International Thermal Systems Enhances Aerospace Manufacturing with Custom Batch Oven Solution
International Thermal Systems (ITS) has successfully partnered with an aerospace company to address significant operational challenges by designing and delivering a customized batch oven solution.
International Thermal Systems (ITS) has successfully partnered with an aerospace company to address significant operational challenges by designing and delivering a customized batch oven solution. The collaboration highlights ITS's commitment to safety, efficiency, and customer satisfaction.
Challenge Overview
The aerospace company faced critical issues with their existing batch oven, including:
-An unsafe operating environment due to a defective plate floor.
-A lack of user-friendly features, complicating operation.
-Persistent floor damage that prior vendors had failed to address.
ITS Objectives
International Thermal Systems set out to:
1-Replace the unsafe, outdated batch oven with a safer, modern alternative.
2-Enhance usability with updated controls and optimized loading/unloading processes.
3-Repair the defective plate floor and provide a long-term, reliable solution.Innovative Solutions
To meet these objectives, ITS implemented the following:
-Designed and installed a state-of-the-art batch oven equipped with melting wax technology for optimized production processes.
-Incorporated advanced control systems for improved operational ease and precision.
-Delivered a durable plate floor repair, ensuring a safe and reliable foundation for operations.
-Customer Benefits
The aerospace company now enjoys:
-A significantly safer working environment with a modernized batch oven.
-Streamlined workflows through intuitive controls and efficient transportation systems.
-Confidence in ITS commitment to excellence, reflected in the seamless project execution.
-Customer Satisfaction
The aerospace company expressed high levels of satisfaction with ITS innovative approach and professional service. The new oven has transformed their manufacturing process, ensuring safety and operational efficiency.
About ITS Batch Ovens
Industrial Batch Ovens can be used for a wide variety of heat processes including drying, curing, powder coating, aging, annealing, stress relieving, bonding, composite curing, tempering, preheating, and forming. ITS manufactures both large and small walk in ovens that can be used for a wide variety of heat treating applications. Standard batch ovens are offered in many sizes, with multiple options available upon request. ITS also manufactures custom engineered batch ovens.
What makes an ITS Batch Oven the best walk-in batch oven in the industry? Air Flow Design.
Learn more: https://www.internationalthermalsystems.com/industrial-ovens/batch-oven/
Contact us to discuss your need for a batch oven: 414-672-7700
International Thermal Systems
International Thermal Systems (ITS) is a global leader in designing and manufacturing industrial ovens, washers, and furnaces. With a focus on innovation and customer success, ITS provides tailored solutions to meet the demands of various industries, including aerospace, automotive, and more.
Featured Product
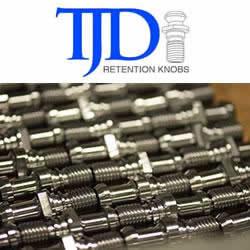
T.J. Davies' Retention Knobs
Our retention knobs are manufactured above international standards or to machine builder specifications. Retention knobs are manufactured utilizing AMS-6274/AISI-8620 alloy steel drawn in the United States. Threads are single-pointed on our lathes while manufacturing all other retention knob features to ensure high concentricity. Our process ensures that our threads are balanced (lead in/lead out at 180 degrees.) Each retention knob is carburized (hardened) to 58-62HRC, and case depth is .020-.030. Core hardness 40HRC. Each retention knob is coated utilizing a hot black oxide coating to military specifications. Our retention knobs are 100% covered in black oxide to prevent rust. All retention knob surfaces (not just mating surfaces) have a precision finish of 32 RMA micro or better: ISO grade 6N. Each retention knob is magnetic particle tested and tested at 2.5 times the pulling force of the drawbar. Certifications are maintained for each step in the manufacturing process for traceability.