INFICON ELT Vmax delivers first industry-scale, production speed battery leak testing
INFICON recently showed two innovative leak-testing solutions aimed at automated, industrial-scale leak testing at the recent Advanced Automotive Battery Conference (AABC) in Las Vegas, Nevada at Mandalay Bay Resport & Casino. One of the systems, the company's ELT Vmax, is specifically designed for industry-scale mass-production environments using automated leak testing stations.
INFICON, a global leader in leak detection technology, showed two innovative leak testing solutions aimed at industrial-scale leak testing at the recent Advanced Automotive Battery Conference (AABC) in Las Vegas, Nevada at Mandalay Bay Resort & Casino. The ELT Vmax is specifically designed for industry-scale mass-production environments using automated leak testing stations, and ELT3000 PLUS features Dual Operating Modes; a stand-alone mode for battery development and pilot projects plus automation mode for integration into processes.
The ELT Vmax and ELT3000 PLUS rapidly test leak-tightness of all types of battery cells regardless of the type of electrolyte including all metal-ion batteries such as lithium-ion and sodium-ion traction battery cells, plus the ability to test semi solid-state batteries. Both use INFICON'S patented "Direct Electrolyte Leak Detection" method to detect electrolyte leakage from filled cells, without changes in production line speeds.
For production environments, the ELT Vmax delivers the capacity to test thousands of individual cells per hour at full line-speed and provides highly individual customized leak-test solutions. Alternatively, the ELT3000 PLUS is perfect for Research and Development, laboratory and pilot line leak testing with manual loading of battery cells and modules.
In either scenario, completed cells are placed into a vacuum chamber. There, ELT Vmax or ELT3000 PLUS maintains precision and sensitivity using INFICON's powerful mass spectrometer system and detects minute leaks down to single-digit micrometer diameters, equivalent to a helium leak rate of 5∙10-7 mbar∙l/s. Such sensitivity is impossible or impractical for alternative leak testing methods (water immersion or pressure decay) as it represents a leak rate of one drop of water over many months; pressure decay can be easily and swiftly affected by minute environmental changes.
"ELT Vmax supports multi-chamber operation in test stations with several vacuum test chambers where cells are tested in batches, for example 16, 32 or 64 units, in less than 15 seconds," said Thomas Parker, automotive leak testing sales manager at INFICON. "If a batch fails, automatic repeat tests are carried out by halving the batch size until the defective cell is identified, typically in an offline process."
"Batteries may have very large leaks which can contaminate the testing environment. The ELT Vmax' rapid detection of large leaks ensures that escaping electrolyte does not heavily contaminate the testing environment," Parker commented.
Parker also noted that regularly scheduled verification of the testing system's functionality is essential to validation. "INFICON offers a calibration leak called E-Check 2.0 for fixed integration and fully automated calibration which takes less than 30 seconds, and a simple test measurement to verify test accuracy that can be performed within the typical testing cycle time, normally around 12 seconds. This means that, for the first time, battery manufacturers can offer true 100-percent validation."
About INFICON:
INFICON is a leading provider of innovative instrumentation, critical sensor technologies, and Smart Manufacturing/Industry 4.0 software solutions that enhance productivity and quality of tools, processes, and complete factories.
These analysis, measurement and control products are also essential for gas leak detection in air conditioning/refrigeration, and automotive manufacturing. Other users of vacuum-based processes include the life sciences, research, aerospace, packaging, heat treatment, laser cutting and many other industrial processes. We also leverage our expertise in vacuum technology to provide unique, toxic chemical analysis products for emergency response, security, and environmental monitoring.
INFICON is headquartered in Switzerland and has world-class manufacturing facilities in Europe, the United States and China, with subsidiaries on three continents.
For more information, please visit www.inficon.com or contact reachus@inficon.com.
###
Featured Product
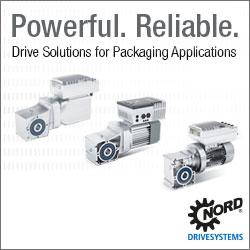