Fonseca Advisers Launches Field & Repair Service Add-On for BEAS Manufacturing
Fonseca Advisers introduces a powerful Field & Repair Service add-on for BEAS, seamlessly integrating with SAP Business One to transform field and repair operations with real-time data and efficient workflows.
Fonseca Advisers is excited to announce the launch of its latest innovation, the Field & Repair Service add-on powered by BEAS Manufacturing. Designed for manufacturers who face complex, fragmented field and repair service challenges, this solution integrates seamlessly with SAP Business One to streamline service operations, boost productivity, and enhance customer satisfaction.
The Field & Repair Service add-on offers a comprehensive suite of tools tailored to support in-house and field service management. Key features include robust service administration, web-based data capture for real-time updates, and support for third-party integrations—allowing manufacturers to maintain control of both office and field-based tasks on a single platform.
"Today's manufacturers need agile, connected solutions that keep pace with the demands of the field," said [Milton Fonseca, CEO of Fonseca Advisers. "Our Field & Repair Service add-on empowers businesses to reduce operational complexity and improve field service productivity by bringing all service functions—from dispatch to invoicing—under one system. This means faster response times, accurate billing, and a better experience for customers."
This release aligns with Fonseca Advisers' mission to simplify operations for manufacturers through innovative technology solutions. With the new add-on, manufacturers can look forward to reduced operational costs, higher service efficiency, and an ability to capture real-time data for faster decision-making.
The Field & Repair Service add-on is available now for BEAS Manufacturing and SAP Business One.
Featured Product
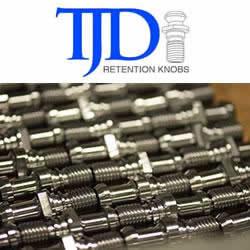