Future-proofing warehouse operations will require smart connectivity and specifically scalable, fluid network capacity and a new way of thinking about the invisible network that keeps the robots rolling in the warehouse of tomorrow.
Shaping the Future-Proof Warehouse through Smart Connectivity

Tamer Kadous, Vice President of Terrestrial Network, | Globalstar
Warehouse construction and automation spiked during the COVID-19 pandemic to meet the needs of online shopping. When the pandemic ebbed, so did warehousing and the automation that boosted its efficiency. Demand for warehouse automation began to recover in late 2023, however, and is forecast to accelerate in 2024 and 2025 to reach $44 billion by 2028.
That’s the good news. The bad news is that, as process automation becomes the top priority, the infrastructure demands on the warehouse are changing. The traditional warehouse is full of fixed infrastructure: conveyors, carousels and vertical lift systems, scanners and sensors, and the wired connectivity that integrates it all with data and process management systems.
With the return of growth, companies are now looking for ways to future-proof their facilities, seeking the flexibility to scale capacity up or down as needed. Key to this are autonomous mobile robots (AMRs). They are projected to dominate warehouse automation spending in the next half-decade, which will double to $18 billion by 2029. Amazon alone has grown its fleet of AMRs from 30,000 in 2015 to 750,000 today.
Goals for future-proofing the automated warehouse
In the future-proof, automated warehouse, robots receive and store goods, pick them in response to orders and deliver them to human workers for packing and shipping. Compared with fixed infrastructure, they offer –
- More compact and efficient warehouses. The active zone of a warehouse can shrink to dense stacks of storage bins connected by horizontal tracks and automated vertical lifts. Small, low-profile robots navigate the maze with ease and return to a service area for recharging, where multiple robots are typically clustered.
- Greater personnel safety. Workers engage with the robots at workstations on the outer edge of the active zone, whether packing goods or handing off incoming supplies to robots. The activities with the greatest potential risk take place inside the stacks.
- Faster adaptation. “Ripping and replacing” fixed infrastructure to grow capacity is costly and time-consuming. When robots are the primary moving parts in a warehouse, however, changes can be quickly developed in software and, when stable, implemented immediately. This “fluid capacity” offers a significant competitive advantage.
Connectivity options
You are probably familiar with the wireless network options available in the warehouse environment. Wi-Fi is the original option, operating in unlicensed bandwidth. The more recent contender is private cellular using Citizens Broadband Radio Service (CBRS).
Wi-Fi dominates in private wireless with some 600 million devices sold, because it is free to use, and the technology is low-cost and easy to install. Many applications benefit from Wi-Fi, but the sheer number of Wi-Fi networks offers much opportunity for interference between them to affect performance. In wide areas where multiple Wi-Fi access points (APs) are needed, the network requires a roaming capability for coverage – something that Wi-Fi is not good at. Security is another concern, because the popularity of Wi-Fi has attracted hackers and given them years of experience in penetrating its security. For all these reasons, Wi-Fi is not the ideal technology for mission-critical automation.
That’s why CBRS 4G/5G networks are growing in popularity. Using cellular standards, they are more secure and face less interference than Wi-Fi. Like Wi-Fi, they are free to use, though every network must register with the Spectrum Access System, an online database, because licensed CBRS users in the area have priority. In other words, availability of the frequency is not guaranteed. Even when it is available, the SAS system can disrupt some applications if the wireless link is interrupted to change frequency.
Both Wi-Fi and CBRS options face challenges in a dense automated warehouse full of radio-absorbing metal structures. Keeping a robotic workforce functioning there requires extensive advance planning of coverage, capacity and interference. That planning needs to be repeated whenever infrastructure changes.
Is there a better way?
When those were the only options on the table, warehouse developers naturally worked with what they had. But the time is long past for a fundamental rethink of cellular private network design.
The strength of standard cellular design – an array of overlapping cells of radio frequency – is also its greatest weakness when it comes to private wireless networks in a congested environment. The weakness is that each cell works alone to avoid disruption of service. The boundaries between these cells in dense deployments create interference at the edges and require tricky handovers. It is common to see a user equipment (UEs) ping-pong among a few cells or handovers fail to complete. When many robots congregate within one cell – for instance, while they are recharging – it responds by dividing its available bandwidth among them. Both throughput and latency rapidly degrade. Meanwhile, the next cell over may have ample bandwidth available but is out of reach.
What would an ideal network design look like for the future-proof warehouse? Forget separate cells – it would consist of a single “supercell” without boundaries, in which all radios transmit to all UEs at the same time and somehow do it without interfering with each other. The total lack of interference would automatically give throughput a major boost. Because each UE would have the potential to access the total bandwidth of the network, instead of just one of its cells, there could be no congestion in a single cell. And, of course, the same ideal network would not require all-new technology everywhere. Instead, it would work with radio units already available in the market and interface seamlessly with existing UEs.
That’s easy to say and hard to accomplish. However, an answer is emerging: a software-based system running on generic compute that provides the sophisticated synchronization and calibration that a supercell requires. It includes compatibility with key standards from the Open Radio Access Network (ORAN) and the Third Generation Partnership Project (3GPP). And it is already in use in one of the most robot-intensive, automated warehouses in the world, operated by one of the world’s leading retailers.
Future-proofing warehouse operations will require smart connectivity and specifically scalable, fluid network capacity and a new way of thinking about the invisible network that keeps the robots rolling in the warehouse of tomorrow.
Tamer Kadous is VP of Terrestrial Networks at Globalstar, responsible for building and commercializing 5G technologies for KPI-demanding applications with a focus on factory automation and Xtended Reality (XR). Tamer joined Globalstar through the acquisition of XCOM-labs 5G technology. Under Tamer’s leadership, two XCOM-labs commercial systems have been built for licensed and unlicensed spectrum wireless technologies. Before XCOM, Tamer worked in Qualcomm Research, designing and implementing wireless communication systems.
The content & opinions in this article are the author’s and do not necessarily represent the views of ManufacturingTomorrow
Comments (0)
This post does not have any comments. Be the first to leave a comment below.
Featured Product
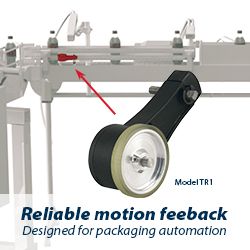