GE Additive & Kaspar Schulz Q&A - Additive Manufacturing: there’s always something brewing!
The limited-edition 3D-printed Masskrug designed and manufactured at GE Additive Munich for last year’s Oktoberfest continues to bring a smile to everyone’s face. However, this year we wanted to go a layer deeper and explore the potential that additive technology could have on the brewing and beverage industry.
Over the past six months, GE Additive’s CEC Munich team has been working with Bamberg-based Kaspar Schulz GmbH - the oldest brewing equipment manufacturer in the world.
We asked Dr Matthew Beaumont, GE Additive’s CEC Munich site leader, Dr Benedikt Roidl, advanced lead engineer at GE Additive and Jörg Binkert, head of Research & Development at Kaspar Schulz GmbH to tell us more.
Bamberg is often called the beer capital of Germany because of the high concentration of breweries there. Why did you approach Kaspar Schulz?
Matthew Beaumont: We were looking for a partner for this project who was based nearby in Bavaria. Bamberg obviously offers a lot of possibilities with the large number of brewers and other companies associated with the brewing industry. Our Concept Laser facility is just down the road in Lichtenfels, and some of our team have connections to the Bamberg brewing scene, so – pardon the pun – we were able to tap into some local knowledge
Kaspar Schulz as a company can trace its origins back the 17th century and today, the tenth generation of the same family is still at the helm. Although it is over 300 years old, it has remained a leader in its field, by remaining at forefront of innovation, adapting to new processes and technologies and then passing that innovation on to its customers.
We love working with early adopters in any industry, so the combination of a family business with a proven heritage of applying modern design, engineering and manufacturing made me think they would be great for this project.
Jörg Binkert: We were very pleased that GE Additive approached us. We were already familiar with 3D modelling and making designs with CAD, but additive manufacturing was something new for us. But once we started looking, it didn’t take us long to find a couple of good applications that could really be improved by using additive technology.
You’ve worked on two very different parts. Why did you decide to focus on those in particular?
Matthew Beaumont: Individually, the parts we worked on are great examples of two proven benefits of using additive manufacturing over traditional machining.
For the access door knob, Kaspar Schulz currently mills the part out of a block of stainless steel. This is something that we see regularly in aircraft manufacturing, but it was a surprise to see it in use here, too.
Using additive, we were able demonstrate savings in terms of material use, manufacturing time and include the possibility to customize the part with their company logo - at no additional cost or effort.
The racking blade design, however, was a chance for us to really show the freedom of design that additive allows.
At our first meeting, Mr. Binkert showed us some sketches of ideas that he had for improvements to the current racking arm for the lauter tun. His goal was to improve the filtration effect of the spent grain bed in the vessel in order to rinse it more thoroughly in order to save time and make it more efficient.
Our team was quickly able to come up with a design to efficiently loosen the spent grains and inject water, throughout the bed, during rotation. The design of a thin blade that has internal channels to distribute water evenly is only achievable using additive manufacturing.
Jörg Binkert: Now we have a real, new technology with a real, new technique. At Kaspar Schulz that’s what we call innovation - creating something what was previously not possible before.
Were there any “Aha” moments along the way?
Benedikt Roidl: Plenty! It amazing to see how many best practices the team at Kaspar Schulz has developed in the field of brewing, malting and distilling over the past 300 years.
Together with Mr. Binkert and his team, our specialists at the CEC in Munich evaluated how to improve the lautering process and we came up with the idea of dynamically loosening the spent grain using an induced swirling flow field.
As Matthew says, we used additive to incorporate built-in channels to fluidize the spent grain – that’s a nice new little feature. We’ve also been able lean on our knowledge and expertise from the aerospace and other industries to new applications and industries – in this case the brewing industry.
Jörg Binkert: The way that we have been able to change the way we introduce water, during the sparging process, is unique and without parallels. We anticipate will be able to reduce time by 30% and even improve the yield.
What about obstacles?
Matthew Beaumont: As with any new product development, time is always a challenge. We set the goal of achieving a first design in time for this year’s Oktoberfest, and we were able to do simulation analysis, complete the design, and perform basic functional tests before now.
What still lies ahead of us, though, is the final use verification in the complete brewing process. We want to verify the benefit in via chemical analysis of an actual batch of wort – and of course a taste test by the project team!
The aerospace and healthcare industries are often cited as leading the charge with additive technology, but how might additive transform the brewing and beverage industry in the short to long-term?
Matthew Beaumont: The use of additive technologies for the brewing or the beverage industry in general can have an evolutionary effect as opposed to a revolutionary effect. Functional integration, reduction of the number of joints and seals are the quick wins that additive can offer without a massive change to the machinery. Beyond that, there can be incremental improvements to individual steps in the brewing process by taking advantage of the design freedom that additive allows. The racking blade is a great first example of that potential.
Jörg Binkert: This is just the beginning!
Caption left: CAD mode of racking blade. Caption right: prototype of racking blade during testing
About GE Additive
GE Additive – part of GE (NYSE: GE) is a world leader in additive design and manufacturing, a pioneering process that has the power and potential to transform businesses. Through our integrated offering of additive experts, advanced machines and quality materials, we empower our customers to build innovative new products. Products that solve manufacturing challenges, improve business outcomes and help change the world for the better. GE Additive includes additive machine providers Concept Laser and Arcam EBM; along with additive material provider AP&C.
Comments (0)
This post does not have any comments. Be the first to leave a comment below.
Featured Product
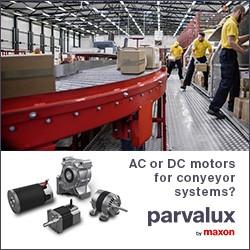