KUKA Educated More than 200 at Manufacturing Automation Tech Day
A direct response to on-going labor shortages, AMRs allow manufacturers to automate repeated intralogistics functions. At Manufacturing Automation Tech Day, KUKA showcased its newest AMRs - the KMP 600P, KMP 1500P and KMP 3000P.
SHELBY TOWNSHIP, Mich., March 13, 2025- KUKA Robotics opened its doors to more than 200 people for Manufacturing Automation Tech Day at the company's North American headquarters in Shelby Township, Michigan on Wednesday, February 26, 2025. Developed for manufacturers across the Midwest and Southern Ontario challenged by labor shortages and increased production goals, KUKA's interactive curriculum featured autonomous mobile robots (AMRs), automated machine tool solutions and welding robotics.
A direct response to on-going labor shortages, AMRs allow manufacturers to automate repeated intralogistics functions. At Manufacturing Automation Tech Day, KUKA showcased its newest AMRs - the KMP 600P, KMP 1500P and KMP 3000P.
The KMP 600P is the most compact platform in KUKA's high-performance P series of AMRs to date and is particularly suitable for confined production environments. With a 600-kg payload, the KMP 600P is a cost-effective platform for efficient material supply from the warehouse to work stations, assembly lines or preassembly lines as well as for process linking and reliable point-to-point transporting.
The KMP 1500P features intelligence, safety and easy commissioning to navigate complex, dynamic environments with the SLAM (Simultaneous Localization and Mapping) navigation method. The AMR platform automatically identifies loads with QR code readers, and 3-D cameras detect obstacles.
With the capacity to transport loads up to three tons in any direction, including diagonally, the KMP 3000P's omnidirectional drive ensures maximum flexibility in the tightest of spaces. Four integrated 3D cameras and two laser scanners enable a 360° view, allowing the platform to recognize obstacles and drive around them safely.
For manufacturers seeking lights-out production capabilities to meet increasing production goals, KUKA created a fully operational automated shop for event attendees. A KR CYBERTECH robot, using a Roboception vision system and KUKA's SmartBinPicking software, randomly picked steel billets from a bin, placed them onto portable part trays, and then moved the billets for processing through a Goodway CNC turning center. Within the automated demo, the bin-picking KR CYBERTECH robot was equipped with a SCHUNK robotic tool change system and a Magswitch magnetic gripper, while FESTO brand valves provided the end of arm tooling control. The powerful multi-functional KR CYBERTECH robots are specially designed for handling large components in machining, assembly, palletizing and arc welding applications. Load capacities from 8kg to 35kg and maximum arm reaches of 1612mm to 2013mm.
For the machine-tending robot, a standard CNC turning machine tending solution from MAIROTEC, featuring a KR CYEBTERCH nano robot quipped with Zimmer grippers, allowed for fenceless operation. The KR CYBERTECH nano series is compact, robust, streamlined, agile and flexible with reaches that include 1820 mm, 1620 mm and 1420 mm. For material handling applications, the KR CYBERTECH nano product family is also available in a high protection version.
For foundries and fabricators, KUKA offered guests ways to expand current workforce capabilities with arc, spot and friction stir welding robotic solutions. For arc welding, KUKA brought its arc Edition robots to the demonstration floor for Manufacturing Automation Tech Day. Ideal for shops that are ready to implement their first robotic welder, the Edition series draws on KUKA's current technology portfolio, including welding software and offers simplified, focused and reliable technology at lower procurement costs.
Applicable to a variety of the event guests, in particular those who work in Automotive Tier 1 environments, KUKA's KR QUANTEC industrial robots featured spot welding applications. With the best reach and payload in this category of robots, KR QUANTEC is built to work in virtually any market segment, from automotive to medical.
The versatile heavy-duty KR FORTEC was in the spotlight for friction stir welding at the event. The KR FORTEC is suitable for a wide range of applications. In particular, the Machine Tool variant of the robot is ideal for milling applications in the high payload range, while the Foundry variant performs heavy-duty tasks for foundry work. Further, the robot's compact design is a space-saver on production floors.
Additional automation and robotic demonstrations were open and available during Manufacturing Automation Tech Day including but not limited to primary food handling and consumer goods packaging.
As with all the company's automation solutions, those shown at Manufacturing Automation Tech Day are backed by KUKA's expert service and support for training, complete system engineering and simulation, readily available spare parts, robot refurbishment and more. All of these features are easily accessible through the my.KUKA.com site, and KUKA maintains corporate offices and production operations, along with integration partner facilities, throughout North America to provide responsive customer service and support.
KUKA
KUKA is a global automation corporation with sales of around 3.3 billion euro and roughly 14,000 employees. The company is headquartered in Augsburg, Germany. As one of the world's leading suppliers of intelligent automation solutions, KUKA offers customers everything they need from a single source: from robots and cells to fully automated systems and their networking in markets such as automotive, electronics, metal & plastic, consumer goods, e-commerce/retail and healthcare.
Featured Product
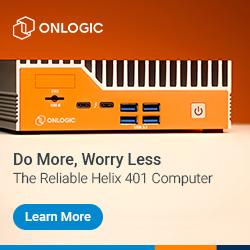