3D Printing Trends 2021: A Year of Radical Renewal
As we mark our entry into the 4th decade of 3D printing in 2021, we also enter a decade with the potential for radical renewal. The COVID-19 crisis has had an enormous effect on every industry and continues to propel us into a space where we need to think differently. To think about where we need to push the boundaries of innovation and creativity.
With this being said, the legacy of 3D printing starts in 2021 with three key trends: going back to the drawing board to rethink manufacturing; enabling the personalization of not only products, but also 3D printers themselves; and creating new solutions, fast.
This is not the first time the world has seen this opportunity for change. Apple introduced the iPod right when the dotcom bubble burst. Airbnb came to life during the financial crisis of 2008, and Alibaba launched its online marketplace at the height of the SARS epidemic in 2003.
“In this time of great flux, we must dare to take bold steps and discard what is not future-proof. We need to harness the core values of technologies like additive manufacturing (AM) to move towards new ways of thinking and doing that have meaningful impact,” says Fried Vancraen, Materialise CEO and Founder.
We believe that additive manufacturing is meaningful when it empowers people to make better choices. The COVID-19 crisis has shown that AM can step up and provide meaningful solutions to emerging challenges. But so far, these solutions have not truly played to the strengths of the technology. The value of AM lies in being able to create things that no other manufacturing method can.
AM’s ability to customize, to print with fewer components and with less waste, means that it can ensure solutions that are socially inclusive and that operate with sustainability at their core. The key to a strong legacy for our industry is to continue finding meaningful applications that take advantage of these qualities and to bring a greater awareness to all that AM has to offer.
In the short-term, we are still locked into the COVID crisis, but the trends we foresee in the coming year look to successfully take us to the other side of this stronger and more flexible, and ready for possibilities where 3D-printed products or components bring more value.
Let’s not forget that this value is often created at the beginning of the chain, in the digital capturing of the essential customer data and requirements. At the end of the chain, the 3D printing packages this value into a product. Let’s rethink value chains as Apple, Airbnb or Alibaba did.
As Fried put it, “As companies realize that they need to do things differently, AM empowers them to make a difference. And in this way the legacy of AM will not be what it allows us to make, but what it makes possible.”
1. Back to the Drawing Board
Everywhere around us, the COVID-19 crisis is turbo-boosting digitization. At the same time, the climate crisis continues to press upon us a sense of urgency to reconsider the status quo of our economic and industrial systems. The continued emergence of such extreme crises means that we can no longer continue the way things have been going. We need to dramatically rethink the way industries operate and how we develop solutions to new challenges.
The pressures of these types of existential threats demand more than just incremental steps forward. Incremental processes of innovation also leave little room for revolutionary technologies like AM to make an impact. But by allowing ourselves to completely rethink how we approach solutions, we open the door to radical new designs and innovative processes, something AM is naturally designed to do.
Take Airbus, for example. They recently revealed plans to accelerate the development of hydrogen-powered commercial jets and skip over the development of hybrid engines entirely. This bold jump means that by 2035, the world could see the first zero-emission, climate-neutral aircraft. Technologies like AM can play a big part in realizing these types of innovative concepts.
More than anything that came before, global crises are incentivizing industries to fast-track their technological innovation, and this climate of radical reinvention represents an opportunity for AM to really become instrumental in the areas of design and manufacturing.
According to Materialise CTO Bart Van der Schueren: “AM frees designers from the constraints and limitations of traditional manufacturing technologies, helping them to focus on the solution instead of the product. As a result, AM allows us to create performance, weight-saving, time and cost advantages. Until now, AM has really only been able to demonstrate its potential. Now it gets the chance to actually do it.”
Starting fresh doesn’t mean starting from nothing. By going back to the drawing board, we create freedom to give new technologies a chance. To unleash new perspectives and possibilities. Then, the only limit to the change we can create, is our imagination.
2. Personalizing the Process
“It is generally known and accepted that a unique and distinguishing characteristic of 3D printing is that it significantly reduces the cost of customization of products. What is less known and often overlooked is the importance of empowering engineers and operators to also personalize and optimize the printing process as such,” says Materialise’s Executive Chairman, Peter Leys.
Why is customization of the process so important? Is the ideal AM world not a world where the operator simply pushes the start button and then prints whatever product that needs to be printed based on a pre-installed set of parameters that comes with the machine?
Well, the illusion of a world where one standard printing process fits all applications is wrong, short-sighted and, last but not least, dangerously boring.
First, it is wrong because 3D printing is such a flexible technology that its potential would by definition be under-used if only a few standard processes would be deployed regardless of the product that is being manufactured. If you want to use additive manufacturing to its fullest extent, then you have to tweak each and every parameter of the machine and the process to the specific product that you intend to print. In a prototyping context, this possibility and need was less crucial as the efforts to adapt the process to a particular product could only be depreciated over, at best, a very small batch of products. As AM is more and more used for mass production, the need to come up with the most optimal process for a particular product obviously becomes more and more relevant.
Second, the one-process-fits-all-products philosophy is short-sighted, because it completely overlooks the fact that personalization and localization go hand-in-hand. Or to put it differently: 3D printers can only be deployed in a distributed manufacturing setting, if the local operators have the freedom and ability to adjust the process to their local reality. Typically, the primary parameters would be set centrally and then more specific secondary parameters would be adjusted by the engineers in their respective locations to meet their local needs.
Finally, a world where an operator cannot contribute the added value of their knowledge and expertise to the printing process would be a dull push-the-start-button world. The world of standard processes would not only be boring; it would also be dangerous, because it would be a world with less competition as 3D printing facilities would not be able to distinguish themselves from other operators by adding their personal expertise and experience to the process. And lack of competition means, at the end of the day, lack of innovation.
So, the more operators are empowered to fine-tune, optimize and personalize the 3D printing process, the more the value of 3D printing will be unleashed. Yes, 3D printing should become faster, cheaper and more reliable. But to get there, 3D printing should also, and foremost, become more and more personal.
3. No Time to Waste
Materialise Vice President for Medical, Brigitte de Vet says, “COVID-19 has launched the world into a state of constant urgency. Healthcare professionals as well as regular consumers have been confronted with shortages and quality issues for both essential medical products and everyday consumer goods, a consequence of a global market model that hinges on centralized, mass-manufacturing. Things we used to take for granted are no longer necessarily available or even appropriate, and new solutions need to be developed fast.”
Digitization is accelerating in every area as companies are investing in technologies that can help them adapt to this new normal of filling supply gaps, remote work and local solutions. But as part of this adoption, they need to make choices, and they will choose based on risk, cost and quick return on investment (ROI).
AM is one of those digital technologies that can deliver short-term ROI, low-cost manufacturing, and low risk, but the entry point has typically come with a lengthy learning curve. Some companies started the AM adoption process ten years ago and are well-positioned to make greater shifts to the technology, but companies new to AM no longer have the luxury of time.
Brigitte continues, “As a result, we see a growing trend for services that guide companies along this path. We see this for example in the medical world, where the value of personalized medicine is well known, but there is a low tolerance for uncertainty. New solutions need to offer strong evidence that they are safe and effective and can deliver a high-quality standard of care. Consultancy services can help minimize the risk of such big investments and accelerate the timelines by sharing their expert knowledge of what the technology can and can’t do, and the right manufacturing method needed for each unique case.”
Comments (0)
This post does not have any comments. Be the first to leave a comment below.
Featured Product
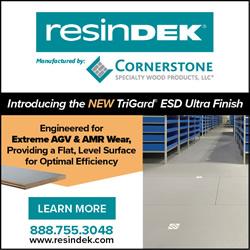