What is Cast Urethane Manufacturing?
Stated by urethane manufacturers, this process starts with a model that is made through CNC machines, polyjets, or other technology. The master is then used to make a rubber mold. Silicone is often used instead of rubber because of its durability and tolerances. Once the mold is made, it has to set.
Then, the mold is used to make the cast urethane that is made of liquid pre-polymers and curatives. They have to be specifically mixed in a timely manner. When the chemicals are mixed, they have to be used within a set amount of time so the liquid can properly turn to a solid. During the set time, colors are added if the manufacturer requires them.
Eventually, the part solidifies and manufacturers use controlled steps to enhance its mechanical properties. The part might be quickly removed from the mold, or it might have to sit in the mold for several hours so it can set properly.
Molds can be used to make cast urethane parts that measure as small as a one-inch cube, to a part the size of a small refrigerator. Cast urethane is highly versatile, which is why so many manufacturers are turning to it.
Why Use Cast Urethane?
The material has several benefits that make manufacturers eventually turn to it. Urethane parts use polymers that have strong yields and serious stability. Many shops often have their own steps in making cast urethane parts, because they have been around for so long. But, they also look at ways to make the process more efficient.
Urethane parts can be made with extreme accuracy, so they can be used in final products and as tools in the different stages of production. Their mechanical and physical properties make them highly desirable in several facets of manufacturing. Castings are strong and stable. Many are also flame-resistant and they withstand impact tests with ease, too.
Cast urethane is practical for manufacturers. They are less expensive than tools made from metal, so manufacturers and customers who do not need a part for large-scale production can save money on a cast part. Then, if the part is only needed for the short term, it might be recyclable in another way. Metal parts do not have that same practicality and recyclability.
Where is Cast Urethane Used?
The market for cast urethane products is growing. As the technology and the materials have advanced, manufacturers are looking at more pieces made from cast urethane. They are quick to get in the market and easy to manufacture. Popular industries that are turning to cast urethane include
- Aerospace
- Automotive
- Medical
These industries appreciate cast urethane parts because they meet engineering requirements. They also go to production faster than those made from metal tool manufacturing. When you need a product to get to the marketplace faster, you turn to cast urethane. This increases the bottom line for these vital industries and for the others that use cast urethane, too.
Another important reason that those industries use cast urethane manufacturing is the speed of turnaround times. For example, every time there is a subtle change to an automobile, new tools are needed to be made to design those parts. It is easy to make a new model and cast new urethane parts. It is significantly faster than doing that with metal tool-and-die processes.
How Does Cast Urethane Solve Manufacturing Problems?
All industries suffer from different types of problems. In manufacturing, customers often neglect projects or put them off for later dates because they are expensive. Producing new tools for any project is expensive, especially when overseas production is involved. With urethane cast manufacturing, the cost to make a model is minimal. And they can be made quickly, so products do not have to be put on hold. Growing the bottom line is important in a business, and cast urethane can help get business done at a low cost.
When you turn to cast urethane manufacturing, you need to work closely with customers. It is also important to keep a close eye on the processes used to make them cast faster. Those include processes that require heat and pressure as well as vacuum and time.
Another problem that cast urethane manufacturing solves is the annual redesign. Cast urethane can be changed quickly, so competitors who use cast urethane can deliver faster than a traditional tool and die maker can. Urethane is inexpensive, especially when compared to the materials used for traditional tool manufacturing.
Why Turn to Cast Urethane Manufacturing?
The business is booming for cast urethane manufacturing. Engineers and designers specialize in creating prototypes, which manufacturers often turn to produce parts from those cast models. Cast urethane is affordable and environmentally friendly, making it a useful product for manufacturers to embrace.
Comments (0)
This post does not have any comments. Be the first to leave a comment below.
Featured Product
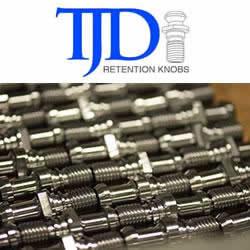