When Digital Transformation’s “Check Engine” Light Comes On
It’s an all too familiar situation: you take your car in for an oil change, but the mechanic pushes you a list of your car’s ailments that you aren’t interested in addressing right now. Instead of solving one simple problem like replacing the oil, you find yourself trying to decide if you need to address your mechanic’s concerns: new fluids, air filters, or tires. Setting off with the ubiquitous goal of “fixing your car” has a way of uncovering more problems. In doing so, you end up uncovering more costs. The same situation often rises when companies embark on company-wide digital transformation.
A New Solution to an Old Problem
When CIOs are charged with digital transformation, it’s often not as smooth a process as expected. Our newest report found that 78% of industrial professionals encountered underlying issues when they began implementing digital transformation. These issues can be costly and often slow the entire process down. The company’s “check engine” light comes on and there’s a long list of expensive issues that need to be addressed.
With so many digital transformation efforts landing companies in the shop, it is becoming clearer that the traditional method of a total overhaul of digitization is not necessarily the best one. New data suggests that a more precise approach of digitizing one specific workflow with one specific solution could be more effective. With Operation-Specific (Op-Specific) Digital Transformation, CIOs and their employees can implement a program to digitize one specific workflow. This means fewer hurdles along with less time and money.
The Setbacks and High Costs of Digital Transformation
The most obvious agent of change toward digital transformation has been the COVID-19 pandemic. Many companies had to compress years’ worth of automation-related work into weeks, and 84% of industrial professionals said that COVID expedited their need to digitize their workflows. This need for hyper-digitization not only exposed workflows that were difficult or impossible to perform remotely, but also revealed those unexpected underlying issues.
More than half (57%) of the respondents said that the unexpected issues that came out of the total overhaul method slowed down their digital transformation efforts. Change can’t move forward when there are problems to be fixed. Slowed digitization can defeat the entire point of digitization, resulting in slowing the work process itself.
Many also reported that the legacy approach resulted in higher costs. 44% of the respondents said that unexpected issues added to the cost of their digital transformation efforts. A huge overhaul is more likely to accrue costs than a targeted, measured approach. The additional costs can come in the form of new software, equipment, or labor.
Small-Scale Change for Lasting Impact
By nature, Op-Specific Digital Transformation is cheaper and less likely to uncover issues. More than half of the respondents said that they’ve already explored op-specific digital transformation. Of those, 79% said that it was effective. That is a strong testament compared to the 25% that believe the all-or-nothing approach is the best implementation method.
Small-scale change allows you to change the oil without worrying about the costs that come with your mechanic’s “nice to have” list of repairs with the “check engine” light. When tackling digital transformation, engaging a single tool to fix one problem is a more robust approach. Instead of gambling on a top-down approach, embracing op-specific digital transformation can help you automate the processes that actually need to be automated. Read the entire report on this new approach to digital transformation here.
Comments (0)
This post does not have any comments. Be the first to leave a comment below.
Featured Product
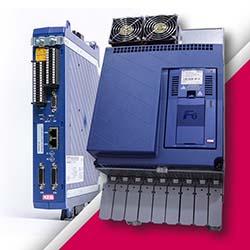