The Industrial Metaverse is emerging as a transformative technology in manufacturing and maintenance, blending advanced technologies to create a more efficient and responsive operational landscape.
Industrial Metaverse: Pioneering Remote Maintenance Solutions
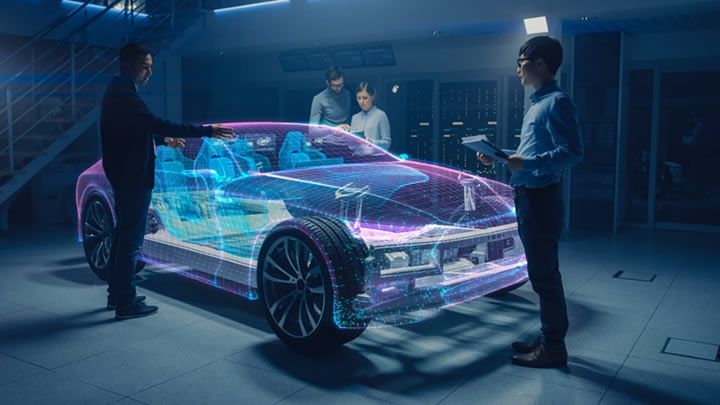
M. Sc. Kutay Can Yinanc & Dr. Maiara Rosa Cencic | Digital engineering - Fraunhofer IPK
The Industrial Metaverse is emerging as a transformative technology in manufacturing and maintenance, blending advanced technologies to create a more efficient and responsive operational landscape. The integration of technologies such as 5G, edge computing, and cloud solutions empower businesses to reimagine traditional production and maintenance processes. This evolution is particularly evident in remote maintenance, which offers significant enhancements over conventional methods and is essential in service-oriented solutions. By leveraging these innovations, organizations can improve operational efficiency, reduce downtime, and maintain a competitive advantage in a fast-paced market.
What is Remote Maintenance?
Over the past few decades, many companies have turned to servitization in two different key ways: by offering additional services that enhance the lifecycle of their traditional products, or by adopting product-as-a-service business models, where they retain ownership of the product while providing customers with pay-per-use or pay-per-time services.
In the first option, maintenance services are the most frequently offered services to enhance the product lifecycle – such as when buying a car and doing its maintenance at the brand’s authorized maintenance network. On the second option – such as on Machine-as-a-service cases, where industrial machinery is offered as a B2B service, while ownership is kept by the machine tool provider - maintenance services are crucial to ensure customer satisfaction and the financial feasibility of the business model. In this case, prolonged product downtime can lead to substantial financial losses for the equipment provider, making timely maintenance critical.
Remote maintenance enables technicians to monitor and service a device, system or machine away from its location. With remote maintenance technologies, organizations can track systems in real-time, analyze data, and predict potential failures, thereby reducing unplanned downtime. To enable remote capabilities, technologies such as cloud computing and Internet of Things (IoT) devices play an essential role. Additionally, extended reality technologies (AR/VR/MR) play a meaningful role in remote visualization of the devices. By combining and integrating those technologies, the industrial metaverse can be key to transforming remote maintenance processes.
Understanding the Concept of the Industrial Metaverse
When we hear the term “metaverse”, our minds drift to typical end-consumer-centric experiences, like gaming, shopping, or tourism. Moreover, in the industrial context, the term “metaverse” is often associated with an immersive environment where bosses, employees or customers colleagues can perform virtual meetings. However, this is not what we only mean by “Industrial Metaverse”.
The Industrial Metaverse (IM) is a vast platform of connected virtual replicas (more specifically, digital twins) of machines, factories and even the company processes, aiming at merging the physical and digital elements in the whole product life cycle. The industrial metaverse enables man-machine natural interaction (i.e., real-virtual interaction), simulation of machine behaviors, and the simulation of entire industrial processes.
Another misconception is to only associate metaverse with extended reality technologies. In fact, alongside AR/VR, cutting edge technologies such as IoT, artificial intelligence, edge computing, data streaming, communication networks and blockchain technologies are also building blocks of this concept. Those building blocks are essential to solve many industrial challenges, such as those faced by Remote Maintenance processes.
Solving Remote Maintenance Challenges in the Digital Realm
One of the primary challenges in maintenance services is the logistical difficulty of getting specialists on-site during breakdowns. Traditional communication methods, such as phone calls, often fall short in addressing complex issues and are prone to potential errors in repairs. The Industrial Metaverse addresses this challenge by creating a collaborative digital space where experts can monitor, diagnose and solve problems alongside field technicians, no matter their physical location.
For instance, consider a German provider of machines-as-a-service operating under a pay-per-use business model. A Brazilian manufacturing company is their client and utilizes these machines in their production line. If an issue arises in Brazil, the German team can perform inspections and support with remote maintenance though an Industrial Metaverse infrastructure. They gather operational data through IoT devices to identify anomalies via digital twins. XR technologies enable visual inspections and interactions with digital assets, allowing on-site personnel to execute real-time maintenance actions. This seamless integration between physical and virtual environments not only preserves equipment but also promotes a sustainable operational model, with AI-driven analytics informing future maintenance strategies based on both historical and real-time data.
Thanks to this digital industrial space, expert teams and onsite technicians can collaborate like never before, pushing the boundaries of what is possible. By visualizing digital twins, technicians can access critical information swiftly, leading to faster problem resolution. AR/VR technologies simplify complex tasks, reducing the need for specialists to travel, thereby minimizing costs, machine downtime and carbon footprint.
In addition, technicians benefit from immersive training experiences in simulated environments, boosting their skills and confidence regarding the maintenance procedures before applying them in real-world scenarios.
Using Distributed Ledger Technology (DLT) in an industrial metaverse environment enhances the security of product and process information by providing a decentralized and immutable record of transactions and data exchanges. Production information, which is difficult to protect with traditional methods, can be digitized with NFTs in the virtual metaverse environment, making it easier to store and share. While this information is visualized with XR technologies, automatic payments are made to the owners who use digital assets. Each piece of information is stored across multiple nodes, making it nearly impossible to alter or delete without consensus from the network. This transparency ensures that all stakeholders have access to the same verified data, reducing the risk of tampering and fraud.
Hidden Challenges of Metaverse Maintenance and Future Direction
While this scalable and sustainable technology presents numerous advantages, several challenges exist. Developing an industrial metaverse requires accurately modeling the virtual space and ensuring its applicability. The key factor is that this digital space may encompass the production environment, all devices and people in the loop. Developing such an environment involves creating a large-scale 3D scene dataset with diverse data formats, making the process labor-intensive.
Another main challenge is to maintain real-time synchronization between physical machines and their digital twins. Asynchronization of changes in the current system can lead to inconsistencies during maintenance tasks. For this reason, the industrial metaverse should be integrated with the existing systems following an adequate strategy that considers data continuity, rate of data update and data quality.
Infrastructural limitations can also negatively impact remote maintenance performance. During remote operations, network latency should be avoided to ensure a stable connection. High-speed connection technologies (like 5G or WiFi6) are essential to avoid network latency during remote operations. On the other hand, the lack of hardware capabilities may limit the processing of the models used in the industrial metaverse. The hardware, such as XR devices, sensory clothing, holographic projectors, brain-computer interface (BCI) devices, or smart display terminals, must be chosen correctly to avoid degrading the quality and detail of the representation of the digital twins. Additionally, reliance on cloud services for processing sensitive data raises concerns about data security and confidentiality, necessitating careful IT infrastructure setup to protect intellectual property.
For properly dealing with those challenges, the advances within the IT infrastructure of companies need to be massive. Therefore, the future of the metaverse in the industrial sector promises significant shifts in smart manufacturing. Innovative federated data infrastructures will become more prevalent, alongside industrial AI and blockchain technologies. Advanced solutions such as B5G, 6G, and quantum communications will enhance big data exchange and real-time interactions. Upgraded hardware and improved XR applications will provide users with more interactive and immersive experiences. Meanwhile, this entire technological landscape must ensure energy efficiency and sustainability.
We know that all those challenges and required technological advances are unrealistic and incompatible with the reality of many companies, where basic issues like lack of data continuity and a lack of integration in the IT landscape are still part of daily routine. However, the last paragraphs have described the ideal scenario – which is not a reality in any company and does not have to exist in order to implement the industrial metaverse. Actually, we recommend the other way around. Implementing the industrial metaverse can start small, with a specific use case that can add value the most and require small technological updates. Starting small-scale implementations, proofing the concept in specific use cases and overcoming challenges locally for these implementations can be an initial step towards evolving the data and network infrastructure and enhancing data continuity and integration.
Conclusion
The industrial metaverse shows great potential as an innovative approach to revolutionize maintenance and repair processes for enterprises. With the combination of cutting-edge technologies, tight bridges are being built between the physical and digital worlds, providing huge advantages in production and maintenance services. Remote maintenance techniques on a digital platform allow faults to be detected and resolved quickly, while at the same time reducing costs for businesses and increasing operational efficiency. There is no denying that there are challenges to overcome in order to ensure the long-term success. However, even though the necessary infrastructure for digital twins needs to be carefully considered, this evolution can start small and evolve slowly according to the company’s needs. The trends indicate that the IM will evolve towards more integrated, efficient and user-friendly systems, significantly improving both remote maintenance and smart manufacturing capabilities. In this context, it is critical for companies to be part of this revolution and adopt innovative solutions to maintain their competitive advantage.
M. Sc. Kutay Can Yinanc, Research Associate Extented Reality
Fraunhofer Institute for Production Systems and Design Technology IPK
Dr. Maiara Rosa Cencic, Leader of Department Extented Reality
Fraunhofer Institute for Production Systems and Design Technology IPK
The content & opinions in this article are the author’s and do not necessarily represent the views of ManufacturingTomorrow
Comments (0)
This post does not have any comments. Be the first to leave a comment below.
Featured Product
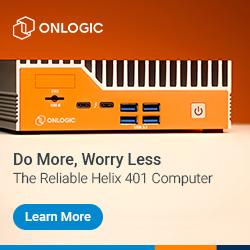