Discussion on thin-walled parts processing technology in CNC parts processing
With the continuous development of the manufacturing industry and the advancement of technology, thin-walled parts are increasingly used in aerospace, automotive, electronics and other fields.
In the
field of CNC parts processing, thin-walled parts processing technology is a key technology used to process parts that require lightweight structures and reduced weight. Thin-walled parts processing requires consideration of factors such as material selection, tool path planning, and processing parameters to ensure accuracy and stability during processing. The use of advanced CNC equipment and precision tools, combined with reasonable processing technology, can effectively improve the quality and efficiency of thin-walled parts processing.CNC thin-wall parts processing technology and tooling design points1. Core of tooling technology1)Combined tooling designAdopt modular combined structure (such as base, sleeve, stopper and fixing parts), reduce local stress concentration through multi-point uniform clamping, realize precise positioning of thin-walled shell parts, and reduce clamping deformation.The support ring and the annular shell can enhance the rigidity of the parts and avoid vibration deformation caused by cutting force during processing.2)Flexible tooling applicationThrough electromechanical and hydraulic integration technology and multi-sensor control, the clamping force can be adjusted in real time to adapt to the dynamic rigidity changes of parts. For example, the aerospace field uses adjustable positioning clamping elements to meet the clamping needs of thin-walled parts of different sizes and specifications.3)Auxiliary support technologyAdd multi-point auxiliary support (such as hydraulic or mechanical ejector) to the weak rigidity area to improve the local rigidity of the processing part. For example, when the aerospace field uses honeycomb grid wall panels for processing, auxiliary support is used to reduce warping deformation.4)Special mandrel and positioning structureFor thin-walled tube parts, use mandrel positioning with equal-height positioning blocks to avoid clamping force acting directly on thin-walled areas and reduce the risk of elliptical deformation2. Processing technology optimization1)Phase-based processing strategyUse a progressive process of roughing → semi-finishing → finishing to gradually release the internal stress of the material. After roughing to remove the excess, semi-finishing is used to correct the deformation, and the final finishing is done to achieve the required accuracy.2)Tool parameter and path optimizationImprove tool rigidity (such as increasing the cross-sectional area of the tool holder) and optimize the tool angle to reduce radial cutting force; use small cutting depth and high speed cutting parameters to reduce thermal deformation.Use five-axis linkage milling or dynamic milling path for complex surfaces to avoid local deformation caused by repeated cutting of the same area by the tool.3)Cooling and vibration controlMake full use of coolant to reduce cutting temperature, and combine dynamic cooling technology to control thermal deformation; reduce cutting force transmission and suppress vibration through high-speed cutting (above 15,000 RPM).3. Industry Application Cases1)Aerospace fieldParts such as turbine blades and cabin panels are processed using five-axis milling combined with flexible tooling to achieve an accuracy of ±0.01 mm. The materials are mainly titanium alloy and Inconel 718.2)Medical equipmentOrthopedic implants are precision turned and electropolished to a surface roughness of Ra 0.1 μm. The material used is stainless steel 316L or PEEK with good biocompatibility.3)Automobile manufacturingThe gearbox housing is made of aluminum alloy 6061 high-speed milling, combined with heat treatment strengthening process, the accuracy is controlled within ±0.02 mm, and the lightweight goal is achieved at the same time.4.Challenges and solutions for machining thin-walled partsThere are many challenges in machining thin-walled parts, such as vibration and deformation, which affect machining accuracy and surface quality. To solve these problems, a series of measures can be taken, such as optimizing tool selection and tool path design, reasonably controlling cutting parameters, reducing cutting speed and feed speed, etc. The machining quality of thin-walled parts can also be improved by pre-processing the workpiece before machining and heat treatment after machining.Difficulty in clamping and deformation control1)Thin-walled parts have poor rigidity, and traditional clamps can easily cause indentations or local deformation on the clamping surface (for example, the clamping deformation of aluminum alloy parts can reach 0.1 mm).2)Special-purpose fixtures need to be frequently replaced for special-shaped parts, and the changeover takes more than 20 minutes, which is inefficient.3)Dimensional deviations due to cutting forces, residual stresses and thermal deformation during machining (scrap rate can reach 30%).4)Thin-walled parts are easily affected by cutting forces and vibrate and deform, and insufficient tool rigidity leads to poor surface roughness.5)Cutting heat causes local expansion of the material, and insufficient cooling causes dimensional fluctuations.Solution:1)Use hydraulic combination vises or modular tooling to evenly distribute clamping force at multiple points, expand processing space and improve changeover efficiency.2)Use mandrel positioning or slotted sleeve clamps to avoid radial clamping forces acting directly on thin-walled areas and reduce the risk of elliptical deformation.3)Processing in stages (rough machining → semi-finishing → finishing), combined with aging treatment to release internal stress, control the deformation within 0.03 mm.Adopt vertical clamping axial compression instead of radial compression, and use micrometer to monitor deformation in real time.4)Use a large cross-sectional toolholder and a positive-edge-angle turning tool to optimize chip removal direction and improve rigidity.Use small cutting depth (0.1-0.3 mm) + high speed (above 15,000 RPM) to reduce cutting force and thermal deformation.5)Fully pour cutting fluid and use dynamic cooling technology to control the cutting temperature within 50℃ to reduce thermal deformation.Development Trend and Prospect of Thin-wall Parts ProcessingWith the continuous development of the manufacturing industry and the advancement of technology, thin-walled parts are increasingly used in aerospace, automotive, electronics and other fields. With the continuous innovation of CNC technology, materials science and other fields, thin-walled parts processing technology will be further improved, and processing accuracy and efficiency will be further improved, providing better support and guarantee for the development of various industries.Featured Product
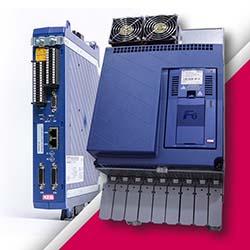
KEB VFDs for High Speed Motor Control
KEB's VFDs are the key to unlocking peak performance in your high-speed machinery. Engineered for precision control, even without feedback sensors, our F6 and S6 drives utilize advanced software and high-frequency output. This ensures smooth operation, reduced vibration, and optimal efficiency. Whether you're building turbo blowers, power generation systems, or other high-speed applications, KEB VFDs deliver the reliability and performance you need.