GE Awarded $9 Million from Office of Naval Research to develop framework enabling the rapid qualification and certification of 3D Printed Parts
From multi-billion- dollar assets like Navy ships at sea to cars and SUVs driving on highways and roads, imagine the day when you can visit any repair or service shop and get replacement parts on-the-spot. A team of scientists at GE Global Research, the technology development arm for GE (NYSE: GE), have been awarded a four-year, $9 million program to develop a rapid process for creating exact digital models of replacement or newly designed parts to move closer to that day.
Together with scientists and engineers from GE Aviation, GE Additive, Honeywell, Penn State, Lawrence Livermore National Laboratory (LLNL), Navy Nuclear Lab (NNL) and the National Center for Defense Manufacturing and Machining (NCDMM), the team is building digital twins from model-based data on parts and sensor-based data from 3D metal printers to dramatically speed up the qualification and certification process for replicating and printing replacement parts no longer manufactured for various naval marine and aviation assets and to create parts for newly designed assets. GE’s Digital Twins are living, learning digital models of physical assets, parts, processes and even systems. These models are continually updated as new sensor data or engineering knowledge from technical experts is integrated to reflect the exact state of its physical counterpart at any point in time.
“Using GE’s Digital Twin technology, we’re aiming to rapidly speed up the time that parts could be re-engineered or newly created using 3D printing processes,” said Ade Makinde, Principal Engineer, Additive Technologies at GE Global Research. “With today’s technology, the process for designing a new part can take years. We think we can reduce that timeframe to weeks, with the unique digital solutions under development.”
Makinde explained that it is extremely difficult to quickly make a 1:1 replacement part through 3D printing processes that was originally produced using conventional manufacturing techniques. Makinde said, “The key challenge with industrial 3D printing is being able to additively build a part that mirrors the exact material composition and properties of the original part that was formed through subtractive measures. With the kind of mission-critical equipment the Navy operates, there is no room for deviations in material performance or manufacturing error.”
Having a rapid process for producing and installing replacement parts would greatly support the U.S. Navy’s efforts to manage and maintain excellence for an aging Navy fleet. The average age of active Navy ships, for example, is ~17 years, with the oldest in service deployed in 1970. In cases where ships are several decades old, replacement parts often are no longer manufactured. This is like what car enthusiasts have experienced when rebuilding or repairing classic or older cars. Just like the automotive sector, the Navy is turning to 3D printing to get the parts they need faster.
“We’re already seeing the proliferation of 3D printing in the automotive sector, which are enabling the manufacture of outdated car parts no longer being made,” said Makinde. “When it comes to mission-critical assets like Naval ships and aircraft, the bar is higher for producing high quality parts that encounter much higher stresses and tolerances. But as one of the world’s leading aircraft engine makers that produce and maintain a fleet of 35,000+ jet engines that are in service for decades, we bring a unique understanding and depth of expertise to what kind of digital models are required.”
LLNL is bringing to the partnership its years of research and development of intelligent “feed forward” design methods in metal additive manufacturing. The Livermore method combines multi-physics modeling and simulation with state-of-the-art experimental observations to train 3D printers to predict and produce defect-free metal parts the first time, in lieu of traditional “trial and error” approaches.
“We are pleased to have the opportunity to bring our modeling and simulation methods, as well as our expertise in in-situ sensing and monitoring to this project,” said Wayne King, head of LLNL’s Accelerated Certification of Additively Manufactured Metals (ACAMM) project. “Part certification has been the focus for us all along, and we think we’ve made considerable progress and gained the confidence of our program engineers and physicists with regards to part quality. This partnership with GE is ideal because it connects us with a major U.S. vendor of metal additive manufacturing machines.”
The four- year program will occur in two two-year phases. Phase 1 will focus on the underlying software and hardware developments. In Phase 2, we will build a complete additive system that demonstrates the rapid and robust creation of a part’s digital model or digital twin and printing of that part using a 3D Direct Metal Laser Melting (DMLM) printer.
About GE Global Research
GE Global Research is the hub of technology development for all of GE's businesses. Our scientists and engineers redefine what’s possible, drive growth for our businesses, and find answers to some of the world’s toughest problems.
Visit GE Global Research on the web at www.ge.com/research. Connect with us at http://twitter.com/geresearch.
Comments (0)
This post does not have any comments. Be the first to leave a comment below.
Featured Product
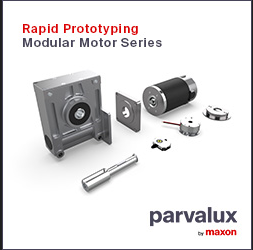