The Future of 3D Printing Materials and Innovations: Shaping Tomorrow’s World
The 3D printing materials market is expanding rapidly, driven by adoption in aerospace, healthcare, and automotive industries. Key materials include plastics, metals, and ceramics, with plastics leading due to versatility and cost-effectiveness. Metals are growing for high-strength applications, while ceramics are used for heat resistance. Trends include sustainable materials and mass production integration. North America and Europe dominate, but Asia-Pacific is growing fast due to manufacturing advancements.
3D printing, or additive manufacturing, has come a long way since its inception. What began as a tool for rapid prototyping has evolved into a transformative technology capable of producing everything from custom medical implants to entire houses. While the printers themselves have seen significant advancements, the real game-changer lies in the materials being used. The future of 3D printing is being shaped by groundbreaking innovations in materials science, which are expanding the boundaries of what can be created. From sustainable options to smart materials that respond to their environment, the possibilities are endless. In this blog post, we'll explore the exciting developments in 3D printing materials and how they are poised to revolutionize industries and everyday life.
The global 3D printing materials market is experiencing significant growth, driven by advancements in additive manufacturing technologies and increasing adoption across industries such as aerospace, healthcare, automotive, and consumer goods. The market is segmented by product type, including ceramics, plastics, metals, and others, with plastics currently dominating due to their versatility and cost-effectiveness.
Metals are gaining traction for high-performance applications, while ceramics are emerging in niche sectors requiring heat resistance and durability. Key trends include the development of sustainable materials, customization for specific industries, and the integration of 3D printing in mass production. North America and Europe lead the market, but Asia-Pacific is expected to witness rapid growth due to expanding manufacturing capabilities and rising investments in 3D printing technologies.
Beyond Plastics: A World of Diverse Materials
For years, 3D printing has been synonymous with plastics like PLA (polylactic acid) and ABS (acrylonitrile butadiene styrene). These materials are affordable, easy to use, and versatile, making them ideal for prototyping and consumer products. However, as the technology matures, the demand for more advanced materials has grown. Today, 3D printing is no longer limited to plastics. Metals such as titanium, aluminum, and stainless steel are now commonly used in industries like aerospace and healthcare, where strength, durability, and precision are critical. For instance, titanium is widely used for 3D-printed medical implants because of its biocompatibility and resistance to corrosion. Similarly, aluminum is favored in the automotive and aerospace sectors for its lightweight yet robust properties.
But the innovation doesn't stop there. Composites, which combine two or more materials to enhance performance, are gaining traction. Carbon fiber-reinforced polymers, for example, are being used to create parts that are both lightweight and incredibly strong, making them ideal for applications in robotics and automotive manufacturing. Ceramics, too, are emerging as a key material for 3D printing, particularly in industries that require heat-resistant components, such as electronics and energy. And then there are biomaterials, which are opening up entirely new possibilities in healthcare. From biodegradable scaffolds for tissue engineering to 3D-printed organs, these materials are pushing the boundaries of what's possible in medicine.
Sustainability in 3D Printing: A Greener Future
As the world grapples with the challenges of climate change and environmental degradation, sustainability has become a top priority for industries across the board. The 3D printing industry is no exception. In recent years, there has been a significant push toward developing eco-friendly materials that reduce the environmental impact of manufacturing. One of the most promising developments is the use of recycled plastics. Companies are now producing filaments made from recycled PET bottles, turning waste into valuable resources. This not only helps reduce plastic pollution but also lowers the cost of materials, making 3D printing more accessible.
Biodegradable polymers are another area of focus. Materials like PHA (polyhydroxyalkanoates) and PLA are derived from renewable sources such as cornstarch and sugarcane, making them a sustainable alternative to traditional petroleum-based plastics. These materials break down naturally over time, reducing the long-term environmental impact. Additionally, researchers are exploring the use of natural fibers like hemp, flax, and even wood-based filaments. These materials are not only sustainable but also offer unique aesthetic and functional properties, making them ideal for consumer products and prototyping. The shift toward sustainable materials is not just a trend—it's a necessity, and it's reshaping the future of 3D printing.
Smart Materials and the Rise of 4D Printing
While 3D printing has already revolutionized manufacturing, the next frontier is 4D printing—a technology that adds the dimension of time to the equation. 4D printing involves using smart materials that can change shape, color, or functionality in response to external stimuli such as heat, light, or moisture. Imagine a 3D-printed pipe that can expand or contract based on water flow, or a medical stent that adjusts its shape to fit a patient's anatomy. These are not futuristic fantasies; they are real-world applications being developed today.
Shape-memory alloys are one example of smart materials used in 4D printing. These materials can be deformed into a temporary shape and then return to their original form when exposed to heat or another trigger. Self-healing polymers are another exciting development. These materials can repair themselves when damaged, extending the lifespan of 3D-printed objects and reducing waste. Responsive materials, which react to environmental changes, are also being explored for applications in robotics, aerospace, and even fashion. The potential of 4D printing is vast, and it's set to redefine how we think about manufacturing and design.
Nanomaterials: Precision at the Molecular Level
At the cutting edge of materials science are nanomaterials, which operate at the molecular or atomic level. These materials offer unparalleled precision and functionality, making them ideal for advanced applications. Graphene, for instance, is a nanomaterial known for its exceptional strength, flexibility, and electrical conductivity. It's being used to create lightweight, durable components for electronics, sensors, and even energy storage devices. Nanocomposites, which incorporate nanoparticles into traditional materials, are also gaining attention. These composites enhance mechanical, thermal, and electrical properties, making them suitable for high-performance applications in aerospace, automotive, and healthcare.
The use of nanomaterials in 3D printing is still in its early stages, but the potential is immense. For example, researchers are exploring the use of nanomaterials to create highly sensitive sensors that can detect minute changes in temperature, pressure, or chemical composition. In the medical field, nanomaterials are being used to develop targeted drug delivery systems and advanced imaging techniques. As research progresses, we can expect to see even more innovative applications of nanomaterials in 3D printing.
Customization and On-Demand Manufacturing
One of the most exciting aspects of 3D printing is its ability to enable customization and on-demand manufacturing. With advancements in materials science, it's now possible to create tailored materials for specific applications. In the medical field, for example, patient-specific implants can be 3D-printed using biocompatible materials that match the patient's anatomy. This not only improves the effectiveness of the implant but also reduces the risk of complications. In the aerospace industry, lightweight, high-strength materials are being developed to meet the unique demands of aircraft and spacecraft components.
Consumer goods are also benefiting from this trend. Companies can now offer products with unique textures, colors, and properties, all tailored to the customer's preferences. This level of customization was unimaginable just a few years ago, but thanks to 3D printing, it's becoming a reality. On-demand manufacturing, where products are printed only when needed, is also reducing waste and inventory costs, making it a more sustainable and efficient approach to production.
Challenges and Opportunities Ahead
While the future of 3D printing materials is undoubtedly exciting, there are challenges that need to be addressed. One of the biggest hurdles is cost. Advanced materials like graphene and shape-memory alloys can be expensive, limiting their accessibility. Regulatory hurdles, particularly in industries like healthcare and aerospace, also pose challenges. Ensuring that 3D-printed products meet safety and quality standards is crucial, but it can slow down the adoption of new materials and technologies. Scalability is another issue. While it's relatively easy to produce small batches of 3D-printed objects, scaling up production without compromising quality remains a challenge.
Despite these challenges, the opportunities far outweigh the obstacles. The growing demand for sustainable materials, the rise of smart and nanomaterials, and the ability to customize products are driving innovation and investment in the 3D printing industry. Collaboration between researchers, manufacturers, and policymakers will be key to overcoming these challenges and unlocking the full potential of 3D printing materials.
Featured Product
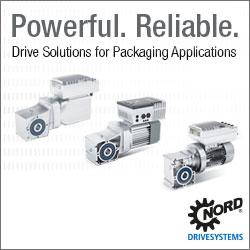