Detecting New Solutions: How Intelligent Sensors Can Support Industry 4.0
Automation continues to generate buzz in the pharmaceutical sector, impacting manufacturers’ decisions on production lines, equipment purchases, workforce development and everything in between. In the ongoing conversation around Industry 4.0 (I4.0) and data connectivity, manufacturers must develop an understanding of the technologies and steps that enable the successful implementation of automation.
To explore the impact of I4.0 and sensors in automated pharmaceutical manufacturing, we spoke with Ron Stuver, director of business consulting at SICK, Inc. (Booth LS-6419), a leading provider of manufacturing sensors. At Healthcare Packaging EXPO—co-located with PACK EXPO Las Vegas (Sept. 23-25; Las Vegas Convention Center), Stuver will deliver a presentation titled “Industry 4.0: Make it Real” on Tuesday, Sept. 24 from 11:00 a.m. to 11:30 a.m. at the North Hall Innovation Stage (Booth N-501). The session will highlight the critical role sensors play in automation and address considerations manufacturers should make when planning I4.0 initiatives.
Q: What should pharmaceutical manufacturers understand about the role of Industry 4.0 in the general shift toward automation?
Stuver: First, to dispel a myth, I4.0 is not a technology in and of itself, but rather a concept of how automation can be better utilized to help companies achieve operational goals in alignment with business strategies. While Industry 3.0 introduced computers and automated machinery to the world of manufacturing, I4.0 takes it to a new level, connecting those computers and optimizing automation for implementation.
At the foundation of I4.0 are the themes of “data” and “connectivity.” With new advancements, machines and automated systems are becoming smarter and more autonomous, and these solutions are fueled by data, machine learning and advanced analytics. In addition, the rise of the Internet of Things (IoT) has enabled a higher level of immediate information, and device connectivity than ever before.
Still, while the last four decades delivered an array of improvements to automation, islands of isolated application remain and are interspersed with manual processes that have yet to evolve. For any of the industry’s latest solutions to truly provide value for pharmaceutical manufacturers, the data created at the edge by sensors and other devices needs to be harvested, aggregated, and applied correctly in order to be utilized when and where it’s needed throughout production.
Q: What are the major drivers in this shift, and how can automation and robotics benefit pharmaceutical manufacturing?
Stuver: As with most shifts in manufacturing, the growth of automation can largely be attributed to the constant search for leaner, quicker, and more cost-effective production. Both in pharmaceutical applications and in general, robotics add value by shrinking the margin of error in the manufacturing process, which has a positive impact on quality and helps mitigate compliance risk. An example may include vision inspection solutions that automate and provide consistency in the quality check of certain products. In addition, the automation of manual processes can also influence operational efficiencies, driving increased capacity and reducing downtime.
Q: What unique challenges do pharmaceutical companies face when implementing automation?
Stuver: All companies considering automation are challenged with quantifying the value and the time frame within which an investment would be recouped. The justification to spend dollars on new technology needs to be balanced with the return, as most manufacturers face competitive pressures and may not be flush with cash that can be spent on hunches. The other “unknown” impacting some companies is the identification of appropriate applications for automation. Depending on the type of pharmaceutical product, the packaging format and the batch size, the level of automation or extent of implementation may differ. Finally, the pharmaceutical sector in particular faces stringent regulations and compliance requirements, making automation useful for consistency but also underscoring the importance of a clear understanding of the technology and methods for monitoring and troubleshooting.
Q: What technologies and steps should manufacturers consider to ease the transition? How can they determine the best path to implementation?
Stuver: With all emerging technologies and production methods, it’s critical to understand the “what” and “why” before pursuing the “how.” Too often, we try to fit products or solutions into situations where we do not yet understand the need. Before capital spends are committed and machinery added to production lines, manufacturers should take early steps to clearly discern what their goals are and why they are important to the company. After these objectives are addressed, consulting with a valued partner who will align capabilities and solutions to these priorities is key to achieving the desired value. On the workforce side, manufacturers will also need to take measures to recruit new employees or retrain existing employees to manage new machinery and production methods.
Q: What role do sensors play in data collection, and how can intelligent sensors aid manufacturers looking to ramp up automation and overall production levels?
Stuver: As the smart machines of the I4.0 era continue to evolve and the network between the machines expands, intelligent sensors promote more streamlined connectivity to information software solutions. Sensors are at the heart of the machines and devices at the edge where the data is created and can, in many cases, transmit data directly to a level where the information is needed. This transfer of information can be done in legacy environments without disrupting existing control processes, simplifying implementation of the technology.
In more complex scenarios, data collection devices can harvest data from multiple sensors, then aggregate, filter, and prepare that data to be transmitted to the level where the information can be visualized and used with historians and other analytics software platforms. This edge computing—data processing done locally, where the information is created—allows simple tasks to be completed without the need to pass data (I/O) back and forth between the sensor and other major data centers, minimizing data traffic and resulting downtime.
When it comes to equipment maintenance, utilizing sensors as micro data centers and collecting information at the edge can be beneficial in monitoring machine health. Localized information can aid manufacturers looking to pinpoint issues. Other useful data generated by sensors may include product-related information such as status of a batch process, count of product or vision inspection information that provides quality-related data. These capabilities can be instrumental to pharmaceutical manufactures implementing serialization and track-and-trace measures or seeking reassurance that products contain the proper documentation to support patient adherence.
Free 30-minute sessions at the Innovation Stage will tackle a wide range of industry topics, including automation, packaging advancements and more. Additionally, The Forum, a growing staple at PACK EXPO shows, offers free, 45-minute learning sessions on the latest industry trends, including hands-on activities, small group discussions and Q&As each day of the show.
Registration, which includes access to both PACK EXPO Las Vegas and Healthcare Packaging EXPO, is $100. For more information and to register online, visit www.hcpelasvegas.com.
Comments (0)
This post does not have any comments. Be the first to leave a comment below.
Featured Product
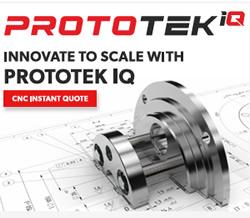