AFRL researchers explore automation, additive technologies for cost efficient solar power
Phys.org: Inspired by newspaper printing, and taking cues from additive manufacturing technology, researchers at the Air Force Research Laboratory are exploring new ways to make solar cells more cost efficient—increasing application potential in the process.
"Sun is abundant, and it's free," said Dr. Santanu Bag, a project scientist at the Materials and Manufacturing Directorate, AFRL. "Solar cells can generate electricity in an environmentally friendly way, but current, complex fabrication costs make the technology expensive. We're looking at new ways to use materials and manufacturing technologies to make these less expensively."
Though research into solar cells began in the 1950s, the technology for making them is complex and labor intensive. At a basic level, to fabricate solar cells, engineers rely on extremely pure, single-crystalline silicon. The pure silicon is extracted from an original material such as quartz or sand and is transformed into thin wafers. The silicon wafers are chemically treated to form an electric field, with a positive and negative polarity. These silicon semiconductors, or solar cells, are encapsulated in a support to form a photovoltaic module, where they are then able to collect and transform sunlight into an electric current.
This multistep, labor intensive process is time-consuming and uses highly sophisticated equipment, requiring a number of technicians and engineers to create the end product. Quality control is key, as a discrepancy during any stage of the manufacturing process could have an effect on the performance of the cells.
This high cost of manufacturing has prohibited widespread use of solar power, despite its cost saving potential. Full Article:
Comments (0)
This post does not have any comments. Be the first to leave a comment below.
Featured Product
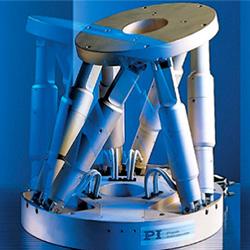