NASA to Advance Unique 3D Printed Sensor Technology
A NASA technologist is taking miniaturization to the extreme.
Mahmooda Sultana won funding to advance a potentially revolutionary, nanomaterial-based detector platform. The technology is capable of sensing everything from minute concentrations of gases and vapor, atmospheric pressure and temperature, and then transmitting that data via a wireless antenna — all from the same self-contained platform that measures just two-by-three-inches in size.
Under a $2 million technology development award, Sultana and her team at NASA’s Goddard Space Flight Center in Greenbelt, Maryland, will spend the next two years advancing the autonomous multifunctional sensor platform. If successful the technology could benefit NASA’s major science disciplines and efforts to send humans to the Moon and Mars. These tiny platforms could be deployed on planetary rovers to detect small quantities of water and methane, for example, or be used as monitoring or biological sensors to maintain astronaut health and safety.
Central to the effort, funded by NASA’s Space Technology Mission Directorate’s (STMD) Early Career Initiative (ECI) is a 3D printing system developed by Ahmed Busnina and his group at Northeastern University in Boston. The 3D printing system is like printers used to produce money or newspapers. However, instead of ink, the printer applies nanomaterials, layer-by-layer, onto a substrate to create tiny sensors. Ultimately, each is capable of detecting a different gas, pressure level or temperature.
Nanomaterials, such as carbon nanotubes, graphene, molybdenum disulfide and others, exhibit interesting physical properties. They are highly sensitive and stable at extreme conditions. They are also lightweight, hardened against radiation and require less power, making them ideal for space applications, Sultana said.
Under her partnership with Northeastern University, Sultana and her group will design the sensor platform, determining which combination of materials are best for measuring minute, parts-per-billion concentrations of water, ammonia, methane and hydrogen — all important in the search for life throughout the solar system. Using her design, Northeastern University will then use its Nanoscale Offset Printing System to apply the nanomaterials. Once printed, Sultana’s group will functionalize the individual sensors by depositing additional layers of nanoparticles to enhance their sensitivity, integrate the sensors with readout electronics, and package the entire platform.
The approach differs dramatically from how technologists currently fabricate multifunctional sensor platforms. Instead of building one sensor at a time and then integrating it to other components, 3D printing allows technicians to print a suite of sensors on one platform, dramatically simplifying the integration and packaging process.
Meet Mahmooda Sultana, Associate Branch Head, Systems Engineering Branch at NASA's Goddard Space Flight Center in Maryland. Mahmooda uses her love of math and puzzles to develop new technologies and miniaturize instruments for NASA missions.
Credits: NASA
Also innovative is Sultana’s plan to print on the same silicon wafer partial circuitry for a wireless communications system that would communicate with ground controllers, further simplifying instrument design and construction. Once printed, the sensors and wireless antenna will be packaged onto a printed circuit board that holds the electronics, a power source, and the rest of the communications circuitry.
“The beauty of our concept is that we’re able to print all sensors and partial circuity on the same substrate, which could be rigid or flexible. We eliminate a lot of the packaging and integration challenges,” Sultana said. “This is truly a multifunctional sensor platform. All my sensors are on same chip, printed one after another in layers.”
Wide-Ranging Uses
The research picks up where other NASA-funded efforts ended. Under several previous efforts funded by Goddard’s Internal Research and Development Program and STMD’s Center Innovation Fund, Sultana and her team used the same technique to manufacture and demonstrate individual sensors made of carbon nanotubes and molybdenum disulfide, among other materials. “The sensors were found to be quite sensitive, down to low parts per million. With our ECI funding, we are targeting the instrument’s sensitivity to parts per billion by improving sensor design and structure,” Sultana said.
According to her, the project addresses NASA’s need for low-power, small, lightweight, and highly sensitive sensors that can distinguish important molecules other than by measuring the masses of a molecule’s fragments, which is how many missions currently detect molecules today using mass spectrometers.
In fact, the agency has acknowledged that future sensors need to detect minute concentrations of gases and vapors in the parts per billion level. Although mass spectrometers can detect a wide spectrum of molecules — particularly useful for unknown samples — they have difficulty distinguishing between some of the important species, such as water, methane and ammonia. “It’s also difficult to reach the parts per billion or beyond level with them,” she said.
“We’re really excited about the possibilities of this technology,” Sultana said. “With our funding, we can take this technology to the next level and potentially offer NASA a new way to create customized, multifunctional sensor platforms, which I believe could open the door to all types of mission concepts and uses. The same approach we use to identify gases on a planetary body also could be used to create biological sensors that monitor astronaut health and the levels of contaminants inside spacecraft and living quarters.”
Comments (0)
This post does not have any comments. Be the first to leave a comment below.
Featured Product
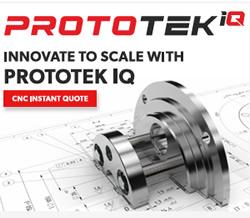