How to harness the power of data through IoT solutions for manufacturing
As we all know, the manufacturing sector was hit incredibly hard in the last year when the pandemic caused countless disruptions and an 11-year low in both employment and new orders. However, this isn’t the first or the last time disruptions will occur in the supply chain, and manufacturers equipped with the right technology to manage those disruptions will be able to minimize the impact of disruptions on the supply chain and come out on top.
More specifically, IoT solutions have been helping manufacturers for years to streamline operations, cut costs and gain otherwise unfounded insights, and their importance is emphasized now more than ever as factories, plants and warehouses adjust to operating under new guidelines coming out of the pandemic and are looking to play catch up.
Here are some ways manufacturers can harness the power of data through IoT insights:
Facility-Wide Real-Time Insights
At a high-level view, the IoT allows manufacturers to keep track of facility-wide metrics in real time and remotely monitor tank levels, consumption data, backup power sources and more. IoT devices are easily paired with existing machinery and are quickly up and running, offering an affordable option for tracking and insights.
For example, IoT connected sensors can monitor pressure, vibration, temperature, humidity, switches and voltage in a facility. This information can be used to detect leaks in tanks or high-pressure pipes that have the potential to burst, cause major environmental damage and put employees and the public in danger, in addition to the monetary losses that would occur for the manufacturer. The sensors’ constant monitoring can be used as a preventative method, alerting manufacturers of an issue, like the need to check on a pipe experiencing pressure levels that are too high. Armed with that data, manufacturers can catch and correct these problems before they become catastrophic.
Tracking the Supply Chain
It’s also crucial for manufacturers that are managing assets to be able to track and trace them within their supply chain to save time and money from within their warehouses or during shipping globally. For example, the recent Suez Canal blockage is just one instance that emphasizes how vulnerable our global supply chains really are and the importance of solutions that can predict and manage these fragile supply chains. Manufacturers that leverage an IoT network and a cloud-based tracking solution receive regular communication from the IoT devices about their items’ location and will receive an alert when there are unexpected movements. The devices utilize GPS, Wi-Fi positioning and Bluetooth beacons to track assets with high precision. Bluetooth beacons can also be used in a warehouse to provide insights into the positions of assets within the warehouse, eliminating time wasted on searching or the potential for misplaced assets.
For example, in the food and beverage industry, real-time transparency helps manufacturers optimize their supply chains. Monitoring for food and beverage silos powered by the IoT can simplify inventory and order management processes and to help the manufacturers and suppliers of raw materials improve their silo replenishment processes. When these goals are achieved, manufacturers can save costs and reduce their environmental impact through route optimization. Digitized IoT solutions can monitor silo fill levels through sensor and cloud connectivity technology on wireless networks and send alerts when the silos need to be replenished, automating that step in the process. These solutions require no maintenance or external power supply for years, giving a quick return on investment and a reliable solution that doesn’t require regular checkups.
Maintaining Business Continuity
Last spring, the COVID-19 pandemic forced companies across the country and world to suspend operations, and operations still have not made a complete return to normal in most places. While there is a light at the end of the tunnel, there is a valid fear of another shutdown and the chance for more disruption. While manufacturers are navigating a reopening, and setting up contingency plans for the future, the IoT can be collecting helpful data to inform decisions about workers’ safety and plant operations.
After making it through a pandemic, manufacturers cannot afford to be dealing with leaks or broken machinery that slow down production. Fortunately, the IoT is an incredibly helpful tool to minimize disruptions and save money in the journey forward.
Comments (0)
This post does not have any comments. Be the first to leave a comment below.
Featured Product
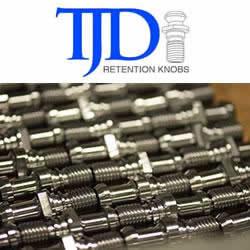