TRUMPF's ‘smart factory' is a factory and showroom in one
David Malone for Building Design & Construction: TRUMPF, a German machine tool and laser manufacturer, recently opened its new “Smart Factory” in the northwest suburbs of Chicago. The new space is both a factory and a showroom that turns high-tech machines and production processes into exhibition-like showpieces. The smart factory is fitted with digitally networked machines that present the entire sheet metal process chain as an interlinked, holistic process.
Designed by Barkow Leibinger, the new structure is divided into two volumes. The first is the showroom to the south and the second is the office and auditorium space to the north. These two volumes are connected at their corners and create two rectangular exterior zones – a driveway and parking lot to the southeast, and a curved terrace that overlooks an adjacent reflection pond to the northwest.
The building ranges from about 4.5 to 13-meters-tall and has a continuous pitched roof. At the front, the 12-meter-high glass facade presents the showroom space to passing traffic. The double glazing used has a low-E coating to protect against excessive solar radiation. The glass facades are made of anodized black aluminum and are recessed up to 1.5 meters back into the volume. Slim, recessed Corten steel I-Beams vertically divide the glass facades and support against horizontal wind loads. In addition to the glass, rust-colored corrugated Corten steel cladding was used on the exterior and charred wood siding was used on the facades of the inner courtyard and pond to achieve a softer appearance. Full Article:
Comments (0)
This post does not have any comments. Be the first to leave a comment below.
Featured Product
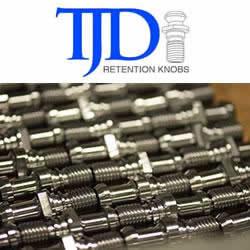