How the Model T Can Influence Your Current Industrial Automation Needs."
Henry Ford was not a newcomer to the car business when he began producing the Model T in 1908. He had already been part of several automotive companies before the Ford Motor Company was founded, and built several other car models including his Quadricycle and the 999. But he dreamed of a vehicle for ‘the great multitude,’ and so the Model T was born. Unfortunately, the original Model T was still too expensive for most Americans. When Ford began churning the cars out via assembly line, however, their price dropped significantly. In 1909, when workers were still using traditional methods to piece the cars together, a Model T was priced at $825, and less than 11,000 were produced. But in 1916, three years after Ford started using assembly line production, the Ford Motor Company produced over half a million Model Ts and sold each one for $345.
Automation can lead you to consider opportunities in ways you haven’t before. A shift in production capabilities and costs allow you to reconsider your market from a new perspective. Higher productivity and efficiency equals a lower per unit cost that will change how competitive you can be within your market.
Henry Ford significantly altered the lives of his workers. At the beginning of assembly-line production within the Ford Motor Co, most workers managed 9-hour days for about $12 a week. But the shift was awkward, the work was hard, and turnover was high. So Ford changed the work periods to three 8-hour shifts and doubled the worker pay through a bonus structure. This, in turn, decreased his labor turnover and allowed for smooth, uninterrupted production of his cars.
Despite fears, current technology does not take away jobs. In fact, automation may help increase the number of skilled, high-paying jobs within the manufacturing sector, since an automated shop has need of better trained, higher skilled workers. This can be a win-win for an existing company as well as their current workforce if management offers educational reimbursement to employees who want to retrain to gain more skills: your employees gain 21st century skills that can allow them to remain with the company in a better-paid position, and you retain good employees who have a proven track record of reliability.
One of the primary advantages to Henry Ford’s assembly line was its increased efficiency. The Model T went through 84 individual assembly processes using interchangeable parts that were all mass-produced elsewhere and assembled into a single car by workers trained to do one particular job. While this seems like common sense today, it was a revolutionary idea in 1913, and one that increased worker productivity to such a level that the time to put a single Model T together dropped from over 12 hours in 1908 to 93 minutes in 1914.
Automation can make the same kinds of leaps in efficiency for your company. When Factory Five Racing, Inc was looking to decrease the time it took to produce their hot rod trim kits, they turned to robotic automation. The change allowed them to produce a higher quality trim kit consisting of four sets of panels (four trunks, four hoods, and eight doors) in 24 minutes, down from 7.5 hours.
Increased efficiency tends to improve throughput, reduces environmental impact due to lower energy use, and cuts costs.
Henry Ford famously said, “Any customer can have a car painted any color that he wants so long as it is black.” While this doesn’t imply a flexible business outlook, Ford’s assembly line was remarkable in its flexibility. At the height of Model T production, there were eleven different bodies built upon the basic Model T chassis, including a racer, a snowmobile, a police wagon, and a woody wagon, and each one could be custom-fitted with any of thousands of accessories.
Flexible automation allows your plant to switch over to take on new processes without a full retrofit. This is made easier by thinking ahead about what challenges might occur down the road and preparing for them during the initial design phase. For example, choosing robots with an open interface will allow for the later connection of third-party equipment for customized processes. This is where working with an experienced robotics/AI design firm can pay significant dividends later.
Another famous saying is “The more things change, the more they stay the same.” While Henry Ford’s assembly line and basic business practices have long been replaced by modern lean manufacturing and Industry 4.0, we can still apply Ford’s reasons for improving processes to today’s changing industrial landscape.
Comments (0)
This post does not have any comments. Be the first to leave a comment below.
Featured Product
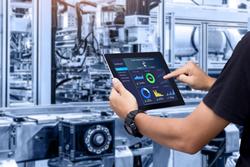