors while inputting the data
- Seamless integration with payroll systems
- Avenues for further analysis and workforce performance insights
Production Reports Automation
Imagine a system that automatically generates a daily production report at the end of every shift. Again, there is no need for manual entry as the data capture is entirely automatic. The best part? This automated data acquisition is even possible with older machines, either through appropriate sensors or it could be done through RPA implementations.
Quick Wins in the Supply Chain (High Impact, Low Complexity)
Now that you have tasted success on your shop floor, you might wish to extend your automated reporting capabilities onto your supply chain.
- Sales dashboards pull existing data from CRM, ERP, and sales databases to give your sales reps a snapshot of their existing performance and help them understand the areas that need attention.
Imagine a dashboard that automatically compiles and displays sales performance data by time ranges, by product or customer groupings, by units and monetary amounts, and by regions or territories. Through these dashboards, you automatically have the data on sales by day or week, sales that happened this year vs last year, Net Sales vs Returns, etc.
- Inventory optimization ensures you never have overstocking or understocking issues. Again, equipping yourself with a dashboard view that automatically populates current stock levels, suggestions for reorders, inventory turnover rate, forecast demands, and supper performance metrics.
Unlock Never-before Business Efficiencies (High Impact, Moderate Complexity)
Be it with simple fixes or quick wins we spoke about earlier, the objective was to create automated reports that address existing inefficiencies in your shop floor and supply chains. But now, you are introducing intelligent documents that unlock never-been-seen efficiencies for the business as a whole.
PO and Contracts Analyzer
The purpose of PO and contract analyzer is not just to accelerate contract review and approvals but to win favorable terms and ensure the obligations are met.
How does it work?
The AI tool analyzes your purchase orders and contracts, extracting key information such as payment terms, delivery schedules, pricing and legal obligations. In return, it flags potential risky terms and inconsistencies in contracts, suggesting alternative terms that reduce the risk or improve the manufacturer’s position. It even sets up automated alerts for contract milestones, ultimately ensuring that the contractual obligations are met.
EDI-ready Shipping Manifests
Imagine you don’t have to go through the hassles of manually collecting the data from multiple systems such as ERP and CRM, then create paper-based manifests, transport clumsy documents physically or through faxes, followed by manual compliance checks and final storage in files.
How about a system that automatically converts raw shipping data into standardized EDI formats, compliant with regulations and ready for secure transmission? The solution also provides audit logs and tracking information, ensuring transparency and traceability for every EDI transaction.
Simplify Business Workflows (High Impact, Moderate to High complexity)
Document Management System
Any manufacturing facility might benefit from a document management system because often, too much time is spent on searching, sorting, and managing the documents. Sometimes, you may have to click 4-5 folders to access important production data. Things further complicate when companies don’t have a formal system to document certain processes. For example, in part production typically seen in machine shops, employees tend to record in scraps of paper. You must note that this same part will be remade in six months, when most likely the paper bits may have flown away.
- The purpose of a custom document management system is to enable your employees to get instant access to important information.
- How about a quick text search to get to the relevant information without having to dig into multiple files and folders?
- You can also create custom workflows to automate the routing of your documents. For example, when a production report is generated, it is automatically sent to the production manager and operations manager for review.
Procure to Pay (P2P)
Procure to pay is a standardized process typically managed through ERP systems. But if you are not using an ERP, you can still implement a P2P system through a combination of standalone software, manual tracking tools, and basic workflow automation. Alternatively, you can realize an end-to-end procure-to-pay system through simple RPA implementations.
- Imagine an RPA bot reading key information in the purchase requisition mail and extracting relevant details such as item descriptions, quantities, and delivery dates.
- Then it logs into the procurement spreadsheet and automatically generates a purchase order using the extracted data. The PO is automatically routed to the relevant stakeholder for approval.
- The bot then monitors the email for order confirmation from the supplier. Once mail is received, it updates the order status in the procurement system and begins tracking order delivery.
- Once the order is received, the bots do the three-way invoice matching before triggering the payment.
ERP Customization
Now, you can buy a customized ERP or customize a standardized ERP. Both have their share of merits, but it is prudent to buy a standardized ERP and build a layer of customization - adding or deleting functionalities as desired.
We have extensively discussed when to customize, but customization can essentially be done to achieve following objectives:
- Create custom approvals (E.g., when you wish to add specific business rules for approval)
- Trigger specific notifications (E.g., when you need high-specific alerts or integrate with external communications tools)
- Automate an innovative process (E.g., when you wish to automate a proprietary quality control procedure)
- Simplify user interface (E.g., when you want your administrators, machinists, QA personnel to collaborate by posting notes, comments on the production process)
- Deeper integration with other systems (E,g, when ERP must be connected with bespoke or industry-specific tools).
Make Intelligent Shop Floors (High Impact, High Complexity)
Remember till now, you have only embraced simple automation on your shop floor. These automations weeded out certain existing inefficiencies. There is still a huge scope to become hyper- efficient and the right way is to create an intelligent production schedule.
AI-based Production Scheduler and Resource Manager
When a new customer order arrives, the AI analyzes order details including product specifications, quantities needed, and delivery deadlines.
It then scans your historical data relating to previous production times, material availability, and machine performance. It also factors in worker shifts, current workloads, and machine performance before delivering a production schedule that is aligned with customer deadlines and optimized resource usage.
Once the plan is generated, it is time to ensure that production runs as per schedule. The AI engages in adaptive resource allocation, considering real-time factors such as labor shortages, machine breakdown, and material lead times. It makes continuous adjustments in resource allocation so that the production schedule always remains on track.
Embrace Customer-centric Manufacturing (High Impact, High Complexity)
Armed with an intelligent shop floor and responsive supply chains, you now wish to include customers in the manufacturing process. Why not give them the flexibility to customize the product at the click of a button? Better, they can even previsualize what they desire.
- The Web/Mobile product configurator gives your customers an intuitive interface to make the customization process easy and enjoyable.
- The configurator typically allows them to customize the colors, materials, features, and specifications that suit their unique needs and tastes.
- The configurator is seamlessly integrated with your backend systems such as ERP, MES, triggering appropriate production flows and delivery.
Realize Next-gen Shop floors (High Impact, High complexity)
Next-gen shop floors are powered by IIOT digital infrastructure. Sensors deployed in machines transmit machine-related data in real-time, which are then captured, processed, and visualized for insights and subsequent decision-making.
AR-enabled Machine Diagnostics
The technician views the machine through the camera of the tablet or smartphone. The tablet screen shows the live video of the machine while the AR app overlays digital information relating to the machine.
The overlaid digital information can include interactive guides, diagnostic data, and highlighted problem areas that assist the technician to effectively diagnose the problem and accordingly repair the machine.
Preventive maintenance with IIOT
The preventive solution requires installing sensors in critical machines, setting up data networks, and integrating it with a predictive analytics system, all requiring significant investment and expertise.
The solution can be implemented in three phases.
- Anomaly detection – identify irregular and unexpected behaviors in machine data
- Diagnostics and prognostics – identify the root cause of anomalies and predict potential outcomes if not addressed
- Prescription and optimization – suggest prescriptive actions and maintenance schedules to prevent future failures
Simplifying Supply Chain Workflows (Moderate Impact, High Complexity)
You can customize your logistics and warehouse management workflows to achieve the following objectives:
- Dynamic route optimization based on real-time conditions
- Real-time inventory tracking, giving continuous visibility into stock levels
- Integration with specialized systems to support complex scenarios like multi-location shipping or reverse logistics
In conclusion, all the above solutions majorly pertain to Industry 4.0, because they enable you to achieve both horizontal integration (across value and supply chains) and vertical integration (empowering front-line to top-floor management staff). They provide your organization the digital maturity characteristic of 4.0 and beyond, setting the stage for future advancements.
"By embracing these technologies, small manufacturing solutions can not only help companies stay competitive but also unlock new opportunities for growth and innovation. It's time to take the next step and realize the full potential of your manufacturing operations."
Rajesh Asher works as the Associate Vice-President of Business Development at Trigent Software Inc. An experienced Sales Leader with a demonstrated history of successful client and team management, he has over 25+ years of experience in dealing with Application Development and Quality Engineering services.
The content & opinions in this article are the author’s and do not necessarily represent the views of ManufacturingTomorrow
Comments (0)
This post does not have any comments. Be the first to leave a comment below.
Featured Product
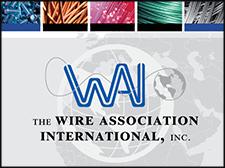