Shutdown and Turnaround: A 7-point plan
Shutdowns are a big deal. From planned inspections to the inevitable unexpected repairs that’ll crop up, without impeccable planning and controls the scenario can easily escalate into a logistical nightmare. And that’s before we get into the aspects of income loss for every day a facility is out of action.
The following details the essential 7 elements to a successful turnaround.
Planning, planning, planning
This is, quite simply, the most important phase and is the baseline from which the success of the operation will grow. Allowing enough time to get all the planning in place is essential – in fact, as soon as one turnaround finishes then the strategy for the next should begin. Details of the following should be included:
- All previous inspection and maintenance data
- Inspections to be performed
- Known maintenance to be carried out
- Equipment logistics, such as those that needs to be repaired, replaced or removed
- What expertise will be needed
- Equipment and tools required
- Budget
- Action plan for unexpected works (both best-case and worst-case scenarios)
Set up a Comms plan
If communication falls down then you’re guaranteed of unnecessary delays. One common failure is a poor understanding of how clients, contractors and subcontractors interact. The key here is to embrace technology, using database software, apps and cloud solutions so everyone involved can instantly share and access data.
Utilize historical data
This information is invaluable, as it provides a constant against which it’s possible to understand costs, man hours and local irregularities. Should there be little existing data, it’s still possible to make accurate estimates using the following:
- The initial known maintenance and repairs to carried out
- Man hours necessary to complete this
- Costs of local and expert labour (as a rough guide, manpower represents somewhere in the region of 30% of the complete turnaround costs)
Create the project plan
Once all of the above information has been gathered, a detailed project plan can be put together. Naturally, this must incorporate all the known inspections and tasks to be carried out, with a margin of error to cover unexpected repairs that are almost guaranteed to come to light. Include in-depth budget planning, such as costs for necessary equipment, all contractor and sub-contractor expenses, as well as the lost revenue while the facility is offline.
It’s vital to approach this with a total budget approach. In other words, to consider the total lifecycle of the asset, as opposed to managing each phase as a stand-alone procedure. While this might mean a more expensive investment is needed, overall this will lead to a more cost-effective solution over the lifetime of the plant.
Use experienced consultants and apply meticulous scope management
While it can be tempting to include maintenance elements in a turnaround that might not be strictly necessary, it’s crucial to ensure that only those that are absolutely essential make the final cut. Get input from all relative departments. Indeed, utilising highly experienced turnaround consultants is money well spent. When assessing what tasks are included within the turnaround period, consider if any could be performed outside of this window. If so, then they should be re-assigned to an alternative time.
Put performance indicators in place
Having an independent overview throughout the whole turnaround process is a wise move. This means warnings will be raised at the earliest opportunity should work not be going to plan. KPIs are an effective method to manage performance and allow for the making of timely decisions.
Take full advantage of technology
The huge leaps in industry-specific technology over the last decade has led to many solutions to streamline and lower the costs of a turnaround. From apps to share data, software tools to help schedule work and progress, through to accurate robotic inspection tools and programmes that reduce reams of paperwork, tech provides a robust way to speed up processes and reduce costs.
The digital era is no longer the stuff of science fiction – it’s the here and now. Facility management that fails to embrace such assets is already at a disadvantage. Turnarounds are historically a challenge, but utilising cutting-edge apparatus makes for highly effective solutions.
Whether it be the oil & gas industry, petrochemical, mining or any other large-scale operative, effective turnaround is best approached in collaboration with an equipment provider with an intimate knowledge of the latest on the market. Perth-based Nexxis not only offers just this, but a unique flexible procurement model that’s as bespoke as a facility’s needs.
Find out more at www.nexxis.com
Comments (0)
This post does not have any comments. Be the first to leave a comment below.
Featured Product
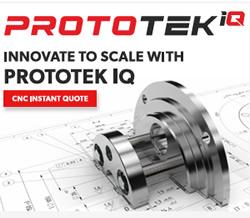