Effects of Anodized Aluminum in CNC machining
Surface treatment is an important part of the CNC aluminum machining process, with a variety of methods and different results. Sometimes only one method can meet the requirements, and sometimes a variety of methods can be used to meet the requirements of the product. Among them, anodizing is the most widely used method.
There are 7 major effects of CNC aluminum machining for anodizing as follows:
1.Enhance the corrosion resistance of aluminum parts.
Anodizing treatment on the surface of CNC parts to form a layer of oxidation film, this film is chemically stable and makes the surface of CNC parts harder, more wear-resistant, while reducing the erosion of various chemical reactions on the CNC parts to improve their corrosion resistance. Anodizing can change the colour of the surface of CNC parts, provide a variety of colour options, improve the decorative effect of CNC parts, keep the surface clean, beautiful, and not easy to be affected by the outside world.
2.Improve the adsorption capacity of aluminum parts to materials.
Aluminum products are chemically or electrochemically polished and then anodized to form a highly transparent oxidation film on the surface. In addition, the oxidation film is porous and has good adsorption capacity, which can effectively adsorb a variety of organic or inorganic dyes, as well as paints and organic films. This aluminum product can come in a variety of vibrant colours, which not only adds to the beauty of the appearance, but also provides excellent corrosion protection. The surface of some industrial aluminum profiles needs to be sprayed with paint, and the surface voids of the anodized aluminum profiles have strong adsorption, which makes the spray paint more even and beautiful.
3.Improve the wear resistance of aluminum parts.
The anodized film is not only corrosion resistant, but also very dense.
The presence of this oxidation film greatly enhances the wear resistance of aluminum products and effectively adapts them to frictional working conditions. The porous oxidation film on the surface has the ability to adsorb lubricants, making the surface of industrial aluminium profiles more wear-resistant, such as automobile engine cylinders, pistons and other parts of the use.
4.Improve thermostability
The thermal conductivity of the anodizing oxidation film is much lower than that of the aluminum profile substrate. The aluminum oxidation film can withstand high temperatures up to 1500 degrees Celsius, while the aluminum profile substrate can only withstand high temperatures of up to 660 degrees Celsius. Aluminum's electrical conductivity is very good, but aluminum profiles need to be insulated in some situations. Anodizing oxidation films, on the other hand, are chemically structured as metal oxides rather than metals and are highly electrically insulating. Some aluminum materials require electrical insulation, such as capacitive dielectric layers. This can be achieved by anodizing.
5.Realize the electrical insulation of aluminum parts.
The non-conductive oxidation layer formed during the anodizing process to improve the electrical insulation of the part, make it suitable for use in electronic components and equipment. Anodized surfaces provide an excellent basis for the application of paints, primers and other coatings, ensuring strong adhesion and long-lasting results. Anodizing is an environmentally friendly process as the chemicals used can be recycled and the resulting oxide layer is non-toxic and harmless.
6.As a substrate for aluminium plating
Aluminum products must be coated on the substrate before plating. There are various methods of applying a primer to the surface of aluminum products, including zinc plating, zinc dipping, chemical nickel plating and, of course, anodizing. Due to the porous nature of the anodized film, the plating process can be facilitated.
7.Protect against electromagnetic interference
For special CNC parts such as electronic parts, certain electromagnetic waves may be generated during operation. After anodizing, the sealed oxide film formed on the surface can effectively prevent electromagnetic interference and ensure that the equipment is not affected by any external factors.
Aluminium is a very common metal in industry and life. In aluminium alloy processing, anodizing is a very important surface treatment method, which can enhance corrosion resistance, improve adsorption capacity, wear resistance, thermal insulation and electrical insulation, and can be used as an aluminium-plated substrate to improve the performance and quality of aluminium products. At GD Prototyping, machining aluminum parts is one of our strengths in terms of CNC machining services, affordable prices, beautiful surfaces, quality and performance.
The protective oxidation layer formed during the anodizing process improves the wear, corrosion and UV damage resistance of the part, resulting in a more durable component, and anodized parts present a uniform, attractive finish that can be further coloured using dyes for a wide range of colours and appearances.
Featured Product
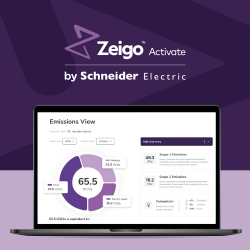
Zeigo Activate by Schneider Electric: Energy efficiency software for manufacturing facilities.
Whether you're responding to new legislation and regulations or getting pressure from stakeholders and customers, Zeigo Activate empowers companies to effectively calculate, track, and reduce their carbon footprint and become more energy efficient. By providing valuable insights, actionable data, and intuitive tools, Zeigo Activate is tailored for businesses at any stage in their energy efficiency journey. Our easy-to-use software allows you to set your emissions baseline and target, receive a customizable project roadmap, and connect to a network of regional solution providers in energy efficiency and renewable energy so that you can put your ambitions into action.