MORGAN ADVANCED MATERIALS EXTENDS REFLECTOR GLAZE RANGE
Developed for high-energy pulsed Q-switching infrared laser applications, a new, high-absorption samarium oxide glaze from Morgan Advanced Materials means it is now able to offer three grades of glaze for laser systems.
Developed for high-energy pulsed Q-switching infrared laser applications, a new, high-absorption samarium oxide glaze from Morgan Advanced Materials means it is now able to offer three grades of glaze for laser systems.
The samarium glaze absorbs radiation at the Nd-YAG lasing wavelength of 1,064nm, and its further transitions near 940nm, 1120nm, 1320nm and 1440nm. A significant amount of fluorescent radiation at the lasing wavelength escapes laterally from the laser rod into the surrounding pumping cavity. Absorbing this radiation prevents it from being reflected back into the laser rod, which would in turn stimulate decay from the upper laser transition level, thereby limiting the number of excited ions which can occupy that level. By preventing this decay, the maximum output energy obtained from the laser is increased. Morgans high- absorption samarium oxide glaze is formulated through the controlled addition of dopant to create optimum reflectance properties
Applying the glaze to Morgans Sintox AL laser pump cavity material produces the high diffuse reflectivity required to achieve uniform illumination of the laser rod surface. Providing typically 98 per cent reflectance in the desired wavelength range, the new samarium oxide glaze matches yellow (GSY) and clear (GSO) glazes between 700 nm and 900nm. The optimum reflectance capability across the range of three glazes now spans wavelengths of around 580nm up to 2,000nm.
Yannick Galais of from Morgan explains: "As diode laser technology becomes more specialised, we continually evaluate our glaze formulations, in partnership with leading laser manufacturers, to improve the reliability of new equipment. Our samarium oxide glaze improves performance in the specified wavelength range and is suitable for high-energy, niche applications such as industrial metal cutting.
"The new glaze perfectly complements our existing yellow glaze - which reduces laser cavity temperatures by absorbing extremely low wavelengths, meaning less cooling fluid needs to be used - as well as our clear glaze, which seals ceramic reflectors against the ingress of cooling fluid."
Morgans laser reflectors are produced from high-performance alumina-based ceramic and boast high strength, good thermal conductivity and excellent dimensional and electrical stability at all operating temperatures. A cost-effective alternative to metal-coated reflectors, ceramic reflectors are also resistant to chemical attack and, when sealed with one of Morgans glazes, benefit from an increased life span and reduced total cost of ownership.
For further information visit http://www.morgantechnicalceramics.com/laserreflectors.
Featured Product
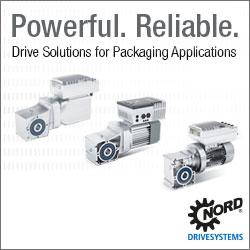
NORD Delivers Powerful, Reliable Drive Solutions for Demanding Packaging Applications
When you need quality, flexibility and high efficiency, NORD has you covered with complete drive solutions for primary and secondary packaging, end-of-line packaging, and higher-level applications. NORD supports you through the entire life cycle of your drive systems with pre-sales engineering support, online tools, and a global service network. Drive systems for both vertically and horizontally networked technology with all the options for sensor incorporation and integration into the higher-level control system.