Embracing the idea of a consistent source of information, in context, for all stakeholders, often referred to as a “digital thread,” can significantly streamline processes, enhance collaboration, and drive efficiency.
Modernizing Capital-Intensive Industries with a Digital Thread
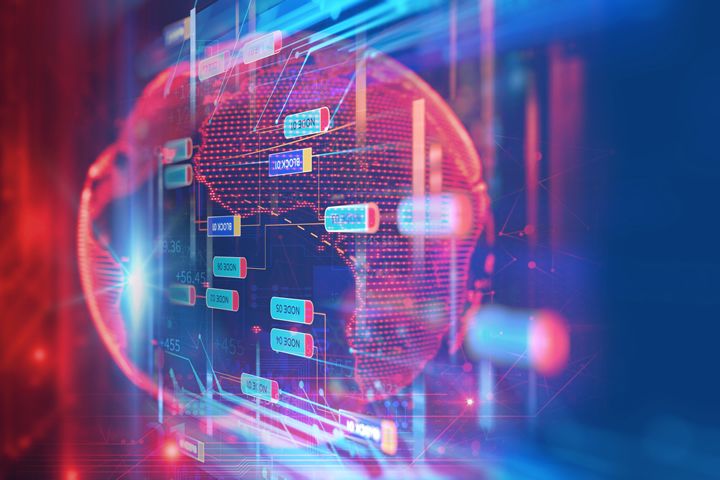
Jason Kasper, Director of Product Marketing | Aras
Capital-intensive industries such as oil and gas, power generation, and shipbuilding face unique challenges during the engineering, procurement, construction and handover phases due to their sheer scale and complexity. These projects often cost billions of dollars and require extensive collaboration across numerous teams, as they encompass intricate systems and have product design and usage life cycles spanning decades.
Managing change, configuration, and documentation, ensuring consistent collaboration between vendors and suppliers, and maintaining data accuracy are critical to the success of these projects. Embracing the idea of a consistent source of information, in context, for all stakeholders, often referred to as a “digital thread,” can significantly streamline processes, enhance collaboration, and drive efficiency from design all the way through the manufacturing process to the ongoing operations phase.
The Challenges of Complex Projects
As one can imagine, capital-intensive development projects are far more involved than any other digital engineering or product design project. The sheer size of the end product and the time it takes to design and build it means an army of designers, partners, and suppliers are involved - and it also means a mountain of information is created in the process. This information is not trivial documentation either - it often needs to be referred back to if there needs to be a change, or an adjustment in the project, or to meeting compliance demands of evolving regulations. If there is a problem, the documentation needs to be at the manager’s fingertips.
You can only imagine just how massive and unwieldy a process this is to manage when using traditional paper-based processes. It’s not uncommon to find hundreds of document binders passed to a manager when a project is completed and transferred. The fact of the matter is, not only is this beyond inefficient, but it also perpetuates the siloing of data and locking away of critical information within certain departments and systems, making it a Herculean task to fully comprehend all of the data in a way that leads to proper decision making.
Bad data affects not only the manufacturing phase, but also the operational phase of a project. Poor data quality can hinder operations, maintenance, and decommissioning, leading to increased costs and reduced performance over time. It goes without saying that paper documentation or disconnected electronic information and isolated data are no longer effective in today's fast-paced design and manufacturing environment.
Why Capital-Intensive Projects Need a Digital Thread
A digital thread connects data from design, build, construct, operate and maintain phases, across the product lifecycle, making it interoperable, reusable, and traceable. This approach allows for centralized data management, providing an authoritative version of the truth that all stakeholders can rely on. By moving from a document-oriented to a data-oriented approach, companies can ensure that valuable information created during each phase of the project is not lost or siloed, never to be seen again. Naturally, better data management and a single source of the truth means it’s easier to locate the data you need, as you need it, which in turn enables better decision-making and improves overall operational efficiency.
As a digital thread builds a comprehensive, data-centric picture of the entire design and manufacturing lifecycle, it also sheds light on any gaps in compliance data, enabling teams to understand and address said gaps before it’s too late. Establishment of a digital thread is particularly beneficial for maintenance as well, as it helps organizations keep better records of when work was done and makes it quick to locate updated procedures and solutions. Accurate maintenance records make it possible for the work done on one project to inform and be applicable to future projects as well, without the need to flip through dozens of binders.
Digital Thread Challenges
While implementing a digital thread approach in capital-intensive industry projects can be rewarding, there are also challenges that need to be recognized and addressed along the way. As expected, the larger the project, the bigger the scale and complexity of the variables and assets involved. These not only include data, but also stakeholders - the vendors and partners, for example, who need access to the same systems and information as everyone else.
The two biggest challenges that need to be actively addressed in order to establish an accurate and effective digital thread are data context and data extraction.
- Data Context - Finding a way to keep data and its context together in an organized way is crucial. Just data alone doesn’t tell end users what they need to know to properly impact decision making. Data needs context and detail alongside it in order to understand it fully. A digital twin can help by providing the complete story of every asset (and of the facility itself) and managing the changing configuration by indicating any changes that were made along the way.
A great example of the importance of context comes from when something breaks down, say on an assembly line. Is it the part itself, the way it’s being repaired, or a larger problem earlier in the process that is causing the piece to break? The data shows a breakdown, but without the context that looks at why there is a breakdown, there may never be an answer to the larger issue at hand.
- Data Extraction - Traditionally, pulling insights from legacy documents is a manual and time-consuming task, often leading to delays or skipped steps. Not only are traditional paper-based sources unstructured and random, but often the work needs to be repeated over and over again whenever there is an issue. The implementation of a digital thread approach creates the single version of the truth necessary for fast, accurate information to be shared. But the question is - how can you pull useful information from data that hasn’t historically been inputted into a digital system? As companies centralize and connect their data in a digital thread, how can you make sure historical data is extracted and used to help identify trends and inform decisions?
In the past, this may have been the unpleasant job of an intern - inputting the mountains of data into the digital system. But with the advent of AI-powered tools, product design and manufacturing data - current and historical - can be extracted using AI, ensuring that all information is accessible and actionable. AI can pull information and insights from unstructured sources and legacy data, while also automating the process of ensuring that new information is updated and available to all stakeholders.
Tying Together Capital-Intensive Projects
Today’s capital-intensive projects need to fully move away from traditional paper and manual models of documentation once and for all. By embracing a digital thread approach, organizations can finally make data management a less expensive and complex process, while empowering their teams to make better informed, more accurate decisions in the long-term, improving efficiency and effectiveness.
Jason Kasper joined Aras in 2017 and is the Director of Product Marketing, primarily focusing on supporting Digital Transformation, Digital Thread, and Digital Twin go-to-market programs. Jason has over twenty years of experience working with customers to develop enterprise software solutions for industries including discrete manufacturing, oil and gas, mining and metals, utilities, and transportation. Before joining Aras, Jason was an analyst at LNS Research, specializing in Asset Performance Management, the Internet of Things (IoT), and the Digital Twin. Prior to this, Jason held senior positions at Meridium (GE Digital), IBM, ABB, and Aspen Technology, focused on the development of industry solutions for asset-intensive organizations in the Enterprise Asset Management and Asset Performance Management markets. Jason holds a BS in Management from California State University, Chico, and an MBA from the D’Amore-McKim School of Business at Northeastern University.
The content & opinions in this article are the author’s and do not necessarily represent the views of ManufacturingTomorrow
Comments (0)
This post does not have any comments. Be the first to leave a comment below.
Featured Product
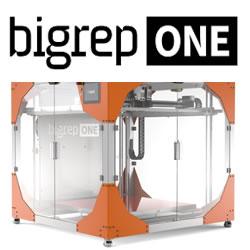