Ultimation Industries Recommends Material Handling Solutions for a Safer New Year
Suggestions include five products that offer better ergonomics, product safety or injury prevention
Manufacturers, distributors and warehouses can ring in a safer new year with material handling solutions that offer product protection, minimize injuries and improve ergonomics, according to Ultimation Industries. Ultimation is an MCE company that solves productivity challenges with special purpose machinery and industrial automation equipment systems as well as direct-to-consumer solutions for a broad range of end-markets, including energy, automotive, logistics and vertical farming.
"The new year is a great time to take stock of potential material handling safety concerns and explore options for making improvements," said Carl Milodrowski, operations manager for Ultimation. "A well-designed conveyor system can help companies keep personnel, packages and products safe throughout the year and well into the future."
"A well-designed conveyor system can help companies keep personnel, packages and products safe throughout the year and well into the future."
Milodrowski provides five product suggestions companies can use to keep workers and products safe in their facilities:
--Injury prevention. Safety light curtains are often used within manufacturing and industrial settings to protect personnel from injury and hazards from dangerous equipment or devices. When the light curtain is interrupted, photoelectric sensors send a signal to stop the connected machine before an injury can occur. They can also be used to safeguard machines and robots from damage. Installation of light screens is quick and easy, thanks to their compact design and the variety of mounting brackets for multiple applications.
-- Ergonomics. Eliminating repetitive bending and stretching in the workplace could be as simple as making sure the facility's gravity conveyors are at the appropriate height. Ultimation offers stationary floor support legs in a wide range of widths and heights, with each style offering adjustable height ranges. They are available in light, medium and heavy duty versions depending upon the load weight.
Another way to improve ergonomics in a warehouse or distribution center is through the use of Autonomous Mobile Robots (AMR) to carry loads that would be too heavy for humans. When fitted with an appropriate top module, AMRs can move their loads safely alongside production workers without the need for pre-programmed paths or routes. When obstacles appear in front of them, they quickly find alternate safe paths to the destination just like a self-driving car. The speed of the AMR will change according to its safety conditions. Speeds are generally in the range of 3 - 6 mph (5-10 km/h) which matches typical warehouse walking speeds.
--Product safety. Recent news reports have been filled with stories about food recalls. While the sources of contamination vary, food manufacturers and distributors can make sure their material handling systems aren't one of them. Food-grade conveyors are one of the most important parts of the food and beverage industry because they transport raw ingredients, organic materials and other consumable goods within the facility and ultimately out to the consumer. Unlike regular industrial conveyors, food and washdown material handling solutions must be constructed of sanitary and hygienic materials to meet rigorous safety standards. Belt conveyors are often used in food applications because they offer a smooth, continuous surface and are easy to clean.
Keeping products safe during their movement through a manufacturing or distribution facility can depend on the type of conveyor system in use. Motor-driven roller conveyors (MDR) are a mainstay due to their fast, smooth package movement and sensors that ensure packages don't get damaged by crushing against each other. Various lengths, widths, zones and roller spacing configurations, including curved sections, provide the ability to customize a solution without specialized engineering expertise. Gravity conveyors can easily be converted to a motorized roller system for faster, smoother package movement.
For more ideas on how to improve material handling safety, visit the Ultimation website at https://www.ultimationinc.com/ for more information.
About Ultimation, an MCE company
Ultimation Industries, LLC is the leading direct-to-consumer conveyor manufacturer serving the automotive, food processing, vertical farming, heavy equipment, warehousing, fulfillment and delivery industries. The company offers a line of proprietary automation systems and is also the largest integrator of Jervis Webb Conveyor Systems. Ultimation's e-commerce channel sells Ultimation, Interroll, Itoh Denki, Jervis Webb, and a wide range of other conveyor equipment.
Ultimation became part of the Motion & Control Enterprises (MCE) family of companies in 2023. Visit https://www.ultimationinc.com/ for the latest product information and news about Ultimation.
Featured Product
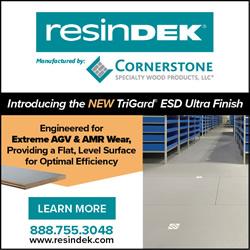