Debunking Concerns About the Use of Abrasive Finishing Tools in CNC Applications
With new advances in abrasive technology, machining center operators are able to complete surface finishing simultaneously with other machining operations, to speed cycle times, improve quality and save on off-line finishing time and costs. As a result, contract machine shops are increasingly turning to abrasive finishing tools that can be easily integrated into CNC machines carousels or tool holding systems.
However, in doing so, questions inevitably arise about the use of abrasive materials in expensive CNC machining centers. The concern is often a generalized impression that “abrasives” – like sandpaper – release large amounts of grit and debris that could clog coolant lines or damage exposed slides or bearings.
“These are very expensive, very accurate machines,” says Janos Garaczi, president of Delta Machine Company, LLC, a machine shop specializing in complex, tight tolerance parts made of titanium, nickel alloys, stainless steel, aluminum, plastics and other exotic alloys. “I wouldn’t do anything to jeopardize the accuracy or lifespan of the equipment.”
Fortunately, a closer examination of abrasive tools demonstrates that these concerns are largely unfounded. Although “abrasives” are often all lumped into the same category, a distinction must be made between abrasives used for aggressive material removal and abrasive finishing tools. Finishing tools release little to no abrasive grit during use, and the amount generated is comparable to the metal chips, grinding dust and tool abrasion created during the machining process itself.
Even if minimal fine solids are produced, the filtration requirements for abrasive tools are not much different than for machining. Any particulate can be easily removed using inexpensive bag or cartridge filtration systems, according to Jeff Brooks of Filtra Systems, a company specializing in industrial filtration systems including for CNC coolant.
“A disposable media vacuum filter or pressure filter is the most cost-effective option for the end user for filtration that will achieve the high clarity levels required,” explains Brooks.
“For fine honing work, I would recommend a 20-micron bag or cartridge filter at minimum to catch any fine solids and adequately protect the tool, the sump pump and keep the coolant ports from clogging,” says Chris Erato, Director of Sales at Oberlin Filter, another leading manufacturer of separation filtration for CNC coolant systems.
For CNC operators interested in a fully automated pressure filtration systems, there are units that eliminate the need to remove bags or clean magnetic separators that maximize production uptime.
Case Studies from the CNC Shop Floor
According to Tim Urano, Quality Manager at Wolfram Manufacturing, any additional cost for filtration related to the use of abrasive tools is so negligible it is “not really a consideration because filtration systems are already required to remove particulate from the coolant generated during the machining process itself.”
At his shop, that includes scale, grit and rust created by cutting through raw stock. Wolfram Manufacturing is also machining more 3D parts made of Inconel, which can release fine metal powder into the coolant that isn’t fully sintered.
As for abrasive tools, Urano says Wolfram Manufacturing has, “never ever experienced any problems caused by abrasives in our cutting fluids.”
For the past eight years, the machine shop has incorporated the Flex-Hone in all CNC machines for cross-hole deburring and surface finishing. The Flex-Hone from Los Angeles-based Brush Research Manufacturing (BRM). Characterized by the small, abrasive globules that are permanently mounted to flexible filaments, the product is a flexible, low cost tool utilized for sophisticated surfacing, deburring and edge-blending.
Removal of burrs and sharp edges in cross-drilled holes and other difficult-to-access areas such as undercuts, grooves, slots, or internal holes is critical. Failing to remove burrs can cause blockages or create turbulence in the flow of fluids, lubricants and gases through critical passages.
“On a given part, we might deploy two to three different size Flex-Hones, depending on the number of cross port intersections and different hole sizes,” explains Urano.
The Flex-Hones are added to the tool carousel and are used daily, usually several times an hour, on some of the shop’s highest volume parts.
“The volume of abrasives that could even possibly come off of the Flex-Hone is insignificant compared to the rest of the particulate that gets into the coolant,” explains Urano.
At Delta Machine in Gardena, Calif., automated crosshole deburring is also integrated into the CNC machining process.
“When you use the Flex-Hone for deburring, all you are doing is removing the burr. It doesn’t create much dust,” adds Delta Machine’s Garaczi. “So, for me, any grit or dust released is zero concern. It is not like we are grinding inside the machine with powder everywhere – this is not the same at all.”
Abrasive Nylon Filaments
For Eric Sun, founder of Orange Vise Company in Orange County, Calif., even cutting tools such as carbide drills and end mills can create debris that must be filtered from the coolant.
“Some machine shops might say, ‘I don’t use any abrasives in my process; therefore, my machine is completely free of all particulate matter,’ but that is not the case. Even cutting tools can wear down and the carbide can come loose and get into the coolant,” says Sun.
Although Orange Vise is a contract manufacturer, the company primarily machines vises and quick-change fixturing components used in CNC machines out of aluminum, steel and cast iron. The company utilizes four Mori Seiki NHX4000 high speed horizontal machining centers and two vertical machining centers.
According to Sun, many of the vises are made of cast iron with selectively hardened surfaces. To match the surface finish of the hardened surfaces, Orange Vise uses NamPower abrasive disc brushes from Brush Research.
Composed of flexible abrasive nylon filaments bonded to a fiber reinforced thermoplastic base, the NamPower abrasive disc brushes contain a unique combination of both ceramic and silicon carbide abrasive. The abrasive filaments work like flexible files, conforming to part contours, wiping and filing across part edges and surfaces to deliver maximum burr removal rates along with an ideal surface finish. Other common uses are edge blending, part cleaning, and rust removal.
To complete the surface finishing operation, abrasive nylon brushes are installed in the tool loading system of each CNC machine. Although abrasive grit is involved, Sun says the NamPower brush is a “different type of abrasive” because it is essentially “self-sharpening.” Because of its linear construction, sharp new grains constantly come in contact with the work surface and wear off exposing fresh cutting particles.
“We have used the NamPower abrasive nylon brushes daily for six years. During that time, we have had no issues with any sort of particulate or grit getting into any critical surfaces,” adds Sun. “In our experience, any small amount of grit created is a non-issue.”
Comments (0)
This post does not have any comments. Be the first to leave a comment below.
Featured Product
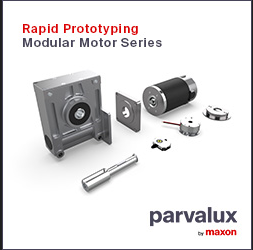