The Use of 3D Printing and Autonomous Equipment in Construction
There are a lot of applications of 3D technology in various fields. One of the most promising ones is the use of autonomous equipment and 3D printing in construction. Read on to learn more about the use of these technologies in the construction industry and how they can develop in the coming years.
What Is 3D Printing in Construction?
As a concept, 3D printing is far from new. The origins of 3D printing date as far back as the '80s. However, it wasn't until recently that 3D printing has become mainstream. The technology improved over the years and the cost of 3D printing declined, ushering in the era of their practical use.
Many fields, such as medicine and dentistry, started exploring what this technology is truly capable of. Construction companies followed suit and started incorporating 3D printing as well. There are two main ways construction can benefit from 3D printing.
Firstly, a 3D printer can build a construction project on-site. In that case, the printer is attached to a construction arm. It prints the full project, so the use of manpower, in this case, is minimal.
Secondly, a construction company may use a 3D printer to create certain components they need for a project. Here, the printer stays in a factory, where it makes the necessary parts of a construction project. The construction workers then assemble said parts on-site, so a certain amount of labor is still necessary.
As of 2021, combining 3D printing and construction is still quite rare. There aren't a lot of 3D-printed houses and buildings you can point to. However, the future of autonomous construction looks promising.
The Benefits of 3D Printing in Construction
Although the use of 3D printing in construction isn't common, it has proven to be quite beneficial. Because of its many uses, construction companies are ready to invest in this technology. Here are the main benefits of the use of 3D printing and autonomous technologies in construction:
Fewer Injury Risks
Construction work can be quite dangerous. The workers have to carry heavy materials and operate dangerous equipment, which can lead to serious injuries. That's where autonomous construction equipment can be of great help.
Essentially, automated machines are less susceptible to error than humans are. Most accidents happen because a person is tired or can't focus on the task at hand. However, a machine can't get tired, which leads to overall improved safety.
Fewer Material Costs and Less Waste
The construction industry is responsible for about 1 billion tons of waste per year. Although you can try to get just enough material, you'll likely end up with an excess. Since you never know the exact amount of material you'll need, it's necessary to buy more than you'll end up using.
However, if you use 3D printing during the manufacturing process, you will use the exact amount of materials you'll actually need. Therefore, you'll reduce unnecessary waste, and you can even make your construction process completely zero-waste. Additionally, you'll end up saving money you would've spent on the excess materials.
A Cheaper and Quicker Construction
Autonomous construction equipment can mostly run on its own. Therefore, you'll have to hire fewer workers for a particular job. Since you will be paying fewer salaries, the whole construction process will be much cheaper.
Additionally, autonomous equipment is less prone to mistakes. In fact, a high-quality piece of equipment is essentially mistake-free. Therefore, the speed of the construction process will increase as well.
Similarly, using 3D printers in construction is much quicker than using human labor. A 3D printer can build a whole house in about a day. The same task would take a few experienced workers at least a week. Therefore, contractors will be able to do more jobs, earning much more than if they weren't using 3D printing.
Freedom to Experiment With Unusual Designs
One of the main benefits of 3D printing is the freedom of design it allows. For a long time, construction was held back by what humans could create. If a design is too labor-intensive or expensive to make, it would be quite difficult to get it off the ground.
However, as 3D printing improves, so does the ability to design and make complex constructions. It allows you to optimize the amount of material you will use, so the project ends up costing you less. Additionally, autonomous equipment can take on most of the work and help finish the project quickly.
Potential Difficulties of 3D Printing in Construction
Although there are clear benefits to including 3D printers in the construction process, people are still apprehensive about it. Many are used to living in brick homes and may find it unusual to have their home 3D printed. Potential customers opt out of trying the new technology because they think it's just a gimmick. Because of that, they end up paying more than they have to for the construction materials and the labor involved.
The Future of 3D Printing and Autonomous Construction
The future of automated equipment and 3D printers in construction is bright. 3D printing has already found a home within the design and construction industries. For example, you can use AutoCAD Architecture to make your dream design a step closer to reality.
Luckily, this field shows no signs of slowing down. As 3D printers become more widely available and cheaper to use, you can expect their use to skyrocket in every field. Additionally, as people get used to the idea of living in a 3D printed home, this way of home construction will become more popular.
In Conclusion
3D printing in construction is far from an untapped territory. Quite the contrary, this industry will only expand in the future. There are a lot of 3D-printed bridges, houses, and office buildings already in use.
About the author
Roger Liucci is a building information modeling (BIM) and 3D printing specialist at Microsol Resources, an Autodesk Platinum Partner in their New York office. He is particularly interested in the interaction between design and technology innovation as it relates to digital fabrication and cloud computing where one can work anytime, anywhere and optimize designs with virtually infinite and mobile cloud computing power.
Roger studied Environmental Architecture at Arizona State University and has an Associate Degree in Applied Sciences from SUNY Farmingdale. He has given talks on building information modeling and technology innovation at Autodesk University, and the Revit User Group to name a few.
Comments (0)
This post does not have any comments. Be the first to leave a comment below.
Featured Product
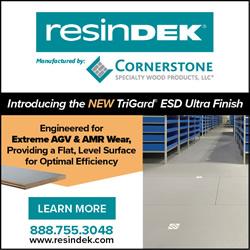