In this playbook, we’ll explore how manufacturers can use RIA to improve their operations and bottom line, and why the performance improvement partner you select to implement this process matters in ways that may surprise you.
Supercharge Manufacturing Performance with Rapid Improvement Approach

Article from | Milliken
Suppose there was a roadmap to solving your biggest operational challenge. Better yet, let’s say it’s a step-by-step process that lets your team improve quality, safety and performance — all while hitting your profitability goals.
Welcome to Rapid Improvement Approach (RIA), a highly evolved manufacturing improvement system designed to quickly and efficiently address frontline performance issues. No line shutdowns. No frontline staff disruptions. RIA lets you keep your foot on the gas as you swiftly resolve a significant process issue. It’s a strategy with a proven track record across nearly all manufacturing sectors, including paper and packaging, food and beverage, chemical, consumer packaged goods, medical device, construction and metals.
What kind of numbers are we talking about? A typical result delivered through RIA yields a 30% increase in productivity, a 50% improvement in safety engagement and ROI that is three to five times the initial investment. Within four months, many organizations can expect to see a five- to 10-point surge in their OEE (overall equipment effectiveness) rating when using RIA.
In this playbook, we’ll explore how manufacturers can use RIA to improve their operations and bottom line, and why the performance improvement partner you select to implement this process matters in ways that may surprise you.
A Need for Speed
The global need for RIA intensified in March 2020, as the pandemic changed everything for a large swath of global manufacturing. In days, supply chains that may have taken years to negotiate and nurture were upended. Manufacturing output fell at a 43% annual rate and hours worked fell at a 38% rate in Q2 2020 — the largest declines since World War II. No major industry was spared.
Lean manufacturing took on a whole new meaning as material and labor dwindled. The discipline of long-term continuous improvement took a back seat to expediency, as manufacturers raced to meet unchanged or even accelerated customer demand.
The aftershocks of 2020 and 2021 are still felt today. The need to streamline or critically rethink manufacturing processes hasn’t gone away. In many ways, it’s more imperative than ever as manufacturers face persistent needs, such as:
- Customer demand (both quantity and quality).
- Employee turnover and evolving skill sets.
- Frontline supervisor development.
- Machine performance.
“Many manufacturers don’t have the luxury of focusing on long-term performance improvement goals. They need improvement now. They have orders to fill,” explains Phil McIntyre, VP, and managing director of Performance Solutions by Milliken (PSbyM), a well-established global performance improvement consultancy specializing in RIA engagements. PSbyM serves over 400 operations in more than 45 countries.
Major Capex Savings
There are many reasons a manufacturing company would consider RIA. For instance, the company may want to:
- Fix a dire operational issue that negatively impacts product throughput, quality, waste, staff morale, maintenance, uptime or other concerns.
- Supercharge frontline associates with the mindset, skills and equipment to go from good to great with speed and resolve.
- Engage a third party because they may not have the process engineering bandwidth or expertise to work through a performance improvement issue internally.
In each case, RIA is a catalyst for rapid change. Chris Caldwell, a U.S.-based senior client lead for PSbyM, illustrates a typical scenario:
“An assessment is scoped and shaped based on the company’s need. For example, they might say we need more throughput or else we lose a major customer. The questions are, ‘Do we open another line and budget millions of dollars for frontline staffing, training and equipment?’ Or ‘Can we squeeze another five or 10 points of operational efficiency out of our present line and save millions of dollars?’”
180% Improvement
“It comes down to identifying the losses, the constraints and the pain points,” Caldwell, a former plant manager, says. “It’s our job to use sound performance improvement practices to reduce variability. Variation is not your friend. And that means driving out variability in the machine, operator and process.”
The practical effects of RIA can be surprising and gratifying. Caldwell cites a recent RIA engagement that demonstrates the outcome through aggressive diagnosis and treatment. “The client wanted to gain 10 OEE points in a constrained area within four months,” Caldwell reports. “That was our starting point.”
After an assessment identified the losses, Caldwell’s team scaled the RIA down to a single production line, which was easier to measure. “The line selected wasn’t the worst or the best,” Caldwell says. “The aim was to establish a system we could confidently implement across all lines. The goal was 10 points within four months. We delivered 18 points of efficiency improvement on schedule.”
No Surprises
The keys to a successful RIA implementation are clear expectations and the rigor to meet them. Caldwell’s U.K.-based colleague, PSbyM senior client lead Darren O’Connor, puts it plainly: “We sit down with plant leadership and frontline staff to explain our process and what success looks like.”
The absence of surprises is crucial to success with RIA, notes O’Connor, a Six Sigma Black Belt holder and veteran manufacturing leader. “There’s no ambiguity. No uncertainty. Never a surprise. The goal is to over-communicate, if anything.”
To avoid ambiguity and uncertainty, a dashboard presenting the mutually agreed upon key performance indicators (KPIs) in the statement of work is installed and presented within the first week. It’s a level of transparency and visibility that reinforces RIA goals and delivery to date weekly.
“It shows the tactical items we must accomplish,” Caldwell says. “Every team has a specific set of tasks that they must do. Did we get those things done or not? The dashboard either signals red or green. If something isn’t accomplished, it’s noted what needs to happen to achieve the deliverable. It’s highly disciplined. There’s no scope creep.”
What is Scope Creep?
While working through RIA goals, manufacturing management may be tempted to expand the scope, especially as the pace of results escalates. It’s a temptation PSbyM practitioners resist. “A good statement of work at the beginning is very helpful,” Chris Caldwell observes. “It keeps us between the ditches.”
McIntyre adds, “It’s very easy to be looking at another piece of equipment and see an unrelated opportunity. If you start chasing everything, nothing gets done. We stay focused on the job at hand.”
11:1 Return on Investment
McIntyre offers another lesson in RIA dynamics by describing a 12-week assignment for a multibillion-dollar consumer foods manufacturer. The company’s senior leadership believed aggressive improvements at four underperforming plants could generate cost savings of $3 million annually through less overpacking and changeover times, improved equipment effectiveness and quality throughput. What could RIA achieve in a single quarter?
The four-plant engagement yielded investment returns from 3:1 to 11:1 across the plants. Other results include:
-28% overpack waste
-19% changeover times
-31% minor machine stops
+17% off-quality
The strong results across the four pilot plants encouraged the company to expand the RIA to plants in Europe and China.
Qualities to Consider
There are factors to consider when assessing a potential RIA advisor, including third-party references, years of experience, portfolio diversity and other characteristics.
McIntyre suggests manufacturers should also include less common qualifiers, such as how much hands-on plant management experience the advisor — called Practitioners by PSbyM — brings to the engagement?
“Call it dirt under the nails. I’d want to know how long the practitioner has paid his or her dues on the shop floor,” the 35+-year manufacturing, supply chain and business leadership veteran describes. “Do they know from personal experience the special challenges line supervisors, shift managers and frontline associates face every day?”
McIntyre also recommends three additional considerations that manufacturing leaders should weigh while deciding on partners:
1. Proof of Concept. “We open the doors of a Milliken plant to any company that considers working with us,” McIntyre says. Milliken operates over 40 manufacturing facilities in the U.S., U.K., Belgium, France, Germany, Mexico and China. Industry observers often point to Milliken’s manufacturing process as among the world’s finest examples of operational excellence, synthesizing the best elements of Kaizen, 5S, JIT/Kanban, TPM, Six Sigma and 3P into a distinctive, holistic manufacturing philosophy. “Touring our sites ensures our beliefs align with the client’s when it comes to manufacturing excellence.”
2. Zero-Loss Thinking. McIntyre says practitioners should come to every engagement with a zero-loss mindset, meaning there is no acceptable level of failure, from breakdowns and delays to poor quality and manufacturing waste.
“Loss analysis is a discipline that’s proven and ultimately serves the client’s best aims, no matter the industry or performance requirement,” McIntyre says.
3. Frontline Engagement. It’s important to win buy-in of any performance improvement strategy by mid-level and senior leadership. However, to create enduring change, the full engagement of hourly associates is key. “What is happening in RIA is transformational. It’s not a hurried in-and-out, a triage operation. A manufacturer needs a sustainable, enduring solution that not only hits the immediate target, but supports all levels of the workforce, from the hourly associate on up, today and tomorrow,” McIntyre advises.
Caldwell and O’Connor believe decision-makers at manufacturing companies should be mindful of differentiators like the ones McIntyre describes. “It’s probably not vital that a client knows that I can handle a lift truck or I’ve owned a pair of steel toes. Yet, I think that does make a difference in establishing empathy and understanding. I know the true effects of RIA. The folks I work with benefit from a world of experience I can apply to their situation,” observes Caldwell.
O’Connor agrees. “I’ve sat on both sides of the table,” he says. “I’ve run plants. I’ve dealt with performance issues my entire career. It’s our obligation to leave behind a legacy a company can build on.”
Next Steps
No manufacturing company is free from performance issues. For some, it’s realizing the extra margins and operational dividends that result from lifting a so-so OEE rating to the next level. For others, it’s improving processes that already work.
Companies that are willing to commit to the all-in approach that RIA offers will see rapid ROI as the number of defects fall away, equipment runs better, throughput multiplies and morale improves among frontline workers.
Your journey to ever-higher levels of manufacturing excellence requires a seasoned, discerning pathfinder. As you weigh your performance improvement options, it pays to consider all aspects of your service provider. Do they come conditioned with a wide and deep background in manufacturing excellence? Is the practitioner exactly that — a professional seeped in frontline reality and experience? Are you working with a partner happy to open their plant floor door for a first-hand inspection?
Performance Solutions by Milliken (PSbyM) is a global team that specializes in RIA and has a proven track record of success. Get in touch today to explore how you can transform your operations.
Milliken & Company is a 159-year-old privately owned and technology-based company headquartered in Spartanburg, South Carolina. The firm employs over 8,000 associates worldwide and is considered one of America’s Most Innovative Companies by Fortune, just one of 11 manufacturers on the 2023 list. The company holds 2,500 U.S. patents and more than 5,500 patents worldwide.
The firm is relentlessly dedicated to manufacturing quality across its global manufacturing network. It closely studies production methods worldwide and aggressively implements ‘the best of the best’ practices in its plants, which are frequently used as educational and training showcases. The approach has garnered numerous industry honors, including the Malcolm Baldridge National Quality Award, European Quality Award, British Quality Award, Canadian Quality Award, Japan Institute of Plant Maintenance TPM Excellence Award, America’s Safest Company, Fortune’s 100 Best Companies to Work For and is included on World’s Most Ethical Companies list, among other distinctions.
As the former CEO Roger Milliken summed up the Milliken philosophy, “Operational excellence secures the present. Innovation excellence secures the future.”
The content & opinions in this article are the author’s and do not necessarily represent the views of ManufacturingTomorrow
Comments (0)
This post does not have any comments. Be the first to leave a comment below.
Featured Product
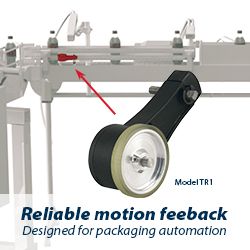