V8 Piezo-Walk Technology Powers Vacuum Compatible Nanopositioning Stage, new from PI
UHV option is ideal for applications in semiconductor and beamline research. The compact design facilitates the integration of the new N-332 linear positioner.
PI's new N-332 nanometer-precision linear stage family, configurable to multi-axis setups of XY, XZ and XYZ, is designed for high-end applications in semiconductor technology, fiber-optics, microscopy, bio-nanotechnology, metrology and scientific research in beamlines and laser labs. The stages have a low profile of 30mm and a small footprint of 80x110mm an 80x160mm with travel ranges of 1" and 2", respectively.
No Brake or Counterbalance Required
Due to the high active force of 75N and power-off passive holding force of 80N, the N-332 nanopositioning stage does not require a brake or counterbalance when operated in vertical orientation.
UHV-Option
For demanding applications that require operation in high vacuum, N-332 stages are available in configurations suitable for pressures down to 10-9 hPa. The self-clamping nature of the piezo motor allows the stage to hold a position without heat generation.
PICMA-Walk Technology - High Force and High Resolution
The PICMA-Walk piezo motor inside the N-332 stage is based on 4 pairs of PI's proprietary PICMA® piezo actuators, arranged in a V8 configuration. PICMA® piezo actuators were successfully tested for 100 billion cycles by NASA/JPL before being used on the Mars Rover's instrumentation lab. PICMA-Walk motors provide high force linear motion to 75N and are capable of sub-nanometer resolution and self-locking when de-energized - a great advantage for applications where a stable position must be maintained without power, heat generation or servo jitter.
Featured Product
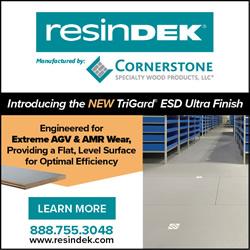