The complexity of mineral processing and manufacturing plants — how Artificial Intelligence can help
Each and every plant has a unique way of operating. From hundreds of control parameters, to the volume of production materials processed and the measured outputs, there is a huge amount of data available. Pre Industry 4.0 plants are hampered by their inability to capitalize upon this valuable resource, often resulting in poor operational performance and quality metrics.
Industry 4.0 encapsulates not only manufacturing but also mineral processing plants and the differences between these should be considered carefully in the deployment of 4.0 solutions such as Artificial Intelligence (AI).
Three key comparisons between mineral processing and manufacturing plants:
1. Tolerance levels: Manufacturing and mineral processing plants are similar in that they often consist of a series of unit operations, each designed to achieve a certain output. It can, however, be argued that the tolerances demanded at the battery limits within manufacturing plants are tighter and in light of this, manufacturers have been applying Statistical Process Control (SPC) to monitor and control their processes since the 1920s.
2. Volume and scale: Mineral processing plants are significantly different in terms of the volume of material they process and their scale is typically not comparable to the average manufacturing process.
3. Complexity: Even though the mineral processing volumes are huge, this should not be mistaken for a lack of complexity in comparison to manufacturing plants. A mineral processing circuit may consist of multiphase mass transfer, hydrometallurgical and thermal processes; these are often open to the elements and coupled to a variable and evolving feed.
These challenges— tight specifications in manufacturing plants and high volume, complex circuits in mineral processing plants are all managed to varying degrees through process control. Despite the control systems in place, operators in both environments continue to make daily and hourly changes to their area of the plant despite the immense complexity of the system as a whole. Often an innately human combination of experience, and gut-feel, guide the operators in their decisions when an understanding of the intricate and complex interdependencies of the process can’t be processed by them, or the metallurgist and engineers, in real time.
The data challenge is real
It could be said that day-to-day plant operations are an extension of the design experiments which occurred during the design and commissioning phases. What if the learning from the daily changes made by the operators could be captured, similarly to design experiments, and used to inform the decision-making process going forward?
The reality is often that this data is captured in a variety of ways in both digital and non-digital formats. These range from the logbook recordings of the gap on the crusher to the assays stored in the laboratory information management system and the real-time, online measurements from weightometers and flow meters to name a few.
Taking advantage of Artificial Intelligence in Industry 4.0
The use of AI across mineral processing and manufacturing plants is growing significantly. Plant operators and innovation leaders are partnering with engineers and data scientists to extract value from historical data to optimize manufacturing and mineral processing plants.
This begins by unifying often disparate sources of data to provide operators and engineers alike with a unified view of production and quality data for the product, often for the first time in the history of the plant.
Through machine learning and analysis of the data, AI technology creates a learnt digital twin of the plant and is able to inductively discover the entire process from hundreds of man-years’ worth of institutional knowledge embedded in the data.
In this practical application of AI and machine learning, the optimum operating patterns are identified from the historical data and used to prescribe actions based on the current operating characteristics of the plant. These prescriptions are provided within the context of a systemwide view which is cognizant of upstream and downstream processes. AI technology is able to prescribe parameter settings to operators before the fluctuations in the process flow reach their areas of responsibility, ensuring the optimum parameter settings across the plant.
The result is a material reduction in variation and improved plant metrics such as product grade and recovery and therefore a significant increase in profitability.
About DataProphet
DataProphet is a global leader in Artificial Intelligence (AI) for manufacturing. Our award winning technology embeds unique adaptations and advancements of deep learning, enabling AI to have a significant, practical, impact on the factory floor. DataProphet’s solutions are built to be adapted and integrated into existing environments, making it possible for our digital transformation team to take your operations from zero to AI. We understand manufacturing and that real impact is achieved with pre-emptive actions because real-time is often too late.. For more information, visit www.dataprophet.com
Contributed by Gareth Halstead, Mineral Processing SME, DataProphet
Comments (0)
This post does not have any comments. Be the first to leave a comment below.
Featured Product
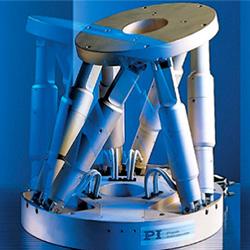